Los tanques pequeños de gasolina, del tipo que se utiliza en equipos como cortacéspedes y sopladores de nieve, se han producido típicamente a partir de polietileno de alta densidad (HDPE).
Los tanques de gasolina para el sector automotor están sujetos a rigurosos estándares de emisión, que requieren construcciones multicapa y que emplean materiales de barrera diseñados para evitar la difusión de gasolina a través de la pared del tanque. No es un requisito que los tanques de gasolina pequeños cumplan con estas normas. Además, su tamaño permite que se produzcan, en la mayoría de los casos, mediante moldeo por inyección.
El tanque pequeño típico es un diseño de dos piezas producido en un molde familiar. Las dos mitades se sueldan térmicamente antes de que se hayan enfriado por completo. Aunque los diseños reales del tanque pueden variar de manera sustancial, el proceso de fabricación es generalmente el mismo.
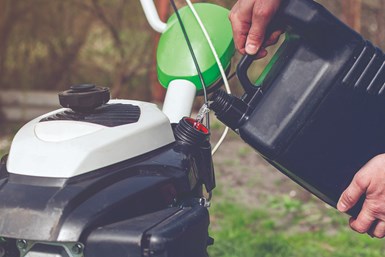
Una amplia investigación de la industria de los tanques de combustible agrietados resultó de un cambio de 0,006 g / cm3 en la densidad del material utilizado para producir los tanques.
En la década de 1990, el material de elección para pequeños tanques de gasolina en toda la industria norteamericana era un HDPE con un índice de fluidez (MFR) de 4.0 g/10 min y una densidad de 0.946 g/cm3. Esto está cerca de la densidad mínima para los materiales clasificados como HDPE, y en combinación con el peso molecular promedio asociado con este valor MFR, el material produjo un buen equilibrio de propiedades de soporte de carga y ductilidad.
Entonces, como sucede a menudo en el mundo de los plásticos básicos, el proveedor del material tomó la decisión de suspender el grado. En ese momento no había reemplazos directos. Los grados con densidades comparables, por lo general, tenían un peso molecular promedio más alto (MFR más bajos). Los materiales disponibles con el mismo MFR típicamente tenían densidades más altas.
El proveedor del material descontinuado sí producía, y sigue produciendo hasta el día de hoy, un material con la misma densidad y un MFR nominal de 2.2 g/10 min. Este habría sido el material ideal para reemplazar la resina obsoleta, y es un grado dirigido específicamente para este tipo de aplicación.
Sin embargo, como hemos discutido al revisar la comprensión del MFR en la industria, muchos procesadores aún creen que las presiones necesarias para llenar y empaquetar una cavidad de molde son inversamente proporcionales a la diferencia en MFR.
Todos los procesadores involucrados en la fabricación de estos tanques expresaron dudas sobre su capacidad para llenar los moldes con el material de mayor viscosidad y todos se negaron a tomar muestras del material. En su lugar, optaron por un material con un MFR de 4.0 g/10 min y una densidad de 0.952 g/cm3.
La transición parecía perfecta. Sin embargo, en menos de un año se descubrieron los primeros tanques de gasolina agrietados durante su uso. Las investigaciones sobre la causa del agrietamiento llevaron meses e involucraron múltiples organizaciones de servicios analíticos, así como a los usuarios finales que estaban poniendo estos tanques de gasolina en sus productos.
La Comisión de Seguridad de Productos de Consumo se involucró y contribuyó a la habitual falta de comprensión científica que normalmente caracteriza a las organizaciones gubernamentales. Algunas empresas quebraron y otras dejaron de suministrar los pequeños tanques de gasolina, por considerar que los riesgos eran demasiado grandes.
Al menos un usuario final dedicó una gran cantidad de tiempo y talento a comprender la interacción entre la selección de materiales, el diseño de piezas y las condiciones de procesamiento. Toda esta tarea se centró en un cambio de 0.006 g/cm3 en la densidad del material utilizado para producir los tanques.
El trabajo analítico estableció que el mecanismo de fallas era el agrietamiento por estrés ambiental (ESC). Este es un proceso impulsado mecánicamente que se acelera por la presencia de una influencia química. Pero para diagnosticar correctamente los factores que contribuyen al ESC es esencial comprender la interacción entre las propiedades del material, el diseño de piezas, los métodos de ensamblaje y el entorno de aplicación.
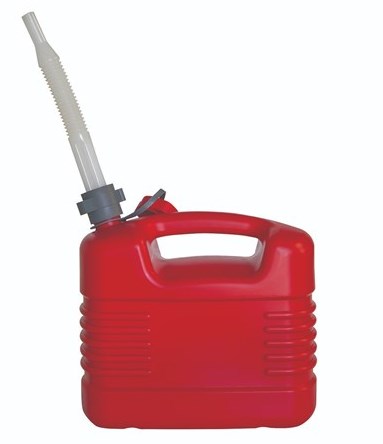
El ESC de los tanques de gas pequeños es una interacción de las propiedades del material, el diseño y el procesamiento, así como la presencia de una influencia química, es decir, la gasolina.
Las tensiones internas son un hecho de la vida en el moldeo por inyección. Las presiones y los índices de fluidez asociados con el llenado y empaquetado de un molde y los cambios volumétricos que acompañan al proceso de enfriamiento producirán varios cientos de libras por pulgada cuadrada de tensión en el moldeado, incluso en una pieza bien diseñada.
El HDPE es el polímero comercial con el mayor grado de cristalinidad, y a medida que aumenta la densidad aumenta también el grado de cristalinidad. Esto incrementa el cambio en el volumen asociado con el enfriamiento. Además, suponiendo que un polímero es capaz de cristalizar, hay una ventana de oportunidad para que se produzca la cristalización. La temperatura del material debe estar por debajo de su punto de fusión, pero por encima de su temperatura de transición vítrea (Tg). La Tg del polietileno es ‒130 °C (‒202 °F).
La temperatura más baja registrada en nuestro planeta, que ocurre en la meseta antártica oriental, es de ‒98 °C (‒144 °F). Esto significa que cada pieza de polietileno en uso en cualquier lugar de la Tierra es capaz de cristalizar durante el tiempo que exista.
Afortunadamente, la mayor parte de la organización estructural asociada con la cristalización en polietileno se realiza en las primeras 48 horas después de la producción de la pieza. Otro cambio incremental medible ocurre en las siguientes cuatro a seis semanas. Pero en algún nivel, el proceso siempre está ocurriendo y ocurrirá más rápidamente en ambientes más cálidos.
La soldadura en placa caliente de piezas recién fabricadas es otro elemento a tener en cuenta. Una vez que las mitades de la carcasa están unidas, el enfriamiento continuo y la contracción de las piezas hace que la tensión se acumule localmente cerca de la zona de soldadura, donde el movimiento del polímero es limitado por la soldadura. Y luego está la influencia de la gasolina en las propiedades del polietileno.
El polietileno es un material no polar y, por lo tanto, tiende a absorber fluidos que también son no polares. Estos incluyen cualquier cosa hecha de hidrocarburos como aceite mineral, aceite de motor y gasolina.
Los estudios realizados durante las investigaciones de análisis de fallas mostraron que el polietileno puede absorber 7-8 % de su peso en gasolina y la fuerza y la disminución del módulo en alrededor del 50 % como consecuencia. Como era de esperar, las piezas también cambian de dimensiones a medida que se lleva a cabo esta absorción. Todos estos factores contribuyen al desarrollo de la tensión.
Al examinar los fracasos surgieron algunos patrones. En primer lugar, las grietas siempre aparecían en la mitad inferior del ensamblaje, donde la exposición a la gasolina sería más constante.
En segundo lugar, las grietas tendían a originarse cerca de la junta de soldadura térmica.
En tercer lugar, solo un pequeño porcentaje de los diseños de tanques eran susceptibles a fallas. Las pruebas aceleradas realizadas a una temperatura elevada durante un periodo de varios meses mostraron que la mayoría de los diseños no presentaban fallas. Esto ayudó a distinguir entre el mecanismo de agrietamiento por estrés ambiental, ESC, y una respuesta química pura del polietileno al entorno de aplicación. El ataque químico ocurre independientemente del diseño.
El polietileno es más susceptible al ESC a medida que aumenta la densidad. A densidades más bajas, las zonas no cristalizadas pueden absorber y administrar la energía asociada con el aumento de los niveles de tensión. A medida que la densidad del polímero aumenta, el contenido amorfo en el material disminuye. Esto aumenta la resistencia y la rigidez, pero reduce la tenacidad.
Los polietilenos de menor densidad pueden soportar niveles más altos de tensión antes de que fallen. Pero a medida que aumenta la densidad, sube la probabilidad de fractura frágil. La falta de comprensión de la interacción entre el peso molecular y la densidad dio lugar a un problema de rendimiento muy costoso que casi resultó en regulaciones que exigían la construcción multicapa de estos pequeños tanques de gasolina, que no están dentro del sector automotor.
El problema fue resuelto por un proveedor de materiales que reconoció una oportunidad de mercado y desarrolló una calidad con un MFR de 3.3 g/10 min y una densidad de 0.945 g/cm3. Aparentemente, un MFR de 3.3 estaba lo suficientemente cerca de 4.0, y los procesadores estaban dispuestos a probarlo. Pero la clave fue el regreso a una densidad más baja para resolver el problema de agrietamiento.
En nuestra próxima entrega veremos algunos aspectos secundarios de las propiedades del polietileno que hoy forman parte de las opciones de selección de materiales disponibles. Estos influyen en el rendimiento y el procesamiento. Y, como suele ser el caso, a medida que el rendimiento mejora, el procesamiento se vuelve más difícil.
Acerca del autor
Michael Sepe
Consultor independiente sobre materiales y procesamiento, a nivel global, cuya compañía, Michael P. Sepe, LLC, tiene su sede en Sedona, Arizona. Tiene más de 40 años de experiencia en la industria del plástico y asesora sus clientes en selección de materiales, diseño para manufactura, optimización de procesos, solución de problemas y análisis de fallos. Contacto: (928) 203-0408 • mike@thematerialanalyst.com
Contenido relacionado
Calentadores solares mejoran calidad del agua con HDPE
El Centro de Investigación en Química Aplicada (CIQA) trabaja en el cuidado del agua mediante calentadores solares fabricados con polietileno de alta densidad. Esta innovadora tecnología contribuye a mejorar la calidad del agua y a preservar este recurso vital de manera sostenible.
Leer MásHDPE tiene potencial para abrir más alternativas sustentables: ALPLA
De acuerdo con ALPLA, el polietileno de alta densidad (HDPE) promete revolucionar el reciclaje en México gracias a sus propiedades y potencial sustentable.
Leer MásFundamentos del polietileno: el peso molecular y la densidad
Las propiedades del PE se pueden ajustar cambiando el peso molecular o alterando la densidad. Si bien esto aumenta las posibles combinaciones de las propiedades, también requiere que la especificación para el material sea precisa.
Leer MásResinas de polietileno: monomodales vs vimodales en empaques
Descubra las diferencias clave entre las resinas monomodales y bimodales. Impacto, aplicabilidad y sostenibilidad en la industria de empaques.
Leer MásLea a continuación
Los fundamentos del polietileno: papel de la densidad
Las piezas de PE pueden fallar cuando se selecciona una densidad inapropiada. Echemos un vistazo a algunos ejemplos y examinemos qué sucedió y por qué.
Leer MásFundamentos del polietileno: el peso molecular y la densidad
Las propiedades del PE se pueden ajustar cambiando el peso molecular o alterando la densidad. Si bien esto aumenta las posibles combinaciones de las propiedades, también requiere que la especificación para el material sea precisa.
Leer MásFundamentos del polietileno: conceptos básicos
Podríamos pensar que sabemos todo lo que hay que saber sobre un material que fue comercializado hace 80 años. Sin embargo, no es así cuando hablamos de PE. Empecemos por repasar los conceptos básicos.
Leer Más