Retos y soluciones en el moldeo de canal caliente
Descubra cómo maximizar la eficiencia en el moldeo de canal caliente. Aprenda técnicas para reducir residuos, identificar fugas y evitar costosas reparaciones.
Compartir
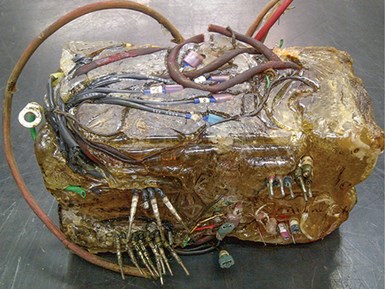
¡No deje que esto le suceda! Las fugas de material fundido son la pesadilla de moldeadores de canal caliente. Pueden evitarse con los procedimientos adecuados y solucionarse antes que se vuelva un problema serio con el software avanzado de los controladores de canal caliente.
El objetivo de todos los moldeadores de inyección es maximizar el tiempo activo y minimizar los residuos, así recurren cada vez más al moldeo de canal caliente como una manera de acelerar el ciclo y reducir el uso de materiales. Aunque el moldeo de canal caliente puede dar excelentes resultados, las cosas pueden ir mal e irán a mal. Si el proceso no se controla correctamente, las reparaciones costosas y el tiempo de inactividad pueden ser potencialmente devastadores.
Este artículo aborda el uso de bloqueos de la máquina, procedimientos, y monitoreo avanzado disponibles en los controles actuales de temperatura de canal caliente para identificar y evitar problemas, detectar pronto las fugas de plástico y predecir fallos en el calefactor.
Mecanismos de seguridad de la máquina de moldeo
Los moldeadores probablemente encontrarán en algún momento estos tres problemas:
- El canal caliente está preparado para calentar, pero no está en marcha el agua de enfriamiento del molde.
- Alguien intenta mover las clavijas de la válvula de entrada de canal caliente cuando el plástico está frío y congelado en el molde.
- La máquina está parada por mucho tiempo, causando la degradación y la quema del material.
- Para evitar que esto suceda, se recomiendan tres mecanismos de seguridad de la máquina:
1. No caliente el canal caliente cuando el agua no está en marcha. Se utiliza agua para enfriar los moldes de canal caliente y proporcionar un control estable de temperatura. Si usted no tiene suficiente flujo de agua y el calor de la canal caliente está encendido, los sellamientos de agua del canal caliente se calientan demasiado y se queman, causando fugas. Sustituir las sellamientos es difícil, lento y costoso.
Mediante la implementación de un simple dispositivo, los moldeadores pueden evitar esta situación. Proteja sus sellamientos asegurándose de que el agua está en marcha. Hay dos opciones principales de seguridad: la primera es monitorear en todo momento el flujo, usando sensores de flujo, presión y/o temperatura. Estos sensores proporcionarán datos clave y enviarán una señal cuando haya un problema. El controlador se "inhibirá" o se pondrá en modo de espera cuando se reciba la señal de problema.
Alternativamente, usted puede monitorear la temperatura de la placa de canal caliente para asegurarse de que no está demasiado caliente. Instale termopares extras en las placas del molde. Estos mostrarán cuando las temperaturas de molde estén fuera de rango e indicarán cuando el líquido no está circulando, identificará bloqueos, etc... El controlador puede estar programado para solo lanzar una alarma o para ponerse en modo de espera o "suspenderá su funcionamiento" cuando la zona de control está fuera del intervalo.
2. Evite la inyección o el movimiento de las clavijas de la válvula de entrada del canal caliente cuando el plástico esté frío. Si el plástico se ha solidificado en el canal caliente, es esencial que todo el sistema de canal caliente sea llevado a las temperaturas correctas de funcionamiento para comenzar la inyección. Si las clavijas de la válvula se mueven cuando la resina está aún fría, probablemente ocasionará graves daños al sistema: las clavijas pueden doblarse o quebrarse, requiriendo reparación y reemplazo. Esto no es una tarea fácil y suele ser costoso, en tiempo de inactividad y en costos de reparación del sistema.
Para evitar que esto ocurra, use los mismo mecanismos mencionados en el #1: monitoreo del agua, usando el flujo, sensores de temperatura o de presión; o medir la temperatura de la placa de molde, que debe estar acompañada de una señal de "OK to Run".
Esta señal le indica que todo está en la temperatura de referencia, todas las zonas abiertas están preparadas, y no hay alarmas, indicando que el agua está funcionando correctamente, el sistema está listo para funcionar, y las clavijas de la válvula pueden moverse con seguridad.
3. Elimine el material quemado o degradado como consecuencia de una parada prolongada de la máquina. El tiempo de residencia es un parámetro clave para cualquier material plástico en un sistema de canal caliente. Es importante saber el número adecuado de inyecciones de material que "residen" en el cilindro de la máquina y el sistema de canal caliente. Los proveedores de resinas publican datos que proporcionan una valiosa información sobre cuánto tiempo los materiales específicos pueden permanecer inactivos antes de que comiencen a degradarse. Además de resinas vírgenes, también deben considerarse los materiales compuestos.
Aditivos, tales como vidrio, talco, estabilizadores UV, colorantes, etc., todos tienen sus propios límites de tiempo de residencia.
Otro detalle sobre el tiempo de residencia: es importante asegurarse de que la máquina del moldeo nunca está detenida durante un tiempo superior al que se ha calculado como seguro. Si se detecta un problema y la máquina pasa de funcionamiento automático a semiautomático o manual, algo o alguien debe intervenir.
El dispositivo recomendado en este caso es establecer temporizadores para abordar esta situación. Cada vez que estos detecten que el tiempo de residencia es más largo de lo normal, pueden notificar al operario y decirle a la máquina o al controlador de canal caliente que apague la máquina o vaya al modo de espera.
En nuestra experiencia, hemos visto al 10% o menos de nuestros clientes de moldeado usando la condición de "espera" en el controlador para evitar que el material se queme. Aunque ese número debería ser mayor, es todavía un mejor porcentaje que el de los moldeadores que no establecen mecanismos de bloqueo para los casos #1 y #2.
Uno por ciento o menos, así es, 1% o menos moldeadores, están realmente estableciendo mecanismos de bloqueo para tratar con control de flujo de agua o evitar que las clavijas de la válvula estén en funcionamiento en un molde frío. Eso significa que el 99% o más de estos moldeadores todavía confía en su personal de planta para detectar problemas antes de que ocurran. Esta es una práctica que se puede mejorar. Está claro que maximizar el tiempo activo y la productividad, y ser más globalmente competitivos, mediante la implementación de unos pocos y simples mecanismos de seguridad pueden mejorar considerablemente las operaciones de procesadores de moldeo.
Mejores procedimientos
Ahora vamos a considerar las mejores maneras para realizar la calefacción y refrigeración secuencial del molde de canal caliente y sin crear una diferencia grande de temperatura dentro del molde que podrían ocasionar la pérdida del sellamiento del colector.
Para mantener las juntas de colector del canal caliente y mantener las recomendaciones de acumulación del proveedor, es esencial la correcta puesta en marcha del molde de canal caliente. Mientras que algunos proveedores de canal caliente tienen las tolerancias más estrictas que otros, las siguientes guías proveen buenos hábitos que deben seguirse para poner en marcha cualquier molde de canal caliente.
Hay que calentar el molde secuencialmente; las masas más grandes, como el bloque del colector, incluyendo la entrada, se debe calentar primero, seguido de las boquillas de calentamiento más rápidas. Esto es lógico, ya que las masas más grandes tardan más tiempo en calentar y propagarse, y las boquillas se calientan rápidamente.
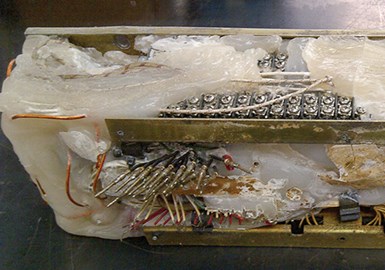
Se ha observado con frecuencia el impacto de las fugas de material en un sistema de canal caliente debido al exceso de procesadores utilizados en el proceso de moldeo.
Permitir que las boquillas encuentren su punto de ajuste podría ocasionar una expansión térmica desigual dentro de la herramienta, causando la deformación dentro del sistema, que conduce a fugas. También, si las boquillas se calientan primero, en el momento en que el colector depende del calor y se está en plena producción, se podría estar quemando el material.
Nota: Es fundamental dar al material que se expande una salida cómoda. Si calienta el interior del molde (colectores) y no la entrada, el material se expande y puede desplazar la entrada como un corcho en una botella de champán, seguido del escape de material fundido potencialmente peligroso.
Una vez en funcionamiento, es común tener problemas con una o más cavidades en el molde de canal caliente. El bloqueo de resina mala (fragmentos de metal, etc.) es un problema frecuente. Si es esencial mantener las piezas moldeadas con las restantes cavidades 'buenas', es importante no apagar el calor a la(s) boquilla(s) mala(s).
La contracción térmica creada por ello podría resultar en el daño del sellado del canal caliente, lo que ocasiona fugas. El procedimiento correcto es bajar la temperatura de la boquilla "mala" a un punto donde el material se solidifique. Esto detiene el flujo de material y evita la quema o degradación del material, lo mismo que desactivar la zona, mientras que proporciona la máxima expansión térmica para mantener el sellado del colector.
El problema con las fugas
Demasiados procesadores por moldeo han visto lo que sucede cuando se producen fugas de material dentro de un sistema de canal caliente. El plástico sale del colector y las boquillas. Si estas filtraciones pasan desapercibidas los daños que causan pueden ser nada menos que catastróficos (véase las fotos que ilustran el artículo).
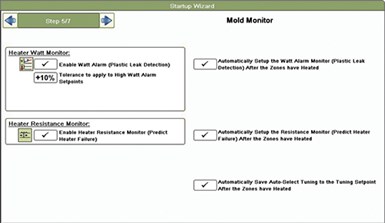
Aunque es ignorado por muchos moldeadores, los últimos controles de canal caliente ofrecen la capacidad de controlar el uso eléctrico del calefactor para detectar fugas antes de que sea algo inmanejable. (Aquí se muestra un monitor de potencia de Gammaflux).
Los sistemas de canal caliente dependen de un gran número de calentadores y termopares para funcionar con eficacia. Estos están presentes dentro y fuera del colector y las boquillas y, a veces, incluso en las puntas de la boquilla. Un molde de canal caliente de 64 cavidades puede fácilmente tener 75 zonas de control de o más. Cada calefactor y termopar tiene asociados cables que van desde el molde de canal caliente a un conector donde los cables conectan el canal caliente con el regulador de temperatura.
Cuando ocurren las fugas, es común que los cables queden recubiertos de plástico fundido y al final deben sustituirse los calentadores afectados y todos los termopares. Algunos proveedores de canal caliente integran los calentadores en las boquillas del canal caliente, lo que generalmente significa que la boquilla entera debe ser reemplazada. No hace falta decirlo, esto es muy caro y ocasiona un tiempo de inactividad significativo.
El costo de la reparación de un sistema de canal caliente dañado debido a las fugas se estima en US$500 por cada zona, y es una cifra muy moderada, ya que no incluye el tiempo de producción perdido. ¿Así que cuánto cuesta ese molde de canal caliente de 64-cavidades que está lleno de material y es necesario reparar? ¡Costará US$37.000 —por lo menos!
Todo esto puede evitarse con el uso correcto de los mecanismos y procedimientos de seguridad de la máquina anteriormente mencionados. Mejor aún, el uso de técnicas avanzadas de monitorización disponibles en los actuales controladores de temperatura de canal caliente pueden disminuir en gran medida las posibilidades de fuga de material en el sistema de canal caliente.
Características de monitoreo avanzado
Los mejores controladores de temperatura de canal caliente emplean hoy herramientas excelentes para ayudar a los moldeadores a detectar y prevenir posibles fugas de material en sus moldes de canal caliente. Cuando el plástico se filtra en el molde, ocupa un espacio que estaba ocupado por aire. Al eliminar el espacio de aire se crea un disipador térmico para la masa circundante. En modo automático, el controlador aumenta la potencia para compensar la pérdida de calor. Algunos controladores monitorean el uso eléctrico del calefactor de diversas maneras para detectar tales tendencias.
Por ejemplo, la alarma watt/fuga de Gammaflux monitorea el consumo de potencia de cada zona de control de canal caliente y alerta al usuario cuando empieza a producirse una fuga. Cuando las lecturas de voltaje de cualquier zona de control son demasiado altas (típicamente 10% por encima de lo normal), esto indica posibles fugas de material y alerta al usuario para inspeccionar el colector.
Medir con precisión la potencia real y actuar con prontitud en lecturas sospechosas, puede ser la diferencia entre un corto viaje a la zona de herramientas para hacer una reparación, o semanas de pérdidas en la producción. La triste realidad es que muchos moldeadores tienen controles de detección de fugas pero no saben cómo usarlos.
Contenido relacionado
Meximold 2023: la vanguardia en moldeo de plásticos vuelve a Querétaro
Llegó la hora de vivir la experiencia más completa en todo lo relacionado con tecnologías para manufactura de moldes y transformación de plásticos. Meximold, en su cuarta edición, reunirá a los líderes de la industria de moldes, troqueles y herramentales en Querétaro. Regístrese sin costo y sea testigo de las últimas tendencias y equipos en moldes, troqueles y herramentales.
Leer MásDesafíos en la ventilación de moldes: velocidad de flujo y calidad
Descubra la ciencia detrás del sistema de venteo en el moldeado de plástico. Desde su funcionamiento básico hasta cómo el aire y el plástico interactúan para obtener piezas de calidad.
Leer MásClaves para el diseño de moldes de inyección de plástico
Exploramos aspectos esenciales del diseño de moldes, desde la elección del material hasta la prevención de problemas de calidad en el moldeo.
Leer MásLo que debe saber sobre las guías y casquillos de moldes
Profundice en las especificaciones de casquillos y guías en moldes. Conozca las tolerancias dimensionales y cómo garantizar un funcionamiento óptimo.
Leer MásLea a continuación
Reduzca los tiempos de paro de los sistemas de colada caliente
Instrucciones prácticas para solucionar sus problemas con sistemas de colada caliente rápidamente y mediante un enfoque sistemático.
Leer MásQué son los sistemas de colada caliente y cómo funcionan
Un experimentado transformador de plásticos aborda los beneficios, las mejoras y los problemas cotidianos de las coladas calientes, luego de trabajar por décadas con varias marcas en el mercado de estos sistemas.
Leer MásClasificaciones de moldes de inyección de plásticos: análisis detallado
Examine los factores que influyen en la durabilidad de los moldes de inyección. Desde la complejidad del diseño hasta la selección de materiales, aprenda cómo optimizar la vida útil de los moldes.
Leer Más