6 factores clave para evaluar un sistema de colada caliente
Aprenda cómo seleccionar un sistema de colada caliente que satisfaga las necesidades de fabricantes de moldes y moldeadores por inyección para mejorar la calidad y reducir costos.

Este sistema de colada caliente de cuatro puntos tiene resistencias tubulares compactadas.
Crédito: Foto cortesía de Incoe Corp.
Los fabricantes de moldes y los moldeadores por inyección tienen diferentes requisitos en lo que respecta a los sistemas de colada caliente. Los fabricantes de moldes a menudo se preocupan por el precio, la entrega y la calidad, mientras que el moldeador se preocupa por la operación, el desempeño y la facilidad de mantenimiento.
Sin embargo, tanto el fabricante de moldes como el moldeador deben ser parte del proceso de toma de decisiones al considerar un sistema de colada caliente y al proveedor para garantizar la mejor selección de las opciones de sistema disponibles y para optimizar la integración del sistema en el molde.
Aquí hay seis puntos importantes que se deben considerar al evaluar un sistema de colada caliente:
1. Resistencias del manifold (distribuidor)
Para la instalación, la mayoría de los fabricantes usan una prensa. Si el contacto de la resistencia con el distribuidor no es uniforme, se crearán puntos calientes en la resistencia, lo que ocasionará una falla prematura y un calentamiento no uniforme del distribuidor. Además, la capacidad del proceso puede verse afectada especialmente con algunos materiales de ingeniería, ya que su viscosidad puede ser más sensible a la temperatura que las resinas básicas como el polipropileno y el polietileno.
2. Resistencias de la boquilla
La medición de la resistencia en ohms para cada resistencia o calentador de la boquilla puede proporcionar buena información al solucionar problemas del sistema de colada caliente. Una variación demasiado grande puede evitar perfiles de temperatura uniformes y aumentará la posibilidad de variación del proceso. Además, la vida de una resistencia con menos eficiencia se reduce debido al aumento requerido en la carga de trabajo.
3. Orificio de la punta de la boquilla
Las diferencias de presión en el moldeo por inyección de plástico se definen en la ecuación de Hagen Poiseuille, donde (Q) es la tasa de flujo, (l) es la longitud de la colada, (n) es la viscosidad del material y (r) es el radio del canal de flujo: ΔP = (8Qln) / (πr4)
La ecuación muestra que cualquier pequeña diferencia en el valor "r", que incluye el orificio en la boquilla de colada caliente y el punto de inyección, se ve afectada a una magnitud de la cuarta potencia. Esto significa que un pequeño cambio en el radio dará como resultado una diferencia bastante grande en la caída de presión desde un punto de inyección a un punto de inyección.
La percepción común es que si los puntos de inyección están todos dentro de la tolerancia, esto no tendrá importancia. Sin embargo, es importante preguntar cuál es la tolerancia aceptable junto con las dimensiones del punto de inyección. El hecho de que estén dentro de la tolerancia no significa que no haya una diferencia en la caída de presión.
Por ejemplo, una tolerancia de +/- 0.002 pulgadas en un diámetro del punto de inyección de 0.300 pulgadas puede ser demasiado grande como rango de tolerancia para lograr un moldeado consistente. Por supuesto, un procesador puede ajustar las temperaturas individuales de la punta para tratar de superar algunas de estas variaciones.
Es importante entender que al hacer esto, el procesador está cambiando las condiciones del material a partir del cual se están moldeando las piezas. Si el procesador procesa materiales semicristalinos, entonces él o ella pueden crear más problemas con las diferencias de cristalinidad cerca del punto de inyección frente a otras áreas de la pieza.
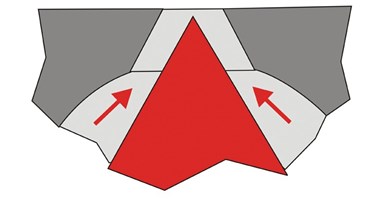
Figura 1a. Esta imagen muestra la ubicación después de una expansión térmica adicional. Observe que el canal de flujo efectivo es menor aquí.
Crédito: Imágenes cortesía de Beumont Technologies y AIM Institute.
Además, las variaciones resultantes en la expansión térmica de la boquilla y el distribuidor de acero que ocurren debido a los diferentes ajustes de temperatura podrían conducir a otras variaciones de llenado, problemas de fugas o rupturas. Por ejemplo, si una cavidad se está llenando detrás de otras cavidades, un procesador puede aumentar la temperatura de la boquilla que alimenta esa cavidad.
Sin embargo, ese aumento de temperatura podría llevar el punto de inyección más adentro del orificio de la inyección debido a la expansión térmica adicional. Esto reduce el radio efectivo (r), en última instancia, restringe el flujo y contrarresta la intención del aumento de la temperatura (ver Figuras 1a y 1b).
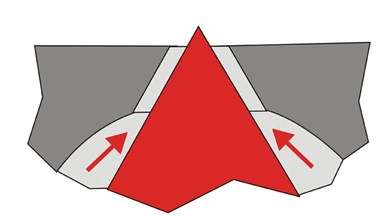
Figura 1b. La posición natural de la punta caliente con la expansión térmica esperada.
Crédito: Imágenes cortesía de Beumont Technologies y AIM Institute.
También es importante comprender que el aumento de la temperatura de la boquilla local o del distribuidor puede causar un aumento en el tiempo del ciclo ya que el material y el molde en esa región permanecerán más calientes durante un período más prolongado.
4. Espesor
Es importante verificar la uniformidad de la altura en todas las puntas de las boquillas (ver Figura 2). Si estas dimensiones varían, entonces el acoplamiento con el punto de inyección también variará, y estas variaciones podrían afectar la capacidad del proceso debido a las diferencias resultantes en la geometría del canal. Solicite el informe de inspección y consulte al proveedor del distribuidor para obtener una tolerancia aceptable.
Figura 2. Comprobar la uniformidad de la altura de las puntas de las boquillas es importante para evitar los problemas de puntos de tolerancia de espesor que se muestran aquí.
Crédito: Imágenes cortesía de Beumont Technologies y AIM Institute.
Revise la ecuación de caída de presión para ver si la tolerancia que proporciona el proveedor es aceptable para un determinado proceso y conjunto de partes.
5. Canales de flujo
Todos los fabricantes de taladros de pistola reclamarán variaciones de 0.001 pulgadas por pulgada de recorrido. Compruebe que puedan verificar que la perforación cruzada de los canales de flujo no deja un paso en la intersección de las coladas con perforación cruzada.
Consulte la ecuación anterior nuevamente. Verifique que el fabricante del taladro alcance y ajuste los canales. Las variaciones en los canales de flujo podrían crear diferencias en la caída de presión a través de las regiones de un distribuidor. De nuevo, esto se refiere a la porción de la ecuación que implica el radio (r), que se eleva a la cuarta potencia.
Los escalones en el canal de flujo pueden crear puntos muertos, que no se limpian bien al purgar y causan problemas de cambio de color y problemas de degradación de material. Además, los escalones hacen posible que el material se asiente en el distribuidor durante períodos prolongados, lo que aumenta la probabilidad de degradación térmica del polímero.
La ruta de flujo natural del polímero alrededor de las intersecciones del canal también causan estas áreas muertas. Esto sucede incluso si las intersecciones de los canales están perfectamente alineadas (ver Figura 3).
Figura 3. La ruta de flujo natural del polímero a través de una colada ramificada y alrededor de una esquina se muestra en rojo. Las posibles ubicaciones estancadas se indican en azul.
Crédito: Imágenes cortesía de Beumont Technologies y AIM Institute.
6. Costo del sistema
El costo del sistema suele ser una de las cosas más importantes a tener en cuenta, pero confiar únicamente en las cotizaciones de varios proveedores no es la mejor manera de abordar el problema. La familiaridad con las diversas opciones que ofrece cada proveedor de colada caliente es útil.
Por ejemplo, algunos proveedores pueden proporcionar la capacidad de separar el distribuidor del molde mientras el molde está todavía en la máquina de moldeo, lo que reduce el mantenimiento y el tiempo de inactividad. Otra cosa en que pensar es cómo se fabrican los canales.
El método de fabricación puede afectar los cambios de color y requerir procedimientos de limpieza adicionales que amplíen los enfoques de purga tradicionales. (Consulte la barra lateral para ver una lista de los costos directos e indirectos comunes al evaluar el sistema en general).
A menudo se dice que todo está en los detalles, y esto ciertamente se aplica a la evaluación y el desempeño del sistema de colada caliente. Surgen problemas, por lo que es importante estar al tanto de algunos desafíos comunes y posibles fuentes de variación, incluidas las altas presiones en los puntos de ensamble, la convivencia con un molde y platinas frías, problemas de puntos de inyección (enfriamiento, obstrucción, babeo, encordado), nivel de habilidad del procesador, tamaño de disparo, tiempo de residencia, fugas (consulte la Figura 4), asentamiento de pasadores de válvula, desequilibrios de flujo de corte, consumo de energía y colocación y contacto de termopares.
Figura 4. Este distribuidor con fugas causó que el plástico encerrara el cableado de la colada caliente.
Crédito: Imágenes cortesía de Beumont Technologies y el Instituto AIM.
Tomar una decisión más informada requiere un conocimiento profundo del diseño, el proceso de fabricación y las opciones disponibles del sistema de colada caliente. También requiere una sólida comprensión de los estándares de resolución de problemas y experiencia en molde. Mantenerse al tanto de los elementos descritos en este artículo reducirá el tiempo de inactividad, mejorará la calidad de la pieza y disminuirá los costos generales.
¿Cuánto me costará una colada caliente?
Obtener precios de proveedores es solo el comienzo. También considere estos costos directos e indirectos.
Costos Directos
- Sistema de colada caliente: número en la hoja de presupuesto.
- Costos y plazos de entrega para el reemplazo de refacciones, incluyendo puntas, resistencias, termopares y boquillas.
- Controlador para el sistema de colada caliente y los componentes y conexiones asociados
Costos Indirectos
- Facilidad de mantenimiento, enfoque de mantenimiento e historial de problemas.
- Tiempo de residencia y efecto en la estabilidad del proceso y calidad de la pieza.
- Cambios de color: tiempo, material y compuestos de purga.
- Variación de la temperatura en toda la producción, creando tiempo de inactividad adicional, desperdicios y otros problemas.
- Requisitos de capacitación y demanda de un mayor nivel de habilidad en procedimientos adecuados para mantener, arrancar y apagar un sistema de colada caliente.
Contenido relacionado
Meximold 2023: la vanguardia en moldeo de plásticos vuelve a Querétaro
Llegó la hora de vivir la experiencia más completa en todo lo relacionado con tecnologías para manufactura de moldes y transformación de plásticos. Meximold, en su cuarta edición, reunirá a los líderes de la industria de moldes, troqueles y herramentales en Querétaro. Regístrese sin costo y sea testigo de las últimas tendencias y equipos en moldes, troqueles y herramentales.
Leer MásMeximold 2024: la feria líder en moldes y moldeo regresa a Querétaro
Meximold 2024 se llevará a cabo los días 9 y 10 de octubre en el Querétaro Centro de Congresos, con la participación de más de 140 compañías expositoras, un programa de conferencias de alto nivel y oportunidades de networking y negocios B2B.
Leer MásHasco celebra apertura de oficina en Colombia
Hasco inauguró su oficina en Bogotá, Colombia, con el objetivo de brindar soporte comercial y técnico a sus clientes de la región Andina y Centroamérica.
Leer MásChecklist para la fabricación exitosa de moldes inyección de plástico
Una guía integral sobre cómo optimizar el proceso de diseño y construcción de moldes de inyección de plástico, centrada en la prevención de problemas y la mejora continua.
Leer MásLea a continuación
Reduzca los tiempos de paro de los sistemas de colada caliente
Instrucciones prácticas para solucionar sus problemas con sistemas de colada caliente rápidamente y mediante un enfoque sistemático.
Leer MásSistemas de colada caliente: más inteligentes y especializados
Ahora, la tecnología de canales calientes incorpora funcionalidades enfocadas en la aplicación que se va a moldear. Así mismo, también se está volviendo más inteligente, al compartir datos y reaccionar a la retroalimentación de la máquina. Esto y más se verá en NPE2018.
Leer MásSistema de colada caliente con boquilla roscada para protección de fugas
El sistema de colada caliente H4016, de Hasco, tiene una boquilla roscada que asegura una operación libre de filtraciones.
Leer Más