Controle el desfase de temperatura de la zona del cilindro
El control deficiente de la temperatura genera un flujo y proceso errático del fundido. Estos son algunos consejos sobre cómo tener estos aspectos bajo control.
Moldear plástico en una pieza aceptable es un proceso complicado con cientos de variables. A algunos les gustaría manejarlo siguiendo un procedimiento ISO 9000. Sin embargo, no creo que alguien los conozca todos, porque siempre están apareciendo nuevos. Pero una variable clave, que si se pasa por alto arruinará su proceso, es "el control de la zona de temperatura". ¿Qué es y qué puede hacer un procesador para controlar esto?
El desfase de la temperatura de zona se produce cuando una de las zonas de temperatura en el cilindro (no la boquilla) está constantemente más caliente, en más de 5° C (10° F), que el punto de ajuste. El desfase de la temperatura de la zona puede suceder incluso cuando el controlador de temperatura de la zona nunca requiere energía para encender la banda calefactora.
Los controladores de temperatura deben poner en marcha el ciclo y apagarlo para controlar la temperatura de la zona. No todas las zonas tendrán el mismo ciclo, ya que cada zona del cilindro tiene diferentes funciones. Por ejemplo, la zona posterior puede iniciar el ciclo más a menudo o por más tiempo que la zona central, ya que está cerca de la garganta de alimentación que es más fría.
La conclusión es que cada zona debe controlar la temperatura para que el tornillo y el proceso trabajen consistente y correctamente. Si la zona del cilindro está demasiado caliente y el controlador no está funcionando, todo el calor en esta zona se está generando por la rotación o recuperación del tornillo.
Algunos pueden pensar que esto está bien o incluso que es rentable, ya que ahorra electricidad. Al comienzo de mi carrera, mi mentor me mostró cómo se podía apagar la energía a los calefactores de la zona y aun así mantener la máquina en marcha. Según recuerdo, se sentía muy orgulloso de esto.
Por desgracia, no es la manera de procesar. Si se está constantemente encendiendo o apagando la banda calefactora, no se está controlando la temperatura. Esto es un control deficiente de la temperatura y no proporcionará un flujo o proceso constante del fundido.
Entonces, ¿cómo obtenemos una corriente del fundido con temperatura uniforme? Los controladores de temperatura de la zona del tornillo y el cilindro deben funcionar correctamente para conseguir uniformidad en la masa fundida. Este es casi como un malabarismo, que involucra el diseño del tornillo, la resina, las configuraciones de temperatura, el diseño de la pared del cilindro, el coeficiente de fricción de los pellets en la pared del cilindro, y hasta la omnipresente Ley de Murphy.
La consistencia del fundido es más complicada en el moldeo por inyección ya que el tornillo no gira continuamente, es reciprocante. Además, no olviden que por lo general no podemos medir la temperatura real del fundido cuando estamos moldeando. No estoy seguro de comprender todas estas interacciones, pero tengo algunos consejos para saber cuál es la causa de la anulación de la temperatura de la zona y qué hacer para lograr el control.
Para entender las causas del descontrol de la temperatura, céntrese en cómo el tornillo funde el plástico.
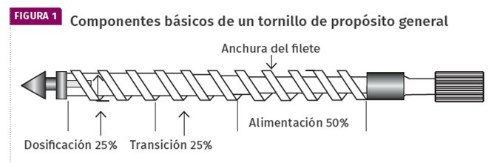
Las secciones principales de un tornillo de propósito general y el porcentaje
que le corresponde a cada una de la longitud total de los filetes. Note cómo
el diámetro original es más grueso en la sección de transición. Aquí es donde
se desarrollan las mayores presiones de compresión.
La figura 1 es un diagrama básico de un tornillo de propósito general (GP); nuestro enfoque es la zona de transición (compresión) ya que es la zona donde se funden los pellets de plástico. Generalmente es conocido que alrededor del 80% de la energía necesaria para fundir el plástico viene de la fricción y la compresión desarrollada por la rotación del tornillo. El resto proviene de las bandas de calefacción. La energía necesaria para fundir el plástico proviene de dos fuentes principales a medida que el tornillo gira:
- La fricción de los pellets entre la pared de cilindro y los filetes de los tornillos.
- La compresión desarrollada en la zona de transición.
Observe en la figura 1 cómo el diámetro de la raíz es más grueso en la sección de transición. Ahí es donde se desarrollan las altas presiones de compresión. Lo que entiendo es que estas presiones son en miles de psi (decenas de mega pascales). Además, estas fuerzas pueden estar concentradas en áreas pequeñas, entre la pared del cilindro y el filete, para el desarrollo de puntos o zonas calientes cuando hay picos de temperaturas.
Para comprobar esto, observe cómo es un tornillo nuevo: luminoso y brillante. Luego observe el color del metal después de su uso; la sección de alimentación se ve bien pero la sección de transición ahora es oscura. Ahora fíjese en las áreas oscuras y verá no sólo un color negro, sino también un negro azulado, marrones y en algún momento colores iridiscentes.
A continuación, busque un manual sobre metales y verá los colores que los metales tienen cuando se someten a calor. Encontrará que los azules y otros colores iridiscentes indican que el metal ha experimentado temperaturas muy por encima de su temperatura de fusión y mucho más altas que la que se han establecido en los reguladores de temperatura.
Todo esto es prueba de la existencia de puntos calientes, y el cilindro tiene que disipar este calor antes de que se degrade el plástico. Esto explica por qué debe tener espacios entre las bandas del calentador y no usar camisas en el cilindro. Es cierto que las camisas de aislamiento ahorran energía, pero pueden también afectar el control de la temperatura de fusión, así que hay que aislar las bandas calefactoras individuales, no el cilindro entero.
Las extrusoras de alta gama y algunas máquinas de moldeo tienen enfriamiento entre las bandas calefactoras para ayudar a controlar la temperatura. La conclusión es que hay veces en que el proceso de fusión-recuperación del tornillo genera demasiada energía y se refleja en el descontrol de la temperatura de la zona. Entonces, ¿cómo puede manejarse esta situación?
Estas son algunas soluciones posibles:
• Retire las camisas del cilindro y aísle las bandas calefactoras individuales para ahorrar de energía.
• Baje las rpm del tornillo de modo que la recuperación del tornillo toma apenas 1-2 segundos del tiempo de enfriamiento. No intente extender el ciclo. No establezca el tiempo de recuperación demasiado cerca del tiempo de enfriamiento, ya que el tiempo de recuperación varía durante la producción. A menos que sea excesivamente alta, no baje la contrapresión.
• Sustituya el tornillo por uno que proporcione mejor uniformidad de fusión. Evite mezclar tornillos. No use un tornillo de propósito general, que el compañero columnista Jim Frankland llama tornillos "sin propósito". El diseño del tornillo es crítico para la uniformidad de la fusión, la recuperación de la inversión es significativa y real. He documentado más de US$250.000 en ahorros en un año al cambiar a un diseño de tornillo más adecuado en siete máquinas (400 a 1200 toneladas).
• Añada ventiladores entre las bandas calefactoras.
• Eleve la temperatura de la zona y la de la zona anterior. Suena loco pero esto reducirá la fricción del plástico contra la pared del cilindro, que a su vez disminuye la energía generada y mejora el control de la temperatura.
• Monitoree el ciclo de encendido/apagado de las zonas de temperatura durante la producción.
Tal vez el descontrol de la temperatura de la zona es la variable que le da a Murphy la munición para actuar. No tiene que ser así.
Contenido relacionado
Manufactura aditiva: nuevas posibilidades en inyección de plástico
La calidad de las superficies inyectadas utilizando canales calientes representa desafíos para la impresión 3D como alternativa para la fabricación de los canales de flujo dentro del distribuidor. Descubra cómo la manufactura aditiva contribuye en el moldeo por inyección multicomponente.
Leer MásQué son los sistemas de colada caliente y cómo funcionan
Un experimentado transformador de plásticos aborda los beneficios, las mejoras y los problemas cotidianos de las coladas calientes, luego de trabajar por décadas con varias marcas en el mercado de estos sistemas.
Leer MásHasco celebra apertura de oficina en Colombia
Hasco inauguró su oficina en Bogotá, Colombia, con el objetivo de brindar soporte comercial y técnico a sus clientes de la región Andina y Centroamérica.
Leer MásVamos a reconectar con innovación y tecnología en Meximold 2023
En un mundo que ha experimentado transformaciones inimaginables, en el que la virtualidad y la digitalización han sido protagonistas indiscutibles, nos entusiasma saber que los eventos presenciales son más necesarios que nunca, y qué mejor manera de reconectar que a través de un encuentro de vital importancia para la industria manufacturera: Meximold.
Leer MásLea a continuación
Cómo instalar una máquina de inyección de plásticos: guía completa
¿Instalación de una máquina de inyección en el horizonte? Asegúrese de conocer todos los detalles importantes para maximizar la eficiencia y minimizar el tiempo de inactividad.
Leer MásRevisando el tamaño del disparo vs. la capacidad del cilindro
Hay muchas variables a las que debe prestar atención al moldear por inyección, pero no olvide verificar qué cantidad del cilindro está utilizando para fabricar las piezas.
Leer MásBusque una hoja de ajuste universal para su proceso de inyección
Descubra cómo una hoja de ajuste específica del molde puede transformar sus procesos de moldeo por inyección, garantizando consistencia y reduciendo costos.
Leer Más