Compartir
Lea a continuación
En los últimos años la influencia de la Industria 4.0 ha abarcado diferentes sectores de la manufactura, y la industria de la inyección de plástico no ha sido la excepción. El proceso de moldeo por inyección de plástico ha sido de gran interés para la adaptación a las nuevas tendencias de la industria 4.0, por la serie de variables que no son fáciles de controlar y que pueden influir en los defectos de la pieza terminada en la etapa del moldeo.
Entre los defectos que se pueden encontrar en la pieza durante el proceso de moldeo por inyección sobresalen rebabas, rechupes, alabeo, porosidad y piezas incompletas. Algunas variables que contribuyen a estas fallas que se pueden monitorear y controlar en el proceso son la temperatura, la presión y la viscosidad.
Tanto los defectos detectados por el área de calidad y los parámetros monitoreados por el área de producción son datos que pueden ser utilizados en su conjunto para obtener un control total del proceso de fabricación mediante el uso de un software de manejo de datos, y para el manejo de esta información se consideran tres niveles: parámetros de la máquina, parámetros en molde y control de calidad de piezas.1 Para llegar a esto y confiar en los datos obtenidos debemos entender las herramientas y los métodos de monitoreo de los parámetros que se tienen. En el caso de los parámetros en molde, comúnmente su control se realiza mediante el uso de sensores de temperatura y de presión. Pero tienen ciertas complicaciones: pueden ser afectados por las altas presiones, la exposición a medios corrosivos, temperaturas extremas y la disposición del sensor en el molde, por lo cual suele presentar dificultades para obtener datos precisos.2 Dentro de los sensores de presión los más comunes están los sensores piezoeléctricos y los sensores de galgas extensiométricas. Entre los sensores de temperatura, los más usados son los termopares de superficie y sensores infrarrojos, pero también se han usado sensores ultrasónicos.
Sensores piezoeléctricos. Utilizan un material como el cuarzo, que al recibir presión generan una carga eléctrica proporcional a la fuerza aplicada. La carga eléctrica es interpretada por un programa y genera el dato de la presión.
Sensores de galgas extensiométricas. Por lo general, conformados por una lámina metálica en un diafragma que al deformarse genera un voltaje directamente proporcional a la presión ejercida sobre el material, y el voltaje se interpreta para obtener el dato requerido. Las galgas extensiométricas son más económicas y tienen un mayor tiempo de respuesta en comparación con los sensores piezoeléctricos.3
Termopares de superficie. Son dispositivos compuestos por dos metales distintos unidos entre sí para generar una diferencia de potencial en proporción al cambio de temperatura entre ellas. El termopar debe estar ubicado sobre la superficie del molde y detectar la temperatura del metal para calcular la temperatura de la masa fundida. Estos sensores funcionan según la propiedad de la conducción del calor, por lo cual dependerán de la pérdida de calor al pasar por el metal antes de llegar al diferencial de potencial, por lo que pueden tener retrasos en la toma de temperatura respecto a la masa fundida, pero por su simplicidad de uso y su facilidad de reposición son ampliamente usados.
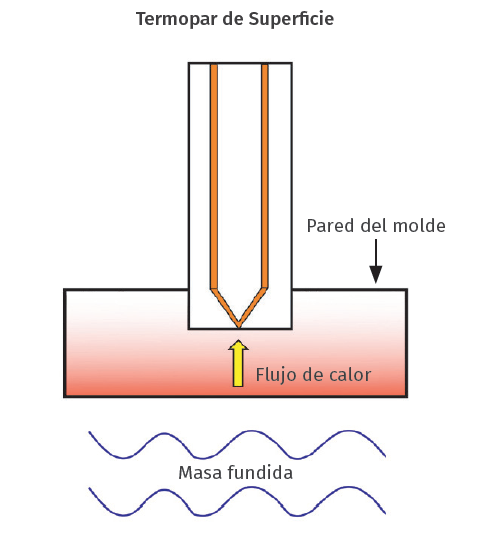
Figura 1. Termopar de superficie.
Sensores infrarrojos. Son detectores de las ondas electromagnéticas que se encuentran en el rango del infrarrojo producido por los objetos calientes. Estos equipos, que pueden detectar la temperatura sin los inconvenientes de la conducción del calor, son más rápidos que los termopares, detectan la temperatura de la masa fundida y pueden medir con mayor precisión las diferentes etapas de la masa fundida en el molde, desde su llenado hasta su apertura. En el mercado se encuentran cámaras infrarrojas que pueden mapear la cavidad del molde, observar los diferentes puntos de temperatura y con estos datos detectar orígenes de fallas como el alabeo.4 También están las sondas de infrarrojo que utilizan una fibra óptica colocada en la cavidad del molde para tomar los datos directamente de la masa fundida y enviar la radiación infrarroja a un detector con el fin de señalar los datos directos del material.5
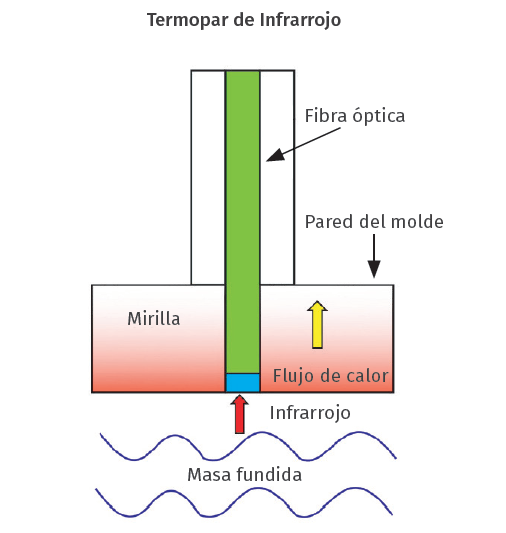
Figura 2. Sensor de infrarrojo.
Sensores ultrasónicos. También se han desarrollado sensores ultrasónicos de temperatura capaces de detectar los cambios de velocidad con la que viaja el sonido en un material, velocidad proporcional a la temperatura a la que se encuentra.6 Recientes investigaciones los confirman como una opción ideal para monitorear la temperatura de los moldes y arrojar mayor información para el análisis7 de fallas de piezas terminadas.8
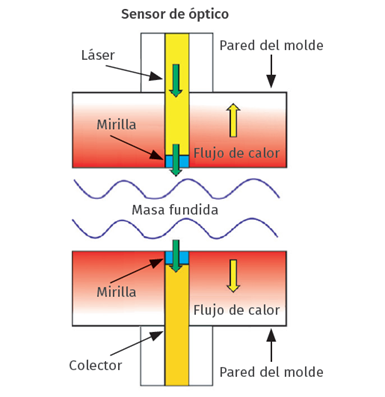
Figura 3. Esquema de funcionamiento del sensor óptico.
Hay más dispositivos en desarrollo para la obtención de datos de los diferentes parámetros durante el proceso del moldeo por inyección, como la viscosidad, sensores de ultrasonido9 y sensores dieléctricos que usan un electrodo dentro de la cavidad.10 También se ha explorado el uso de sensores ópticos para determinar la cristalización del polímero dentro del molde11 o sensores de presión en película fina que permitan colocar varios dispositivos dentro del molde y tener un mapeo de las diferentes presiones de la cavidad.12 Estos sensores serían una parte fundamental en la iteración del proceso y el entramado digital, en la cual un software de manejo de datos podría recolectar, analizar e, inclusive, proponer soluciones a problemas de rechazo del cliente. Por ello, mientras más datos sean recolectados de los tres niveles, parámetros de la máquina, parámetros en molde y control de calidad de piezas, mejor será la toma de decisiones para la resolución de problemas por parte de los usuarios o de una IA.
REFERENCIAS
- Karbasi, H.; Reiser H.; Smart mold: Real-time in-cavity data acquisition. In First Annual Technical Showcase & Third Annual Workshop, Canada; 2006, Citeseer.
- Kazmer, D.O.; Knepper, P.; Johnson S., A Review of In-Mold pressure and Temperature Instrumentation. In Proceedings of the ANTEC 2005, USA, 1–5, 2005, pp. 3300–3304.
- Groleau, M.R.; Groleau, R.J. Comparing Cavity Pressure Sensor Technologies Using In-Mold Data. In Proceedings of the ANTEC 2002: Plastics—Annual Technical Conference, USA, 5–9 May 2002.
- Bula, K.; Róz˙an´ ski, L.; Marciniak-Podsadna, L.;Wróbel, D. The use of ir thermography to show the mold and part temperature evolution in injection molding. Arch. Mech. Technol. Mater. 2016, 36, 40–43.
- Abeykoon, C.; Martin, P.J.; Kelly, A.L.; Brown, E.C. A review and evaluation of melt temperature sensors for polymer extrusion. Sens. Actuators A Phys. 2012, 182, 16–27.
- Ruixi Jia1,2, Qingyu Xiong1,3, a), Lijie Wang1,2, Kai Wang1, Xuehua Shen1, Shan Liang1, and Xin Shi1, Study of ultrasonic thermometry based on ultrasonic time-of-flight measurement, AIP Advances 6, 035006 (2016).
- Wang, H.; Cao, B.; Jen, C.K.; Nguyen, K.T.; Viens, M. On-line ultrasonic monitoring of the injection molding process. Polym. Eng. Sci. 1997, 37, 363–376.
- Fronimidis, D.; Edge, K.A.; Stelson, K.A.; Mileham, A.R.; Sokola, M.A. Use of non-invasive measurements methods to aid the control of part quality in the injection moulding process. Proc. Inst. Mech. Eng. Part B J.Eng. Manuf. Short Commun. Manuf. Des. 2005, X, 1195–1202.
- Ono, Y.; Jen, C.K.; Cheng, C.C.; Kobayashi, M. Real-time monitoring of injection molding for microfluidic devices using ultrasound. Polym. Eng. Sci. 2005, 45, 606–612.
- Chen, X.; Chen, G.; Gao, F. Capacitive transducer for in-mold monitoring of injection molding. Polym. Eng.Sci. 2004, 44, 1571–1578.
- Marinelli, A.L.; Farah, M.; Elida, R.; Bretas, S. Optical monitoring of polyesters injection molding. J. Appl. Polym. Sci. 2006, 99, 563–579.
- Luo, R.C.; Chen, C.M. Pzt thin film pressure sensor for on-line monitoring injection molding. In Proceedings of the 26th Annual Conference of the IEEE Industrial Electronics Society, Japan, 22–28 October 2000; pp. 2394–2399.
Contenido relacionado
Michael Cicco comparte su visión en NPE: el futuro de la automatización
NPE2024 presenta a Michael Cicco, CEO de FANUC America, como conferencista. Compartirá ideas sobre el potencial de la robótica y la automatización en la industria del plástico.
Leer MásAmanco Wavin invierte en dos nuevas plantas de producción en México
Con una inversión de 2.3 MM de dólares Amanco Wavin construirá dos plantas de producción de geosintéticos 3D para fabricación de productos para infraestructura.
Leer MásOportunidades de automatización en la industria del plástico
La automatización es una tecnología en constante avance que les permite a más empresas en la industria del plástico mejorar sus procesos. En este artículo presentamos siete áreas de oportunidad para la automatización y cómo pueden mejorar la eficiencia de su negocio.
Leer MásHasco presenta en Fakuma sus innovaciones para digitalización
Bajo el lema “La digitalización se encuentra en la estandarización”, Hasco presenta sus innovaciones y desarrollos en bases de moldes y canales calientes en Fakuma 2023.
Leer MásLea a continuación
¿Aumentará la automatización en las empresas de plástico luego de la pandemia?
Las razones para incorporar robots y automatizar celdas de producción en las plantas de transformación de plásticos estarán más vigentes que nunca en la pospandemia. Algunos de los principales proveedores de sistemas de automatización compartieron con nosotros su visión del mercado en México y Latinoamérica.
Leer MásCon automatización y robótica, Trademark Plastics aumentó su producción para enfrentar el COVID-19
Enfrentando una alta demanda de insumos médicos, así como la falta de mano de obra, este proveedor automatizó varios de sus procesos de moldeo con robots y sistemas de manipulación de materiales de Wittmann Battenfeld.
Leer MásCambio de paradigma en la inyección de cubetas
StackTeck y Avance Industrial unieron su conocimiento técnico en moldeo por inyección para romper paradigmas en la fabricación de cubetas. Así, demostraron una poderosa combinación de tecnologías de molde, máquina y enfriamiento que les permitió llegar a un ciclo de producción de tan solo 13 segundos para cubetas estándar.
Leer Más