Marshall ADG recurre a Stratasys para imprimir en 3D sus piezas aeronáuticas
La compañía Marshall ADG está utilizando la impresora FDM Fortus 450mc y la resina ULTEM 9085 de Stratasys, para fabricar componentes que cumplen con los estrictos requisitos del sector aeroespacial.
Compartir
Lea a continuación
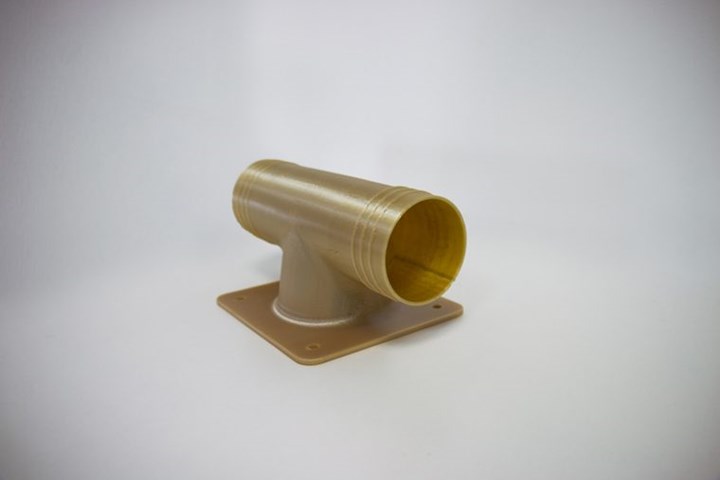
Marshall Aerospace and Defence Group utiliza piezas de conductos impresos en 3D, así como soportes para cuchillos de seguridad e interruptores para interiores de aviones.
Marshall Aerospace and Defence Group está utilizando la tecnología en impresión 3D de Stratasys para la fabricación de piezas para sus aviones militares, civiles y comerciales, así como para producir equipos específicos de operaciones en tierra, con un costo menor que las alternativas de aluminio.
Actualmente Marshall Aerospace and Defence Group es una de las compañías aeroespaciales y de defensa independientes y de propiedad privada más grandes del mundo.
Marshall utiliza piezas de conductos impresos en 3D, así como soportes para cuchillos de seguridad e interruptores para interiores de aviones. La impresión 3D permite a la empresa producir piezas más ligeras que con los métodos tradicionales, en un tiempo considerablemente menor y con un costo más bajo.
Al respecto, Chris Botting, ingeniero de materiales, procesos y fabricación aditiva en Marshall ADG, ha declarado: “Necesitamos un método que pueda producir un conducto preciso, complejo, funcional y ligero de forma eficiente con costes mínimos de herramientas y la impresión 3D encaja a la perfección. Pero también tenemos que asegurarnos de que el conducto será aprobado para el vuelo por la EASA”, explica Botting.
“Por eso estamos utilizando la impresora FDM Fortus 450mc y la resina ULTEM 9085 de Stratasys, un material de impresión 3D robusto pero ligero con una gran resistencia térmica y química. Este planteamiento ha sido decisivo para cumplir con los requisitos estrictos de nuestro sector, ya que ahora podemos imprimir piezas en 3D que cumplen los requisitos de las propiedades FST (llamas, humo y toxicidad) para su uso en el interior de los aviones”, aseguró.
La empresa utiliza también la impresora 3D Fortus 450mc adquirida a través de SYS Systems, colaborador Platinum de Stratasys Reino Unido e Irlanda, para crear piezas finales para uso en operaciones de tierra. Marshall ha realizado recientemente un prototipo de adaptador de conducto para equipo de operaciones en tierra, fundamental para proporcionar aire fresco que refrigere los componentes del aparato. La impresión en 3D de esta pieza concreta ha ayudado a Marshall a dejar atrás los costosos procesos estándares del aluminio.
“Antes de empezar con el costoso mecanizado del aluminio, utilizamos la Fortus 450mc para imprimir en 3D un prototipo con material ASA”, comenta Botting.“Esto nos permitió crear un prototipo funcional y preciso del componente complejo que después pudimos imprimir en 3D en material Nylon 12 en vez de utilizar el método más convencional del mecanizado a partir del aluminio. El conducto impreso en 3D supuso una considerable rebaja de costos en comparación con el mecanizado de la pieza a partir de aluminio, así como una reducción del 63% en el peso total”.
El grupo también utiliza impresoras 3D de Stratasys para una variedad de complejas aplicaciones de herramientas que incluye guías de taladrado, modelos de protecciones, fijaciones unidas y herramientas de moldeo en material composite.
El equipo produce regularmente tiradas pequeñas de herramientas de producción personalizadas tan solo 24 horas después de la petición del ingeniero. De hecho, están promoviendo el uso de herramientas de termoplástico impresas en 3D para sustituir las pesadas herramientas metálicas, lo que reduce la carga para el operador y, sobre todo, el coste y los plazos de entrega para las tareas operativas urgentes.
Botting prevé que el uso de la fabricación aditiva FDM de Stratasys aumente en todos los elementos del negocio y que se promuevan nuevas aplicaciones.
“La tecnología FDM ha cambiado nuestra forma de trabajar y las impresoras y materiales 3D para el sector aeroespacial nos permiten cumplir los plazos cada vez más ajustados y los complejos requisitos de fabricación.
“En el futuro, no cabe duda de que la impresión 3D seguirá teniendo un importante efecto en la forma en que diseñamos y fabricamos en nuestra empresa”, concluyó Botting.
Contenido relacionado
Hacia dónde va la innovación en plástico para la industria automotriz
Conozca cuáles son las principales tendencias que moldearán el uso de plásticos y materiales poliméricos en aplicaciones para la industria automotriz. Platicamos con expertos sobre el tema para presentar aquí las claves de los desarrollos en autopartes que veremos en los próximos años.
Leer MásNPE 2024: impresión 3D y su impacto en la industria de plásticos
La manufactura aditiva fue protagonista en NPE 2024 con tecnologías avanzadas en impresión 3D, optimizando la creación de moldes y piezas para diversas aplicaciones.
Leer MásRE-cycleo: programa de reciclaje para piezas plásticas impresas en 3D
Sculpteo, compañía del grupo BASF, anunció la creación de RE-cycleo, programa de reciclaje para piezas impresas en 3D y residuos posindustriales de Nylon PA12 y Nylon PA11.
Leer MásManufactura aditiva: nuevas posibilidades en inyección de plástico
La calidad de las superficies inyectadas utilizando canales calientes representa desafíos para la impresión 3D como alternativa para la fabricación de los canales de flujo dentro del distribuidor. Descubra cómo la manufactura aditiva contribuye en el moldeo por inyección multicomponente.
Leer MásLea a continuación
Innovación en empaques de pared delgada: tecnología y sostenibilidad
El mercado global de envases de pared delgada está en constante evolución y abarca una amplia gama de aplicaciones y materiales. En el presente artículo exploraremos este mercado, su crecimiento, tendencias emergentes, impacto de la pandemia por COVID-19 y sus proyecciones para los próximos años según un reciente estudio publicado por Mordor Intelligence.
Leer MásOportunidades de la Industria 4.0 para la nueva normalidad en México
La pandemia ha generado graves afectaciones en diversas actividades y sectores económicos de todo el mundo. Sin embargo, detrás de esos problemas llegaron grandes oportunidades, como la adopción acelerada de la digitalización y la diversificación del portafolio de muchas empresas. Aquí la Industria 4.0 tiene mucho que ofrecer.
Leer MásAsí van las proyecciones en economía circular para los plásticos
¿Qué tan cerca estamos de alcanzar la meta de lograr empaques plásticos 100 % reusables, reciclables y compostables para 2025? ¿Qué acciones vienen en curso para cumplirlas? Entrevista exclusiva con la Fundación Ellen MacArthur sobre el panorama de los plásticos en la economía circular en el mundo y en América Latina.
Leer Más