Moldes: la verdad sobre los sistemas de expulsión guiada
Cuándo, dónde, cómo y por qué utilizar sistemas de expulsión guiada en sus moldes.
Compartir
Cuando se instalan pines y casquillos guía dentro de la carcasa del expulsor, se denomina sistema de expulsión guiada. Los sistemas de expulsión guiada aumentan en gran medida la longevidad de un molde, pero también incrementan el costo. Entonces, ¿cuándo son necesarios y cuándo no?
Para responder a esta pregunta necesitamos definir qué ventajas aporta un sistema de expulsión guiada. La respuesta breve es que soportan, guían y alinean las placas expulsoras, lo que a su vez soporta, alinea y guía los pines de retorno, los pines de expulsión, las camisas, las cuchillas, los elevadores y cualquier otro componente asociado.
Un sistema de expulsión guiado evita que la gravedad transfiera el peso de las placas expulsoras a los componentes del molde. Esa es la función de apoyo del sistema. También ayudará a evitar que las placas expulsoras se inclinen y se atasquen debido a una longitud desigual de los vástagos de expulsión de la máquina, a un patrón de expulsión descentrado (debido a un casquillo de bebedero descentrado) o a una disposición no simétrica de los pines de expulsión (más pines en un lado del molde que en el otro). Esta es la función de guía del sistema. Lo más importante es que garantizan que los pines de expulsión, camisas, cuchillas, etc., se encuentren en la ubicación adecuada y se desplacen hacia delante y hacia atrás, de forma perfectamente paralela a la línea central del molde. Es la función de alineación del sistema.
Para ayudarme a entender mejor la mecánica de algo me enseñaron a pensar en términos de extremos. Teniendo esto en cuenta, la placa de expulsión y retención en una base de molde estándar de 35½ × 23¾ de pulgada tiene un peso combinado de 350 libras. Sin un sistema de expulsión guiada, esas 350 libras son soportadas por los componentes conectados a las placas de expulsión. Esto causará que los agujeros de los pines de expulsión se alarguen y se generen defectos en las piezas moldeadas. También aumentarán las probabilidades de que los componentes se agarroten, se doblen y se desgasten prematuramente. En resumen: un sistema de expulsión guiada ayuda a evitar piezas defectuosas, tiempos de paros y los costos de reparación del molde.
Entonces, la respuesta a cuándo un molde debe tener un sistema de expulsión guiada se basa en cuatro factores principales: 1) la vida útil deseada del molde (en ciclos); 2) el peso de las placas de expulsión; 3) la cantidad y complejidad de los componentes de expulsión, y 4) la dureza de los insertos del núcleo. He visto muchos moldes de aluminio sin guía con problemas de expulsión y rebabas en un tiempo muy corto. No sé si la vida útil del molde fue proyectada para ser bastante corta o si el factor impulsor fue mantener el costo del molde bajo. Independientemente de la razón, los problemas de rebaba y desgaste empezaron a aparecer alrededor de los 25.000 ciclos.
Algunos fabricantes de moldes creen que los pines de retorno soportan adecuadamente las placas de expulsión. Esta creencia resulta casi siempre incorrecta. Si alguna vez se ha subido a un balancín, sabe que es la ventaja mecánica. Las fuerzas son iguales en ambos extremos cuando el punto de pivote está en el centro del balancín. Pero cuanto más se acerque el punto de pivote a uno de los extremos y acorte su longitud, mayor será la ventaja mecánica conseguida por la mayor longitud del lado opuesto.
Ahora bien, si piensa en los pines de retorno en un molde, el punto de pivote está en el extremo de la superficie de apoyo, no muy lejos de la línea de separación. Todo el peso de las placas de expulsión está en el otro extremo del pin. Cuanto mayor sea la distancia entre las placas expulsoras y este punto de pivote o de apoyo, mayor será la ventaja mecánica y la fuerza resultará considerablemente superior a las 350 libras mencionadas, lo que puede provocar fácilmente desgaste y daños. Los moldes con carreras de expulsión largas y placas B gruesas presentan una ventaja mecánica sobre los que tienen carreras cortas y placas finas, por ello tienen una mayor necesidad de un sistema de expulsión guiada. Supongo que este es el quinto factor que determina si un molde necesita o no un sistema de expulsión guiada.
La expulsión guiada constituye una característica opcional de la mayoría de los proveedores de bases de molde. Eso es comprensible, además de beneficioso. Pueden recomendar tamaños y ubicaciones para los pines y casquillos, pero usted tiene la opción de especificar la cantidad, el tamaño, la ubicación y el método de instalación que mejor se adapte a su diseño de molde.
Revisé las recomendaciones y especificaciones de los sistemas de expulsión guiada de uno de los mayores proveedores de bases de molde y encontré algunos datos interesantes. Este proveedor ofrecía 43 longitudes y anchos diferentes de bases de molde estándar, desde las más pequeñas de 7⅞ × 7⅞ pulgadas hasta 35½ × 23¾ de pulgada. De estos 43 tamaños diferentes, recomendaban que solo tres de ellos tuvieran dos casquillos de expulsión guiada: los tres moldes de tamaño más pequeño. Para los tamaños restantes aconsejaban utilizar cuatro casquillos. Nunca he visto un molde con más de cuatro pines y casquillos de guía, pero imagino que los moldes muy grandes podrían beneficiarse del uso de seis o, incluso, ocho.
Aunque los diámetros de los casquillos en los moldes más grandes son correspondientemente mayores para soportar el mayor peso de las placas, hay que tener en cuenta la ubicación de estos en relación con el patrón de expulsión de la máquina. Si la distancia entre los vástagos de expulsión de la máquina y los casquillos de expulsión guiada es relativamente larga, se corre el riesgo de doblar las placas de expulsión. Si estas placas son finas o de un material blando, hay gran probabilidad de que esto ocurra, aún con placas de acero en grosores estándar. Nota: Esta es una de las razones por las que añadir más tornillos que conecten la placa de expulsión con la placa de retención de los expulsores suele ser una buena idea.
La capacidad de estos sistemas para guiar y alinear con precisión las placas de expulsión se basa en dos factores principales: la longitud del casquillo y la holgura entre el pin guía y el casquillo. La mayoría de los casquillos de expulsión guiada vienen en dos longitudes: 1½ y 1¾ de pulgada. La holgura entre el pin guía y el casquillo oscila entre 0.0010 y 0.0020 pulgadas. Si hace cálculos, el ángulo máximo en el peor escenario es de apenas 0.076° para el casquillo de 1½ pulgadas, y de 0.065° para el casquillo de 1¾ de pulgada. Esto le da una buena indicación de lo precisos que deben ser los agujeros pasantes y el avellanado para los pines y los casquillos en el molde. El mandrinado de todas las placas ayudará a garantizar la posición y la alineación adecuadas.
A pesar de esta alta precisión, en ocasiones puede ser necesario un mejor guiado. Un ejemplo común es cuando un molde familia de dos cavidades está procesando solo una de las cavidades ―o cuando el molde tiene solo una cavidad desplazada de la línea central―. Independientemente del patrón de expulsión de la máquina, las fuerzas de resistencia tratarán de mover las placas de expulsión en ángulo. En casos como este, el uso de casquillos guía más largos ayudará a evitar cualquier desgaste prematuro o rozamiento. Es posible que se requiera una placa más gruesa o que se perforen las placas para permitir que los casquillos guía más largos ―que ahora sobresalen de las placas expulsoras― acompañen toda la carrera del expulsor. Nota: No se puede evitar que esto ocurra simplemente por utilizar dos vástagos de expulsión desplazados en la máquina. En lugar de desgastar el sistema de expulsión guiada del molde, se va a desgastar el sistema de expulsión de la máquina de moldeo.
Dado que un pin guía cilíndrico se monta en un orificio cilíndrico ligeramente mayor del casquillo, el contacto es lineal, no circunferencial. El contacto lineal se desgasta mucho más rápido que el circunferencial. Obviamente, cuanto más dura sea la superficie del pin y del casquillo, menor será el desgaste. Los pines guía estándar están nitrurados con una dureza superficial de 58 a 62 Rockwell C. Los casquillos guía están disponibles comercialmente en bronce y autolubricados, pero hay que tener cuidado. Varios proveedores no indican la dureza de sus casquillos (esto me molesta).
¿Cómo puede un fabricante de moldes tomar la decisión acertada? También pongo en duda algunas de las especificaciones declaradas por estos proveedores. Por ejemplo, un proveedor dice que sus casquillos de bronce tienen una dureza superficial de 65 a 74 Rockwell C. Desgraciadamente, solo porque lo diga un catálogo no significa que sea necesariamente cierto. La mayoría de los casquillos de expulsión guiados tienen una dureza de 90 a 180 Brinell, que ni siquiera se acerca a la dureza del pasador guía. De hecho, ni siquiera están en la escala Rockwell C. Sin embargo, es posible encontrar proveedores que ofrecen casquillos de expulsión guiados de acero endurecido (48 a 50 Rc), con un diámetro interior bronceado y con ranuras de engrase internas. Estos son mis casquillos preferidos.
Un proveedor de componentes para moldes presentó recientemente un casquillo de expulsión guiada que emplea filas de rodamientos de bolas en el diámetro interior. Dependiendo del diámetro, hay entre seis y ocho filas por casquillo. Se trata de un tipo único de rodamiento “lineal”, porque las filas de rodamientos de bolas no son paralelas a la línea central del casquillo. Están en un ligero ángulo. Por lo tanto, en lugar de un único contacto lineal con el pasador guía, hay docenas de puntos de contacto alrededor del perímetro del pasador guía. Los cojinetes de bolas están endurecidos a 60 o 62 Rc. Esto puede ser un problema, ya que suelen ir sobre un pin guía nitrurado con la misma dureza superficial. Para esta aplicación sería mejor utilizar un pin angular en lugar de un pin guía. La mayoría de los pines angulares disponibles en el mercado, aunque no todos, tienen una dureza superficial nitrurada de 65 a 74 Rc.
He utilizado casquillos lineales con rodamientos de bolas en moldes con placas de separación, tres placas y de placas flotantes. Son extremadamente precisos. El único problema que he tenido es que pueden funcionar demasiado bien, permitiendo que se muevan con muy poca fuerza. Incluso pueden “rebotar” si la carrera de apertura es bastante rápida o si las placas no están amortiguadas al final de su carrera. Eso puede ser un peligro para la seguridad y posiblemente una de las razones por las que ya no los ofrece la mayoría de los proveedores de componentes de moldes.
Pero los casquillos de bolas son una aplicación excelente para un sistema de expulsión guiada. La única preocupación que tendría es la necesidad de una buena lubricación, con aceite, no con grasa. La grasa retiene la suciedad y el polvo más fácilmente que el aceite, lo que puede afectar a la longevidad de los casquillos. Como muchos de ustedes probablemente saben o han experimentado, la aplicación de grasa a un casquillo autolubricado con carbón puede hacer que se desgaste prematuramente. El mismo problema se aplica a los rodamientos de bolas. No hay ningún problema en utilizar casquillos con cojinetes de bolas para los moldes médicos que funcionan en un entorno de sala limpia.
Hay dos métodos principales para instalar los pines guía en un sistema de expulsión guiada. Cada uno tiene sus pros y sus contras. La primera forma es instalar los pines guía en la parte posterior de la placa de sujeción de expulsión (o de la carcasa del expulsor, si la placa de sujeción y los rieles están soldados), como se muestra en la Fig. 1. Este método, un poco más rápido y fácil de mecanizar, es el más común con las bases de molde de la serie B. También elimina prácticamente el problema común con los circuitos de agua, pernos, enclavamientos, insertos del núcleo, etc., que estorban. La desventaja de este método es que cuando se quita la placa de sujeción que sostiene los pines de guía, no hay soporte para las placas de expulsión. Todo el peso recae ahora sobre los pines. Esto no suele ser un problema si se mueven las placas de expulsión a su posición totalmente adelante.
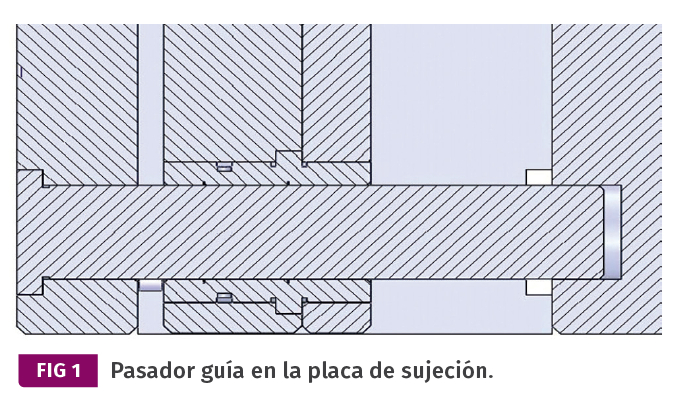
FIG 1. Pasador guía en la placa de sujeción.
Hay dos variantes principales sobre cómo instalar los pines guía del expulsor
El otro método consiste en instalar los pines guía desde la parte delantera de la placa B, suponiendo que se trata de una base de molde de la serie A, como se muestra en la Fig. 2. La ventaja de este método es que resulta más fácil, rápida y segura la limpieza y el reemplazo de los pines para el fabricante de moldes. Este método tiene un pequeño inconveniente. Cuando se retiran la placa de sujeción, la placa de expulsión y los pines de expulsión, siguen sobresaliendo los pines guía de la parte posterior de la placa B. Esto dificulta un poco darle la vuelta al molde sobre su espalda, de forma segura.
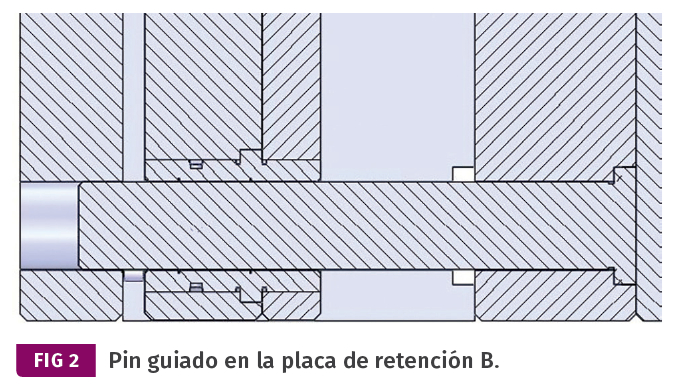
FIG 2. Pin guiado en la placa de retención B.
Casi todos los pines guía tienen un reborde sobredimensionado o ajustado a presión, normalmente de 0.0005 a 0.0010 pulgadas por encima del valor nominal. La longitud de este reborde varía según el diámetro del pin y el fabricante. Tenga en cuenta que, dependiendo de la longitud del ajuste a presión, existe la posibilidad de que interfiera con el casquillo. Si interfiere, simplemente rectifique la cantidad necesaria. Los fabricantes de moldes que quieran hacer lo mejor de lo mejor, deben rectificar todos los hombros de ajuste a presión y reducir el tamaño de los agujeros en los que entran en 0.0005 pulgadas. Es posible que tenga que congelar los pernos y calentar la placa para instalarlos, pero ahora la superficie de apoyo es todo el espesor de la placa.
Hay otra cuestión que afecta ambos métodos de instalación. Los moldes se construyen a temperatura ambiente (68 °F), pero rara vez funcionan a esta temperatura. Por ejemplo, digamos que el molde es de 35½ × 23¾ de pulgada y está procesando un material de grado de ingeniería a 300 °F con aceite caliente. Las placas expulsoras suelen estar hechas de acero SAE 1030, que tiene un coeficiente de expansión térmica de 6,5 × 10-6. Por lo tanto, las placas de la cavidad y del núcleo se expandirán 0.036 pulgadas a lo ancho y 0.054 pulgadas a lo largo. Pero las placas expulsoras apenas se expandirán y es muy probable que los elementos empiecen a atascarse. Como mínimo, los agujeros de los expulsores en los núcleos comenzarán a alargarse, y es posible que solo lo sepa cuando las piezas comiencen a mostrar rebabas.
La forma de superar este problema potencial es utilizar una placa expulsora más gruesa y perforar algunos canales de refrigeración en ella. Esto igualará el problema de la expansión térmica. Además, es mejor montar los pines guía en la placa de retención B de una base de molde de la serie A, y proporcionar suficiente espacio libre en la placa de sujeción de expulsión para acomodar la expansión entre los pines guía. De este modo, la placa de sujeción del expulsor no se calentará de forma significativa y transferirá lentamente el calor a la placa móvil de la máquina. También puede añadir una placa aislante en la parte posterior de la placa de sujeción. Tenga en cuenta que las placas aislantes solo reducen la velocidad de transferencia de calor. No impiden la transferencia de calor.
Si los pines guía se instalan en la placa de sujeción, pero no entran en la parte posterior de la placa B, como se muestra en la Fig. 3, es posible que no tenga un problema de expansión térmica entre los pines y los casquillos guía, pero seguirá el mismo problema de expansión con los pines de retorno, pines de expulsión, camisas, cuchillas, etc. Además, se pierde una cantidad significativa de capacidad de carga cuando solo se ancla un extremo de los pines guía, en lugar de ambos.
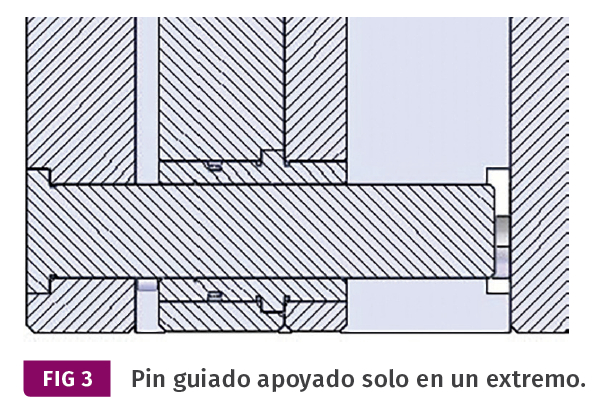
FIG 3. Pin guiado apoyado solo en un extremo.
Si pide una base de molde con el sistema de expulsión guiada preinstalado, el casquillo tendrá un ajuste deslizante en la placa de retención delantera y un ajuste a presión en la placa de expulsión trasera. Muchos fabricantes de moldes preferirían que esto fuera al revés. Aunque hay más superficie de apoyo en la placa expulsora más gruesa, a menudo es difícil (y peligroso) montar y desmontar el molde en esta condición. Si los casquillos se colocan a presión en la placa de retención del expulsor, el fabricante de moldes puede retirar fácilmente la placa del expulsor sin que el peso de la placa de retención del expulsor se aplique a los pines de expulsión. También hay menos posibilidades de que se desprendan las pequeñas llaves o pasadores utilizados para orientar los pines de expulsión. Sea cual sea la forma que elija, es beneficioso añadir dos o cuatro agujeros pasantes roscados en la placa expulsora. A continuación puede atornillar pernos estándar para separar o “levantar” las placas con cáncamos. Este es un método mucho más delicado que el uso de barras de palanca en las esquinas, suponiendo que las placas tengan ranuras para barras de palanca.
Si el espacio disponible dentro de la carcasa del expulsor es un problema, los pines guía también pueden servir de pilares de apoyo, como se muestra en las figuras 4 y 5. Utilice un tamaño de casquillo correspondiente a la cantidad de apoyo que necesite. El diseño mostrado en la Fig. 4 puede utilizarse para moldes pequeños, como los insertos MUD.
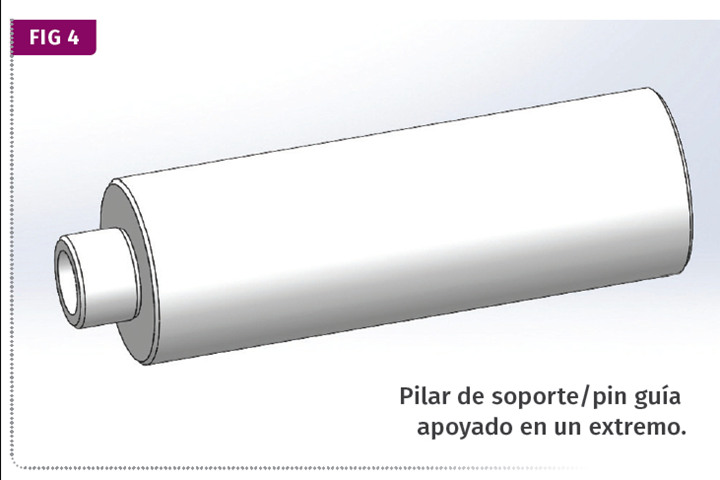
FIG 4 Pilar de soporte/pin guía apoyado en un extremo.
El diseño mostrado en la Fig. 5 se apoya en ambos extremos y es mejor para moldes más grandes con placas más pesadas. Cualquiera que sea el método utilizado, asegúrese de que el pilar de soporte/pin guía esté nitrurado para una mayor duración. El centro de los pines guía nitrurados son lo suficientemente suaves como para mecanizarlos con facilidad, alrededor de 25 a 35 Rc.
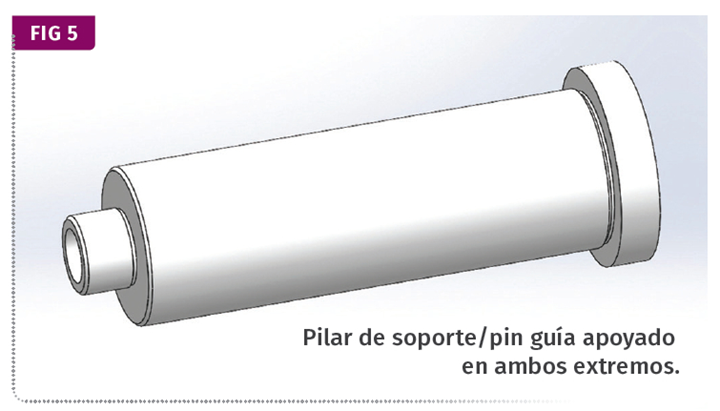
FIG 5. Pilar de soporte/pin guía apoyado en ambos extremos.
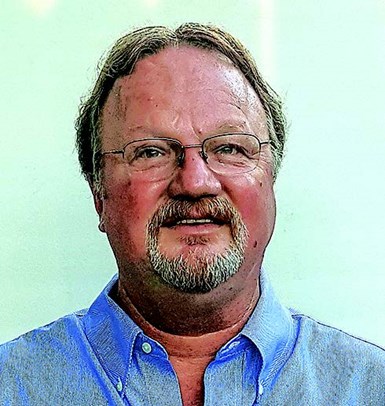
Jim Fattori
Jim Fattori es un moldeador de inyección de tercera generación con más de 40 años de experiencia en moldeo. Es el fundador de Injection Mold Consulting LLC, y también es ingeniero de proyectos para una gran moldeadora de múltiples plantas en Nueva Jersey. Contacto: jim@injectionmoldconsulting.com; injectionmoldconsulting.com.
Contenido relacionado
Meximold 2024: la feria líder en moldes y moldeo regresa a Querétaro
Meximold 2024 se llevará a cabo los días 9 y 10 de octubre en el Querétaro Centro de Congresos, con la participación de más de 140 compañías expositoras, un programa de conferencias de alto nivel y oportunidades de networking y negocios B2B.
Leer MásChecklist para la fabricación exitosa de moldes inyección de plástico
Una guía integral sobre cómo optimizar el proceso de diseño y construcción de moldes de inyección de plástico, centrada en la prevención de problemas y la mejora continua.
Leer MásTratamientos químicos en sistemas de transferencia de calor
Entienda el riesgo de biofilmes y corrosión en sistemas de agua y cómo un tratamiento químico adecuado puede extender la vida útil de su equipo.
Leer MásSimulación avanzada vs. tradicional en moldeo por inyección
Explore el impacto del moldeo virtual en la producción de plásticos. ¿Cómo anticipar defectos y adaptar procesos de inyección? Encuentre respuestas aquí.
Leer MásLea a continuación
Cómo dimensionar compuertas, canales y bebederos, parte 5: consejos y trucos
Haga que el tamaño del bebedero, canales y compuerta del molde se acerquen a los ideales la primera vez.
Leer MásMoldes, de vuelta a lo básico: resortes de compresión
Algunos talleres de moldes insisten en que todos sus moldes tengan resortes para devolver las placas de expulsión. Afortunadamente, hay muchos para elegir. Este artículo se centra en los resortes de compresión para moldes de inyección.
Leer MásLo que debe saber sobre las guías y casquillos de moldes
Profundice en las especificaciones de casquillos y guías en moldes. Conozca las tolerancias dimensionales y cómo garantizar un funcionamiento óptimo.
Leer Más