Seguirle el ritmo informativo a esta pandemia ha sido todo un reto. No solo porque al final estamos hablando de vidas humanas en riesgo, o de economías en crisis, o del colapso de sistemas sanitarios. Desde nuestro nicho de negocio ha sido una tarea demandante porque la industria que atendemos se está moviendo a un ritmo vertiginoso. Con sus propios problemas de proveeduría e inventario, falta de personal, y limitaciones de recursos financieros, las plantas de manufactura en todo el mundo se han sumado al ejército que lucha contra esta pandemia, ofreciendo sus capacidades tanto para el desarrollo de dispositivos médicos, como para la fabricación de elementos de protección personal.
Aquí cabe señalar que muchas de estas iniciativas se han originado de manera espontánea, algunos fabricando piezas internamente y haciendo uso de sus propias capacidades, y otros aliándose en consorcios de manufactura que toman ventaja de lo mejor que cada uno de los asociados puede ofrecer para salir “al campo de batalla” lo más pronto posible.
Por lo anterior, la Ley de Producción de Defensa que invocó el presidente de los Estados Unidos, Donald Trump, fue una medida innecesaria para un movimiento que ya la industria había impulsado orgánicamente. Además, como lo expresó Rick Kline Jr., presidente de Gardner Business Media (casa editorial de esta publicación), cada eslabón de la cadena de suministro que se ha creado para la producción de esta tecnología médica debe seguir procesos cuidadosamente certificados.
“No es tan simple como decirles a los fabricantes que comiencen a producirlos. Necesitan gerentes de calidad e ingenieros de manufactura que comprendan estos estándares, así como las instalaciones para cumplirlos. Luego está la dificultad añadida de que muchos componentes deben desarrollarse desde cero, porque a menudo provienen de fuentes extranjeras y, por lo tanto, no pueden obtenerse en el marco de una crisis como esta. Incluso la comunicación entre las compañías que planean nuevos proyectos es compleja y requiere mucho tiempo. La rapidez con que los fabricantes se han coordinado es un testimonio de su ingenioso uso de la tecnología. Desde las redes sociales hasta el diseño digital y la impresión industrial en 3D, las comunicaciones y los procesos que, generalmente, demorarían semanas o meses están sucediendo literalmente durante la noche”, compartió Kline en una columna publicada en The Wall Street Journal.
Toda esta intrincada cadena de diseño, producción y distribución explica por qué las respuestas e iniciativas lideradas por las empresas y usuarios de manufactura aditiva han sido las más rápidas y generalizadas. Hay portales web como thingiverse.com y www.enable.hp.com que ofrecen, sin obstáculos, diseños listos para descargar e imprimir en 3D de máscaras de protección, cubrebocas, protectores de muñecas, conectores para ventiladores, y hasta respiradores de emergencia. Todo al alcance de un clic.
Por otra parte, están los OEMs y las empresas proveedoras de maquinaria, tecnologías e insumos que, en un esfuerzo más dispendioso, y en algunos casos menos noticioso, han adaptado sus algunas de sus líneas de producción para producir estos mismos insumos con diseños propios o de terceros, en una labor que además implica descontinuar su propia producción y hacer uso de sus propios inventarios. Esos cálculos vendrán luego, una vez superada la pandemia.
También están quienes, sin tener líneas de manufactura, pero con experiencia en temas de diseño, inspección, calidad, y metrología están ofreciendo sus servicios de software libre y asesoría para la fabricación de componentes,
A continuación, reseñamos algunas de estas iniciativas, que no son todas y están de lejos de ser suficientes, pero son el aporte más valioso de la industria manufacturera frente a esta pandemia.
Ford y Ventec Life Systems: ventiladores y máscaras quirúrgicas
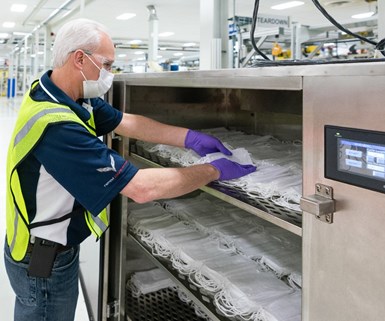
Ventec Life Systems anunció a través de un comunicado de prensa que General Motors construirá ventiladores de cuidados críticos VOCSN aprobados por la Administración de Alimentos y Medicamentos (FDA por sus siglas en inglés) en la planta de GM ubicada en Kokomo, Indiana.
En un esfuerzo separado, GM comenzó a fabricar máscaras quirúrgicas de Nivel 1 aprobadas por la FDA en su planta ubicada en Warren, Michigan. La producción llegará a las 50,000 máscaras por día, con el potencial de aumentar a 100,000 por día. Esta iniciativa propuesta por los empleados fue creada, planificada y aprobada en aproximadamente 48 horas e involucra la base de suministro tradicional de GM, así como nuevas alianzas específicas para la industria de dispositivos médicos.
3M, Ford y GE Healthcare: respiradores y ventiladores
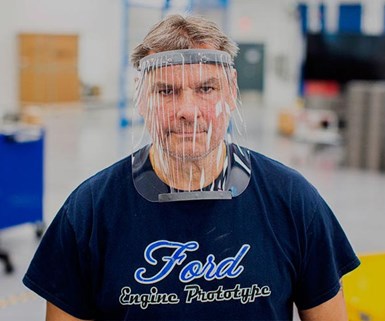
Ford colabora con 3M y General Electric Healthcare para incrementar la producción de respiradores y ventiladores que esas dos empresas fabrican. Ford se encarga de fabricar los respiradores de 3M en las instalaciones de su Centro de Manufactura Avanzada en Michigan y trabaja de manera conjunta para desarrollar un nuevo diseño que aproveche componentes que ambas empresas utilicen para otros productos.
Por esto, los equipos de Ford y 3M han estado adaptando las piezas disponibles en los estantes, como los ventiladores de los asientos con control de temperatura de Ford F-150 para el flujo del aire, filtros HEPA 3M para que no pasen los contaminantes del aire ni gotas que transporten el virus, así como paquetes de baterías de herramientas portátiles para alimentar estos respiradores hasta por ocho horas.
El fabricante de automóviles también está trabajando GE Healthcare para producir en sus instalaciones una versión más simple del ventilador que actualmente comercializa. El equipo de diseño de Ford también está creando y probando los protectores transparentes de cara completa para trabajadores médicos y personal de primeros auxilios. Estos protectores bloquean completamente la cara y los ojos del contacto accidental con líquidos y cuando se combinan con respiradores N95, pueden ser una forma más efectiva de limitar la exposición potencial al coronavirus.
Honeywell: de componentes aeroespaciales a máscaras N95
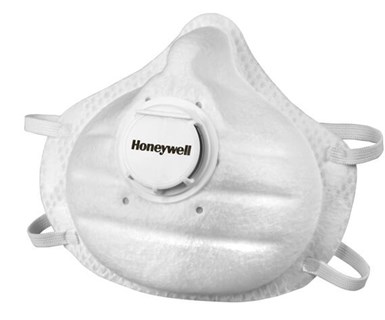
Honeywell está agregando operaciones de producción de mascarillas en su campus de Phoenix Engines, en Arizona, al tiempo que continúa con sus tareas de manufactura tradicionales. Estas instalaciones son unas de las más grandes y se dedican al diseño y fabricación de motores de propulsión de aviones y unidades de potencia auxiliar desde 1950.
La expansión de Phoenix, junto con la nueva producción anunciada previamente en Rhode Island, permitirá a Honeywell producir más de 20 millones de máscaras desechables N95 mensualmente para combatir COVID-19 en los EE. UU. La contratación ya está en marcha para aproximadamente 500 o más empleos nuevos en Arizona, lo que elevará el total entre ambas operaciones a 1,000.
Meggitt, Nissan y McLaren producen ventiladores
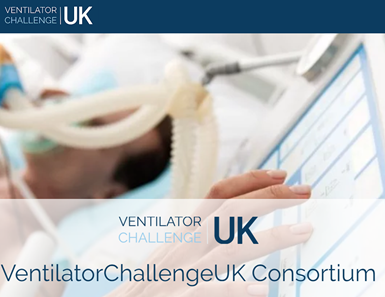
Un equipo dirigido por la empresa Meggitt (que incluye a Airbus, GKN, Thales y Renishaw) es uno de los tres consorcios encargados por el gobierno de Reino Unido para atender la demanda urgente de ventiladores hospitalarios debido a la pandemia de COVID-19. El grupo aeroespacial, más dos de la industria automotriz, encabezados por McLaren y Nissan, tienen como objetivo diseñar prototipos de ventiladores a medida que crece la demanda del kit.
El proyecto es gestionado por la organización de investigación High Value Manufacturing Catapult con sede en Solihull. Dick Elsy, Director Ejecutivo de High Value Manufacturing Catapult y quien lidera el proyecto, dijo que esperan producir 5,000 ventiladores lo antes posible. En última instancia, el objetivo es producir 30,000 más.
Lentes de seguridad de Arburg, Ems-Chemie y Uvex
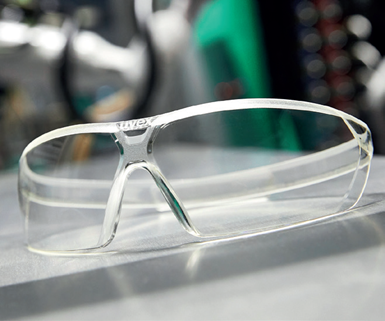
Lentes de seguridad (googles) producidos por Arburg, Ems-Chemie y Uvex.
El proveedor alemán de máquinas de moldeo por inyección Arburg, el especialista suizo en materiales Ems-Chemie y el fabricante alemán de lentes Uvex unieron esfuerzos para proveer una solución rápida a personal médico en la situación actual. Su aporte es la producción de 20,000 gafas de seguridad (goggles) para proteger los ojos y los tejidos conjuntivos de la contaminación.
El Dr. Thomas Walther, director de tecnologías de aplicación de Arburg, fue contactado por una doctora de un hospital en Rottweil el pasado 30 de marzo. Ella había escuchado que en una feria industrial, Arburg había producido unos lentes protectores que ella y sus colegas requerían con urgencia. Walther pasó el requerimiento a Gerhard Böhm, director de ventas, quien ya estaba involucrado en iniciativas regionales de este tipo. Rápidamente las tres empresas se alinearon y dieron inicio al proyecto.
Clariant: producción de desinfectantes a gran escala
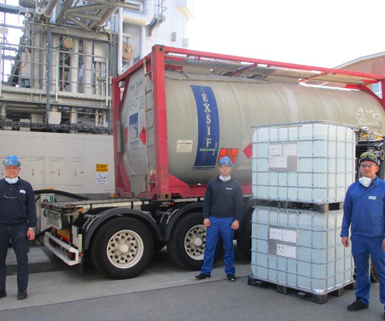
La empresa química especializada Clariant comenzó la producción de 2 millones de litros de desinfectante. El producto se suministra directamente o mediante socios de reempaque a hospitales regionales y otras instituciones vitales en Bavaria.
En sus instalaciones en Gendorf, Clariant puede utilizar su infraestructura disponible para mezclar los ingredientes necesarios para producir el desinfectante. Esto le permite a la compañía satisfacer cerca de dos tercios de la demanda objetivo mensual del Estado bávaro, que apunta a producir un total de 10 millones de litros de desinfectantes en los próximos tres meses.
Sidel: de desarrollo de envases PET a moldeo de botellas para desinfectantes
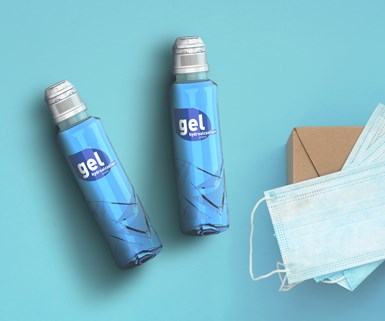
Sidel: de desarrollo de envases PET a moldeo de botellas para desinfectantes.
Sidel, productor de sistemas de moldeo por soplado y estirado de PET, transformó su centro internacional de excelencia para el desarrollo de envases de PET y soluciones de soplado en Francia, en una instalación de producción para moldear botellas de desinfectante de manos de PET. El primer lote de 5,000 botellas para el desinfectante se entregó al Hospital de Dijon y otro lote se distribuyó a farmacias y hospitales en la ciudad portuaria de Le Havre en Normandía.
En solo dos días, el centro de desarrollo de Sidel encontró las materias primas y los socios de cooperación para producir botellas de 500 ml utilizando un molde existente, así como las preformas aportadas por un productor de bebidas.
Eastman: donación de material para protectores faciales
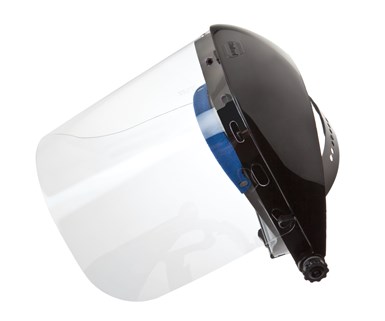
Eastman fabricó y donó el material utilizado para producir protectores faciales en Tennessee, Estados Unidos. La Comisión de Educación Superior de Tennessee coordinó un esfuerzo para producir 10,000 protectores faciales en dos semanas utilizando impresoras 3D ubicadas en universidades de todo el estado. Las universidades intervinieron para cerrar esa brecha haciendo protectores faciales con impresoras 3D. Austin Peay, ubicado en Clarksville, comenzó a comprar láminas de acetato en las tiendas locales para producir los escudos que proporcionan una barrera segura contra las infecciones cuando se trata a pacientes con COVID-19.
El gran escudo de plástico transparente que se adhiere al marco portátil se convirtió en el cuello de botella del proyecto, cuando el suministro de lámina de acetato se terminó. Eastman recibió una llamada para ver si podían producir y donar material de emergencia para ayudar a esta causa. En un par de días ya estaban produciendo rollos de PETG específicamente para este esfuerzo de protección facial y, al día siguiente, 1,000 pies de película PETG fueron entregados.
Solvay y Boeing: compuestos avanzados para protección facial
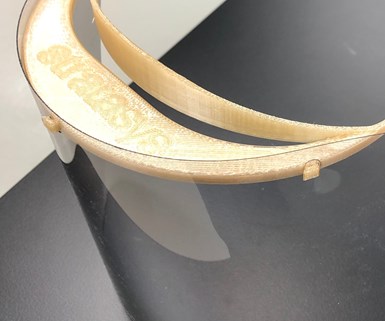
Solvay se asoció con Boeing para la producción de caretas mediante el suministro de película transparente de alto rendimiento y grado médico. Boeing se acercó a Solvay gracias a su experiencia en el uso de materiales compuestos y adhesivos avanzados en múltiples programas comerciales y de defensa.
Fabricados por el negocio Ajedium Films, de Solvay, Boeing utiliza la película termoplástica en la producción de miles de protectores faciales que los hospitales y trabajadores médicos en los EE. UU. necesitan de manera crítica para protegerlos de COVID-19. La película se fabrica con el Radel PPSU (polifenilsulfona) o Udel PSU (polisulfona) de grado médico de Solvay, dos polímeros especiales transparentes ampliamente utilizados para dispositivos médicos debido a su capacidad de esterilizarse y resistir desinfectantes agresivos.
Stratasys: coalición para protectores faciales
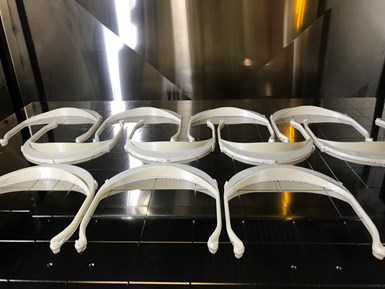
Una coalición de empresas y universidades reunidas por Stratasy está produciendo protectores faciales con impresoras 3D. En un esfuerzo por enfrentar la pandemia de COVID-19, Stratasys estableció un objetivo inicial para producir 5,000 protectores faciales sin costo. Esto incluye una visera impresa en 3D y un protector de plástico transparente que cubre toda la cara. Stratasys sostuvo que la coalición podría llegar a producir 11,000 caretas en las próximas semanas, y 16,000 o más en el futuro.
Cualquier empresa de impresión 3D que desee ayudar a imprimir al menos cien viseras puede completar un formulario en línea para vincularse. Para Estados Unidos, Stratasys está utilizando su software de gestión de órdenes de trabajo GrabCAD Shop para asignar órdenes de los sistemas de salud a cada miembro de la coalición. En Europa, la compañía está sirviendo como un centro para conectar oficinas de servicios con quienes solicitan ayuda, y ha enviado ofertas y solicitudes en la mayoría de los países más grandes. La compañía también ha publicado las instrucciones de montaje e impresión de caretas completas para que cualquiera pueda producir caretas por su cuenta.
HP: archivos descargables de impresión 3D para dispositivos médicos
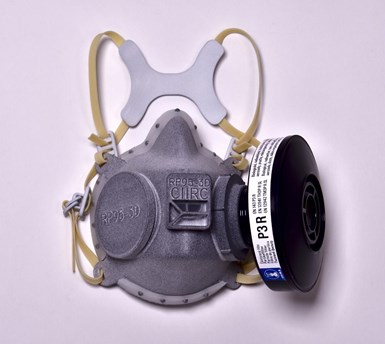
Con el ánimo de apoyar la producción rápida de piezas críticas para afrontar la crisis, HP compartió en su sitio de impresión 3D los diseños descargables de algunos dispositivos médicos y de protección personal para contener el COVID-19. Cada ficha incluye la descripción de la pieza, el tipo de impresora y material recomendado para utilizar, y sus rangos de aplicación. Estos son algunos de los productos disponibles: adaptador para abrir puertas sin contacto de manos, ajustador de máscaras, protectores de cara, ventilador de campo y máscaras faciales FFP3.
Negri Bossi: máscaras para personal médico
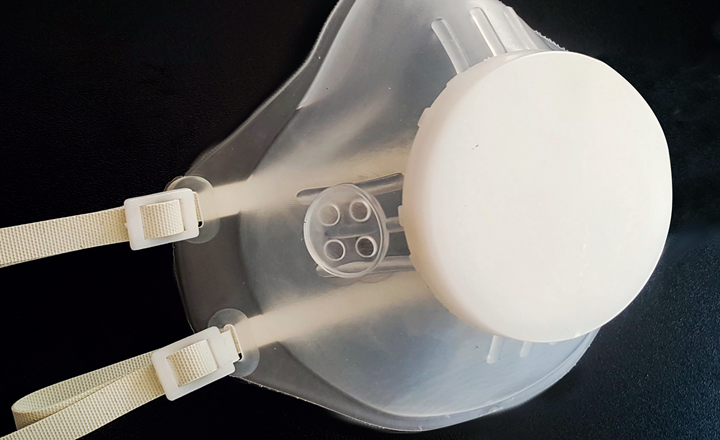
La compañía italiana fabricante de máquinas de moldeo por inyección destinó el uso de dos inyectoras en su sede de Cologno Monzese, en Milán, para producir máscaras faciales totalmente fabricadas en un termoplástico suave y muy flexible, que resulta cómodo y ergonómico. El dispositivo, diseñado por Negri Bossi, puede ser reutilizado gracias a que el filtro de tela puede ser cambiado e inclusive reemplazado por una válvula de exhalación si se requiere un nivel más alto de protección y para futuras certificaciones. La máscara, que es totalmente transparente y no limita la visibilidad, puede ser facilmente sanitizada con agua y jabón.
El molde fue fabricado en tiempo récord por Esistampi, un fabricante de moldes con sede en Ancona y los materiales fueron donados por Francesco Franceshetti Elastomeri Company. En capacidad total de producción, es posible fabricar 500 máscaras por hora. El proyecto recibió el apoyo inmediato de diversas entidades que se sumaron para la logística de distribución.
Contenido relacionado
Amcor y Berry Global se fusionan para liderar empaques sostenibles
Con más de 400 instalaciones en 140 países, la nueva Amcor plc integrará capacidades para ofrecer soluciones innovadoras y acelerar la transición hacia empaques sostenibles.
Leer MásNearshoring: gobierno mexicano anuncia incentivos para sectores clave
Conozca los detalles del decreto que otorga beneficios fiscales para empresas exportadoras de sectores como el de electrónicos, farmacéutico y automotriz.
Leer MásiTech, nuevo representante de ventas de Netstal para México
Netstal, parte del Grupo KraussMaffei, fortalecerá su presencia en el mercado mexicano de piezas moldeadas por inyección con el apoyo de la agencia de ventas iTech-Global.
Leer MásProcesamiento de plásticos en el sector médico: calidad y regulación
Explore las tendencias y desafíos del procesamiento de plásticos médicos, desde sistemas de calidad hasta regulaciones actuales.
Leer MásLea a continuación
Así van las proyecciones en economía circular para los plásticos
¿Qué tan cerca estamos de alcanzar la meta de lograr empaques plásticos 100 % reusables, reciclables y compostables para 2025? ¿Qué acciones vienen en curso para cumplirlas? Entrevista exclusiva con la Fundación Ellen MacArthur sobre el panorama de los plásticos en la economía circular en el mundo y en América Latina.
Leer MásMoldeo por soplado: guía completa y preguntas frecuentes
¿Está interesado en el moldeo por soplado? Conozca las ventajas, desventajas y fundamentos de este proceso de transformación de plásticos.
Leer MásSoluciones tecnológicas para la circularidad de los empaques plásticos
Proveedores de tecnologías para la industria de plásticos, miembros del Compromiso Global liderado por la Fundación Ellen MacArthur, enfocan sus recursos de innovación hacia la creación de soluciones que permitan reciclar y reutilizar el 100 % de los empaques plásticos. Conozca algunas de estas aplicaciones.
Leer Más