Pines de expulsión en moldes: fuerza, fricción y acabado superficial
Conozca cómo las fuerzas, la fricción, el acabado superficial y la lubricación pueden influir en la ruptura de los pines de expulsión de los moldes.
Compartir
Lea a continuación
Nota del editor: Esta es la tercera parte de un especial con cuatro entregas. Puede encontrar las ligas de la serie completa a continuación:
Parte 1: máquina de moldeo y sistema de expulsión.
Parte 2: cuándo y cómo reducir longitud no soportada de los pernos.
Parte 3: fuerzas, fricción, acabado superficial y lubricación.
Además de las posibles causas de ruptura discutidas en las dos primeras partes de esta serie (Parte 1 y Parte 2), existen otras dos razones comunes: (1) la fuerza requerida para expulsar la parte excede la resistencia del pin y (2) desgaste adhesivo.
La fuerza requerida para iniciar el avance de los pines de expulsión se controla mediante la fricción estática más la adhesión de la pieza al núcleo. Las fuerzas de fricción estáticas suelen ser más altas que las fuerzas de fricción cinéticas, que son las fuerzas necesarias para mantener los pines en movimiento una vez que han comenzado a moverse.
Para minimizar el impacto inicial, tanto en los pines como en las piezas, la velocidad de expulsión debe comenzar relativamente lenta. Después de aproximadamente 1/8 pulgadas de recorrido puede aumentar la velocidad de expulsión hasta el valor deseado.
Varios factores pueden hacer que un pin expulsión colapse
La mejor manera de evitar esta falla es usar pines con el mayor diámetro posible y una cantidad suficiente de ellos. Desafortunadamente, los pines de expulsión pueden limitar la capacidad para ubicar los canales de enfriamiento de manera ideal, por lo que a menudo se debe hacer un compromiso.
En cualquier caso, nada aumenta la cantidad de fuerza requerida para extraer una parte más que una condición de sobre compactación, especialmente si hay una gran cantidad de área superficial vertical mecanizada en el núcleo, como venas de refuerzo delgadas y profundas.
La fuerza requerida para expulsar la pieza puede llegar a ser más que la resistencia del propio plástico y los pines de expulsión podrán atravesar la pieza. Nota: los pines de gran diámetro son beneficiosos cuando se intenta expulsar piezas muy delgadas y de paredes muy gruesas. Un pin pequeño puede dentar, perforar o dejar una marca de tensión en una parte débil y de pared delgada.
Puede hacer lo mismo con las partes de paredes gruesas, que a menudo se encuentran muy calientes y suaves en el centro al expulsarlas. En ambos casos, los tiempos de ciclo aumentan simplemente porque los pines de expulsión son demasiado pequeños.
Si su máquina de moldeo le permite limitar la cantidad de fuerza de expulsión que actúa sobre la placa de expulsión, es una buena idea establecer un valor algo mayor que el requerido para expulsar las piezas en condiciones normales de operación.
Limitar la fuerza de expulsión puede ahorrarle mucho tiempo y dinero en caso de que haya un problema con un pin de expulsión. La máquina puede interrumpir el ciclo y evitar daños adicionales. Es muy efectivo cuando se puede vincular el valor de la fuerza de expulsión a una alarma en su máquina, de la misma manera que lo haría con el tiempo total del ciclo o el tiempo de plastificación.
Si el valor de la fuerza no se puede monitorear, quizás el tiempo de detección si, lo cual es casi igual de efectivo. Tal vez algún día un programa de simulación podrá calcular la fuerza necesaria para expulsar una pieza moldeada, de modo que podamos determinar con precisión el tamaño y la cantidad de pines de expulsión necesarios.
Dada la interminable lista de variables, como la geometría de la pieza, las características del material, los ángulos de desmoldeo, el acabado superficial, las presiones de sostenimiento, la temperatura del molde, la ubicación del punto de inyección, contra salidas, etc; dudo que podamos ver un programa así en el futuro.
Sin embargo, Torsten Kruse, presidente de Kruse Analysis Inc. y experto en análisis de flujo de plástico, señala que “algunos programas de software CAE pueden dar a los diseñadores de moldes una idea de dónde colocar los pines de expulsión basándose en el cálculo de la contracción diferencial de una pieza y las fuerzas internas asociadas”. “Los pines de expulsión pueden romperse debido a la contracción diferencial de la pieza que requiere fuerzas diferentes o desiguales en los diferentes pines de expulsión”.
Basado en la declaración de Kruse, cada pin de expulsión probablemente va a requerir una fuerza diferente para expulsar la pieza. Por ejemplo, los pines cercanos al punto de inyección, una esquina interior o en la parte inferior de una costilla profunda, probablemente requerirán más fuerza que los pines en la colada fría o al final del llenado. Esto debe tenerse en cuenta al decidir la ubicación, el tamaño y la cantidad de los pines de expulsión.
Para más información sobre este tema, hay un artículo en SPE ANTEC de 2001 titulado “Friction Properties of Thermoplastics in Injection Molding”, escrito por Ferreira, Nerves, Muschalle y Pouzada de la Universidad de Minho en Braga, Portugal. Es una lectura interesante tanto para los diseñadores de moldes como para los procesadores.
El desgaste adhesivo es una forma de desgaste causado por la adhesión y la fricción cuando dos metales se deslizan uno contra el otro. La condición aumenta si hay una carga lateral que comprime las dos superficies, como cuando un pin de expulsión no está perfectamente alineado con el orificio pasante del núcleo.
Se ejerce más presión en un lado del agujero que en el otro. A menos que un pin de expulsión esté ajustado para una orientación específica, debe poder girarlo libremente cuando las placas de expulsión estén totalmente hacia adelante.
Esto confirma que las líneas de centro de los pines son paralelas, que se alinean con los orificios pasantes en el núcleo y que hay suficiente espacio alrededor del eje y cabeza del pin.
El aspecto adhesivo del desgaste hace que la estructura cristalina del material se resbale y se rasgue, depositando o soldando partículas microscópicas en la superficie adyacente.
A diferencia de otras formas de desgaste, el desgaste adhesivo se produce rápidamente. Por lo tanto, si escucha un chirrido o sonido agudo metálico del pin expulsor, deténgase. No va a mejorar si continua operando la máquina.
El aspecto de fricción del desgaste adhesivo es relativo al tipo y dureza del material. Esta es la misma razón por la que se suele usar diferentes tipos de acero y al menos un diferencial de dureza Rockwell de 10 puntos en superficies deslizantes o en ángulo. El diferencial de dureza es el factor predominante. Cuanto más duro es el acero, o al menos la superficie del acero, menos propenso será a la abrasión.
Si puede rayar el lado de un pin expulsor con una lima de mano que, según mi experiencia, no es tan raro en moldes construidos en algunos países asiáticos, es probable que no deba esperar a ver si se bloquea. Solo acepta el hecho de que eventualmente lo hará y reemplázalo ahora.
Cuando una máquina de moldeo entra en alarma, siempre revise si hay un pin de expulsión roto o sobresaliendo.
Ciertos metales son propensos al desgaste debido a su estructura atómica, especialmente aquellos con altos coeficientes de fricción, como el aluminio, el titanio y, hasta cierto punto, el acero inoxidable. Por el contrario, las aleaciones como el latón o el bronce son muy resistentes al desgaste adhesivo, aunque son mucho más suaves.
A lo largo de los años, varios proveedores de componentes de moldes han ofrecido pines de expulsión hechos de diversos materiales, como H-13, M-2, inoxidable 420 y aleaciones de cobre. Los pines de nitruro H-13, o pines con recubrimientos superficiales duros, Son una excelente opción para reducir la posibilidad de desgaste adhesivo, ya que su dureza superficial es de 65 a 74 Rockwell C.
Los pines de acero inoxidable y los que tienen un fino revestimiento de cromo son adecuados para aplicaciones médicas, de contacto con alimentos y otras aplicaciones en las que restos de grasa u oxidación pueden contaminar las piezas. Los pines cromados no son adecuados para temperaturas extremadamente altas o materiales corrosivos como el PVC rígido.
Tengo algo de experiencia con pines de expulsión de acero inoxidable y no es buena, debido a que son propensos al desgaste adhesivo. Si bien muchos moldeadores usan pines en el núcleo hechos de aleaciones de cobre, hay muchos beneficios de usarlos también como pines de expulsión. Tienen excelentes propiedades de transferencia de calor y son muy resistentes al desgaste.
Desafortunadamente, el precio no es uno de sus beneficios. Al seleccionar qué tipo de pines de expulsión usar, también considere que elemento se va a desgastar o corroer primero: el pin o el núcleo. Reemplazar un pin expulsor desgastado o corroído es mucho más barato que reparar un orificio pasante en un núcleo.
A diferencia de otras formas de desgaste, el desgaste adhesivo se produce rápidamente
El mantenimiento preventivo de los pines de expulsión es tan importante como el mantenimiento de las cavidades y los núcleos. Después de todo, los pines también funcionan en cierta medida como los canales venteo. Deben ser limpiados, lubricados y, dependiendo del material que se inyecta, neutralizados. Los gases corrosivos no tardan mucho en atacar los pines, acelerando el desgaste e incrementando las posibilidades de que se quiebren o rompan.
Un pin bloqueado causado por desgaste adhesivo es un dolor de cabeza para los moldeadores. Si tiene suerte y el pin tiene un diámetro bastante grande, es posible que las placas expulsoras no se extiendan o retraigan completamente, lo que debería hacer que la máquina se detenga y se active la alarma. Eso es suponiendo que tienes unida la placa expulsora al control de la máquina. Si no corres con suerte y el pasador tiene un diámetro bastante pequeño, el pasador se doblará y se romperá dentro del alojamiento de expulsión.
Esto permitirá que las placas se extiendan y retraigan completamente, dejando una parte del pasador roto que sobresale más allá de la línea de unión. Si la seguridad de cierre de baja presión se configuró correctamente, es posible que no se generen mayores daños en el molde cuando se vuelva a cerrar durante el siguiente ciclo automático.
Si la máquina entra en alarma, la falta de entrenamiento, experiencia o agudeza en lo obvio puede hacer que alguien pase por alto el pin sobresaliente y dañe aún más la cavidad al aumentar el ajuste de cierre de baja presión o, peor aún, pasar al modo manual y cerrar el molde con alta presión.
Las velocidades de expulsión y retracción de alta velocidad aumentan el riesgo de desgaste debido al aumento del calor por fricción. Obviamente, los impulsos o repeticiones múltiples en la expulsión y los recorridos excesivos del expulsor agravan el problema.
Para estar tranquilos, algunos procesadores siempre usan una expulsión adicional para expulsar la pieza. Nunca he estado de acuerdo con ese enfoque. Para mí, es como hacer un hueco para tapar otro hueco. Si hay un problema con la expulsión de la pieza, corríjala.
La probabilidad de desgaste puede reducirse en gran medida con una lubricación adecuada. De hecho, el coeficiente de fricción para una superficie lubricada es cuatro veces más bajo que para una superficie seca.
Los proveedores de componentes de moldes ofrecen pernos con varios tipos de recubrimientos lubricantes, como cromo denso, disulfuro de molibdeno, DLC (carbono tipo diamante), disulfuro de tungsteno (WS2), nitruro de titanio (TiN), óxido negro y lubricante seco Dicronite.
Los pines recubiertos con disulfuro de tungsteno no se recomiendan para piezas claras o de colores claros, ya que pueden causar decoloración. He visto esto varias veces con piezas médicas en PC. Además de sus características lubricantes, algunos de estos recubrimientos también tienen la ventaja de ser extremadamente duros.
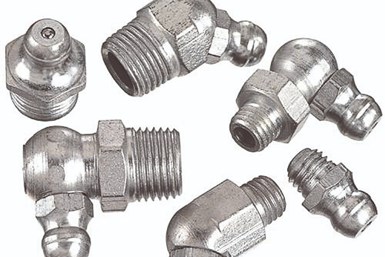
Los proveedores del recubrimiento DLC afirman que los pines con este recubrimiento no requieren lubricación alguna, lo que es ideal para aplicaciones médicas y de contacto con alimentos.
Algunos de estos recubrimientos pueden soportar altas temperaturas, lo cual no pueden hacer otros. Por lo tanto, elija el recubrimiento que mejor se adapte a su aplicación. La probabilidad de desgaste también puede reducirse para cualquier tipo de pin o recubrimiento asegurándose de que haya un enfriamiento adecuado en el núcleo, porque cuando el metal se calienta, se expande.
Los bujes guía de la placa de expulsión tampoco son ajenos al desgaste. Algunos bujes tienen ranuras internas para grasa y una depresión anular externa. Hay un pequeño orificio pasante en el lado del buje que conecta estos dos elementos. El propósito de este orificio es permitir que la grasa sea bombeada hacia el buje mientras el molde aún está en la máquina.
Una pistola de engrase se conecta a un acople Zerk, que está conectado en el borde de la placa de expulsión. La grasa fluye por un orificio o canal perforado que conduce hasta el diámetro exterior del buje guía. No es necesario que el buje esté enclavado u orientado para que la grasa se desplace hacia las ranuras internas de grasa.
¿Qué es un acople Zerk?
Oskar Zerkowitz emigró de Austria a los EE. UU. y cambió su nombre a Oscar Ulysses Zerk. Tiene más de 300 patentes, una de las cuales era un accesorio de engrase conocido como "The Zerk". En el momento de su muerte en 1968, se estimaba que 20 mil millones de estos accesorios habían sido fabricados. Eso fue hace 50 años. Me pregunto cuál es ese número hoy.
Pero para dar crédito donde se debe, fue Arthur Gulborg en Alemite Die Casting Co. quien inventó la primera grasera hueca con bola y resorte en 1916. En 1924, Alemite compró Allyne-Zerk Co. y continuó fabricando ambas versiones de graseras.
En 1933, Joe Bystricky inventó una versión modificada que es básicamente el estilo que todavía se usa en la actualidad. Por el motivo que sea, el nombre de Oscar Zerk sigue asociado a este dispositivo único.
Varias empresas de suministro de moldes ofrecen bujes guía auto lubricados y taponados con grafito. El grafito es una forma alotrópica del carbono. A medida que las placas de expulsión se mueven, los rastros del grafito cubren la superficie del pin guía.
Estos bujes funcionan bien, particularmente en aplicaciones médicas o de contacto con alimentos donde los lubricantes externos están prohibidos. Pero si el material de moldeo produce gases corrosivos, la longevidad de estos bujes auto lubricados puede verse comprometida.
Y si los bujes se lubrican deficientemente, sea con grasa o aceite, su longevidad también disminuirá rápidamente. Solo asegúrese de usar el diámetro y la cantidad adecuados de bujes guía, auto lubricados o no, para soportar el peso de las placas de expulsión. Si la carrera de expulsión es muy larga, a menudo es aconsejable que los bujes guía se extiendan hacia la placa opuesta, de modo que estén apoyados en ambos extremos, en lugar de quedar en voladizo desde un solo extremo.
Es normal que dos componentes que se froten entre sí tengan menos fricción si sus superficies son suaves o lisas en lugar de rugosas. Según el fabricante y el tipo de pin de expulsión, el acabado de la superficie puede ser tan bajo como 2 micro-in, o tan alto como 0 micro-in. Incluso este último es más que adecuado para la mayoría de aplicaciones de moldeo, aunque si está llegando a más de un millón de ciclos al año, un acabado más fino puede ayudar a extender su intervalo de mantenimiento preventivo.
El método más común para instalar un orificio pasante en un núcleo para un pin de expulsión es perforar y luego escariar el orificio. El acabado superficial de un orificio escariado generalmente será suficiente para la mayoría de los moldes. Anteriormente, muchos talleres de moldes pulían los agujeros después de escariar para obtener un tamaño más preciso y un acabado de superficie más fino. Una piedra de pulido gira en el orificio y se mueve hacia adentro y hacia afuera. Esto deja un patrón que ayuda a retener una fina película de lubricante.
El desgaste adhesivo puede reducirse considerablemente con una lubricación adecuada
Hoy en día, cuando el tamaño o acabado superficial debe ser más finos que los de un agujero escariado, se suele utilizar una rectificadora de plantilla o EDM de alambre. Ambos métodos tienen una excelente posición, diámetro y precisión circular de hasta un par de décimas de pulgada. Esto es importante cuando se tiene que instalar un pin cerca del borde de una pared lateral, o precisamente en el centro de una costilla delgada.
Recomiendo usar cualquiera de estos dos métodos cuando hay una gran cantidad de pines expulsores pequeños en un molde, simplemente porque las leyes de probabilidad predicen que al menos uno de ellos causará un problema.
El método de electroerosión por alambre presenta una ligera ventaja: deja picos y valles muy finos, paralelos al eje central del pasador de expulsión. Estos picos y valles ayudan a retener los lubricantes, así como a reducir el área de contacto superficial en el pasador de expulsión, lo que a su vez reduce el calor por fricción.
El proceso de EDM por alambre es más costoso que escariar un agujero. Para ayudar a reducir ese costo, realice una perforación previa entre 0.002 a 0.004 pulgadas más pequeño que el tamaño final deseado.
Así, el proceso de EDM solo tiene que hacer uno o dos cortes de precisión. La tabla en la página 39 muestra el rango de valores de rugosidad promedio para varios tipos de operaciones de mecanizado. Dependiendo de una serie de factores, cada rango podría ser más burdo o más fino que los enumerados en la tabla.
Lea a continuación Parte 4: longitud de los rodamientos.
Acerca del autor
Jim Fattori
Jim Fattori es un moldeador de inyección de tercera generación con más de 40 años de experiencia en moldeo. Es el fundador de Injection Mold Consulting LLC, y también es ingeniero de proyectos para una gran moldeadora de múltiples plantas en Nueva Jersey. Contacto: jim@injectionmoldconsulting.com; injectionmoldconsulting.com.
Contenido relacionado
Qué son los sistemas de colada caliente y cómo funcionan
Un experimentado transformador de plásticos aborda los beneficios, las mejoras y los problemas cotidianos de las coladas calientes, luego de trabajar por décadas con varias marcas en el mercado de estos sistemas.
Leer MásRetos y soluciones en el moldeo de canal caliente
Descubra cómo maximizar la eficiencia en el moldeo de canal caliente. Aprenda técnicas para reducir residuos, identificar fugas y evitar costosas reparaciones.
Leer MásChecklist para la fabricación exitosa de moldes inyección de plástico
Una guía integral sobre cómo optimizar el proceso de diseño y construcción de moldes de inyección de plástico, centrada en la prevención de problemas y la mejora continua.
Leer MásMoldes para plásticos: tecnologías emergentes en impresión 3D
Descubra cómo aborda la industria del plástico el desafío de lograr la textura y suavidad requeridas en las cavidades de molde y conozca soluciones innovadoras para garantizar la viabilidad y eficacia de la manufactura aditiva en la creación de moldes de alta calidad.
Leer MásLea a continuación
Cuándo y cómo reducir longitud no soportada de los pernos en moldes
Nota del editor: Esta es la segunda parte de un especial con cuatro entregas.
Leer Más¿Funcionan realmente los mantenimientos preventivos programados para sus moldes?
El verdadero mantenimiento preventivo reside en monitorear y contar con precisión los problemas y las acciones correctivas en el tiempo. ¿Usted lo está haciendo?
Leer MásPor qué se rompen los pines de expulsión en los moldes: máquina y sistema
Hay decenas de razones por las que los pines de expulsión se rompen. Muy pocas de ellas tienen algo que ver con los propios pines. En esta primera entrega discutiré cómo la máquina de moldeo y el sistema de expulsión pueden ser los culpables.
Leer Más