Cómo dimensionar compuertas, canales y bebederos, parte 5: consejos y trucos
Haga que el tamaño del bebedero, canales y compuerta del molde se acerquen a los ideales la primera vez.
Compartir
Lea a continuación
Nota del editor: Esta es la quinta parte de un especial con cinco entregas. Puede encontrar las ligas de la serie completa a continuación:
Este mes examiné cuatro décadas de notas, bocetos a mano y fotografías para descubrir una serie de consejos y trucos valiosos relacionados con esta serie de cinco partes sobre compuertas, canales y bebederos. Por lo tanto, la conclusión de la serie de este mes será, simplemente, una lista con información útil.
Canales
- Completamente redondos, parabólicos y trapezoidales son los únicos tres tipos de canales que se deben utilizar en un molde de inyección, en ese orden.
- Utilice siempre diseños de canales geométrica o “naturalmente balanceados” para moldes multicavidad. Los moldes de múltiples cavidades tienen inherentemente problemas de balanceo. No agrave el problema con espinas de pescado, escaleras u otros tipos de diseños desbalanceados.
- Algunos diseños pueden tener una gran masa en las intersecciones de ramales. Estos, a menudo, se pueden optimizar (reduciendo masa) sin afectar el flujo o la presión del material, como se muestra en la Fig. 1.
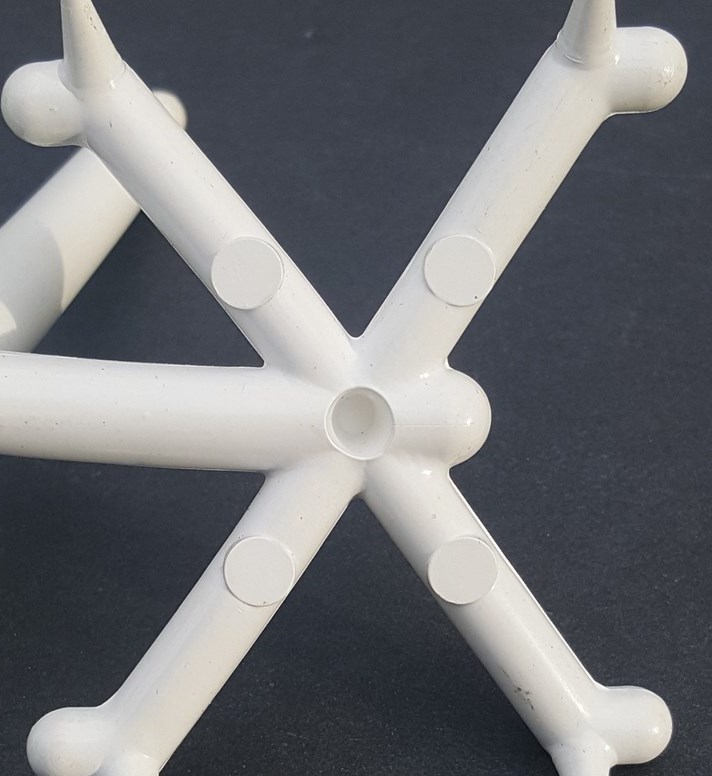
Fig. 1 Una intersección optimizada.
- Un ingeniero inteligente grabó texto en el canal de un molde familia para ayudar a los operadores a identificar piezas de aspecto similar y que pudieran clasificar y ensamblar fácilmente, como se muestra en la Fig. 2. Grabar el número de cavidad en el canal también es útil cuando las piezas son muy pequeñas o los requisitos estéticos no permiten un número de cavidad en la pieza.
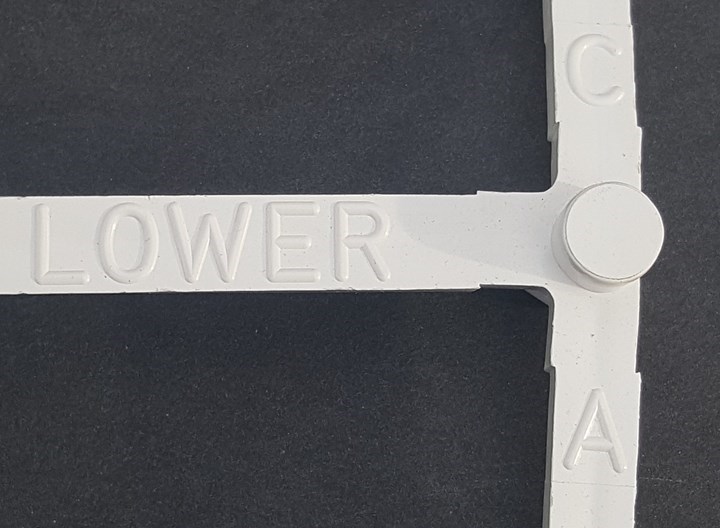
Fig. 2 Un canal grabado.
- Nunca mecanice un canal en una línea de partición de dos o más insertos de molde. La presión de inyección intentará separar los componentes y provocará una rebaba que podría hacer que el canal no expulse correctamente.
- Diseñar el molde con un sistema de canal insertado aparte costará un poco más, pero tiene múltiples beneficios, especialmente para moldes de larga duración.
- Cualquier ajuste de tamaño al canal es más rápido y más fácil de mecanizar.
- Puede ser más fácil colocar un canal de enfriamiento separado en el inserto, lo que puede ayudar a reducir el tiempo del ciclo.
- En caso de rebabas en la línea de partición, el inserto del canal se puede rectificar y calzar. Esto elimina la necesidad de realizar otros ajustes de altura en las cavidades, enclavamientos, levas o cierres.
- Los insertos pueden estar hechos de un material más económico, como un acero de herramientas de alta dureza para materiales abrasivos, o materiales térmicamente conductores para ciclos más rápidos.
- Las trampas de rebaba son beneficiosas en cualquier sistema de canal frío, ya sea un molde de dos placas, tres placas o de placas de separación.
- Agregue un rebose en cada intersección del canal. Esto es particularmente importante para los moldes de placas de separación cuando no hay un pozo frío enfrente del bebedero. La longitud del rebose debe ser de 1.0 a 1.5 veces el diámetro o ancho del canal. Los reboses funcionan muy bien, como se muestra en la Fig. 3.
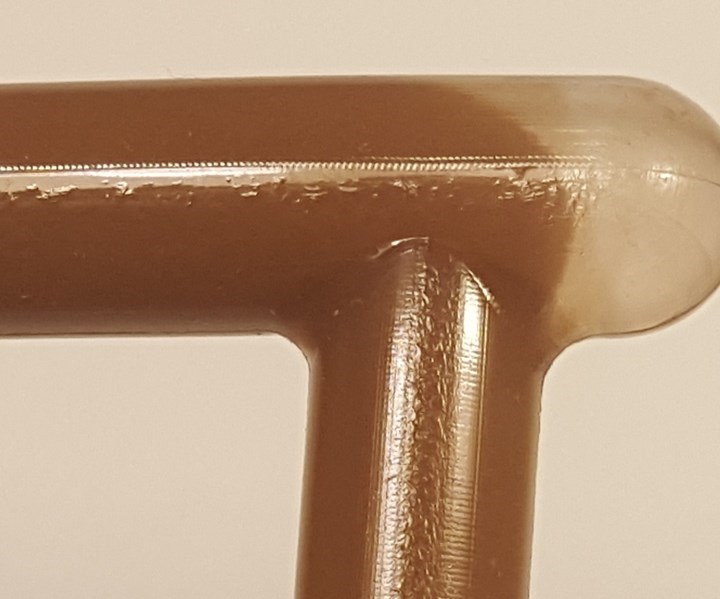
Fig. 3 Prueba que los reboses funcionan.
- La Fig. 4 muestra dos diseños de canales diferentes. Ambos canales tienen sub-gates mecanizados en la mitad de inyección de un molde de dos cavidades. El canal de la izquierda es superior al de la derecha porque:
- El pozo frío es lo suficientemente grande como para atrapar y retener el plástico frío de la punta de la boquilla de la máquina.
- Los refuerzos ayudan a sacar el bebedero del casquillo sin separarse del canal. De lo contrario, el tiempo del ciclo aumenta hasta que la intersección masiva se solidifica lo suficiente.
- No hay extractores directamente debajo del sub-gate, evitando que se doblen cuando se abre el molde. Si el sub-gate no se dobla, podría romperse o producir escamas.
- Los sub-gates se alimentan del costado del canal, lo que permite un pequeño desbordamiento y una buena ubicación para agregar un venteo al canal.
- Los sub-gates tienen forma de cincel. Permiten ajustar el ancho y la profundidad, tal como una compuerta de borde, controlando independientemente la velocidad del flujo o el tiempo de sellado de la compuerta.
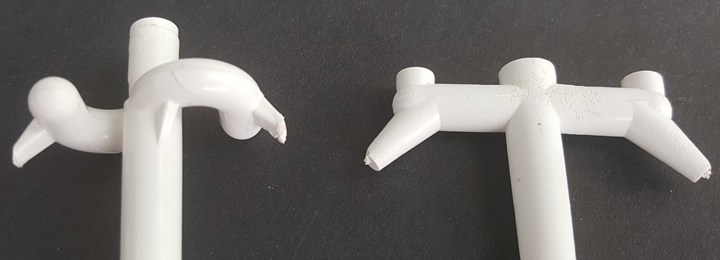
Fig. 4 Un diseño de canal realmente bueno y otro no tan bueno.
- Para materiales sensibles a la cizalladura o con relleno de vidrio, se prefieren los giros redondeados en lugar de las curvas a 90 grados.
- “Romper” o suavizar los bordes afilados del canal ayudará a reducir los esfuerzos en el material y a evitar que se agriete o rompa al ser expulsado. Los bordes afilados se encuentran, típicamente, donde el canal se encuentra con el bebedero, el pozo frío y las compuertas, así como en cada intersección.
Compuertas
- Es mejor alimentar las compuertas de bordes desde canales totalmente redondos.
- Los sub-gates se pueden alimentar desde un canal redondo, parabólico o trapezoidal.
- Para moldes de gran volumen (alrededor de 500,000 ciclos o más), considere incorporar insertos de compuerta reemplazables, especialmente para materiales abrasivos.
- Evite el uso de sub-gates si el material a moldear es abrasivo o si la cavidad está hecha de un metal blando, como aluminio o cobre. Se desgastarán rápidamente.
- Los sub-gates no necesariamente tienen que mecanizarse de forma paralela o perpendicular a la guía. Se pueden mecanizar en casi cualquier ángulo. Esto es útil cuando se debe inyectar una pieza a un ángulo pronunciado o cuando se desea cambiar la ubicación de una línea de soldadura.
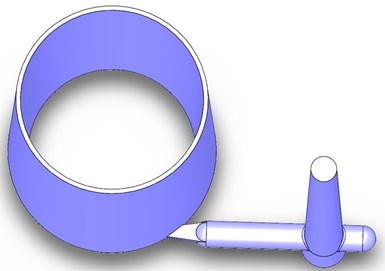
Fig. 5 Una parte con compuerta tangencial.
Una compuerta de borde o sub-gate que alimenta una pieza en un ángulo se denomina compuerta tangencial, como se muestra en la Fig. 5. A menudo se usa para evitar el desplazamiento o deformación del núcleo, reubicar una línea de soldadura o mejorar la resistencia de la soldadura. Sin embargo, puede provocar chorro libre o jetting dentro de la cavidad.
- Recuerde el efecto que tendrán en el molde la ubicación de la compuerta y el patrón de los canales de alimentación. La compuerta y el canal de la Fig. 6 pueden tener un diseño balanceado, pero causó que la cavidad y las mitades del núcleo del molde giraran en direcciones, lo que generó en las partes problemas de núcleo desplazado y diferencia en los espesores.
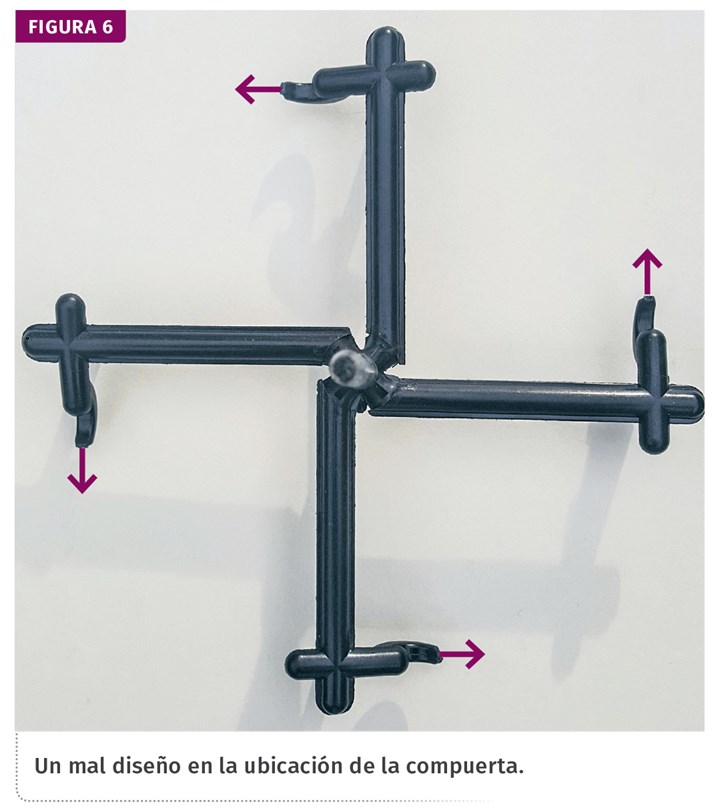
Fig. 6 Un mal diseño en la ubicación de la compuerta.
Balanceo de moldes familia
- El objetivo de equilibrar un molde familia es que todas las piezas terminen de llenarse al mismo tiempo, no que comiencen el llenado al mismo tiempo. Tenga esto en cuenta cuando realice un estudio de llenado.
- Una razón por la que se busca que todas las piezas de un molde familiar terminen de llenarse al mismo tiempo es para que todas reciban la misma cantidad de presión de empaque. Si no es así, se desperdicia material al empacar demasiado algunas cavidades. Otra razón es que las cavidades que están mal empaquetadas o demasiado empaquetadas presentarán problemas dimensionales porque tendrán una tasa de contracción diferente a la esperada.
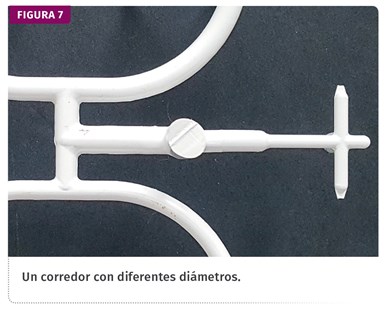
Fig. 7 Un corredor con diferentes diámetros.
El truco para ajustar un molde familia es ajustar el caudal de material en los canales que alimentan cada cavidad. Cambiar la profundidad o el ancho de la compuerta solo cambia la velocidad de llenado (mph). No cambia el caudal (pulg.3/seg). Cambiar la profundidad de la compuerta también crea diferentes tiempos de sellado, lo que lleva a que las piezas tengan diferentes presiones de empaque. Por lo tanto, para equilibrar correctamente los moldes de la familia, cambie los diámetros de los canales de cada cavidad, como se muestra en la Fig. 7.
- Si desea aumentar el tamaño de las compuertas, canales o bebedero en algún porcentaje, debe hacer cálculos. Por ejemplo, si siente que una compuerta de 0,050 pulgadas debe ser aproximadamente un 20 % más grande, no multiplique el tamaño de la compuerta por 1,2. Eso no es un 20 % más grande. En términos de área de flujo, es un 44 % más grande. Una forma fácil y correcta de determinar el tamaño de la nueva compuerta es usar la siguiente fórmula: DNEW = DESXISTING × √ (1 + porcentaje de aumento). En este caso, sería 0.050 × √ 1.2 = 0.055.
- Agregar un limitador de flujo corto, como se muestra en la Fig. 8, no es tan efectivo como reducir el diámetro de toda la rama del canal.
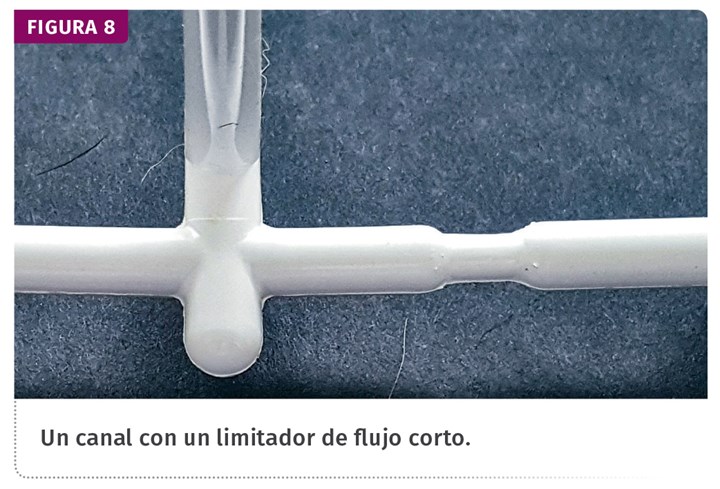
Fig. 8 Un canal con un limitador de flujo corto.
- Agregar secciones redundantes, como se muestra en la Fig. 9, solo tiene un efecto menor en el balanceo del sistema. También reducirá la ventana de procesamiento y aumentará la cantidad de desperdicio del proceso.
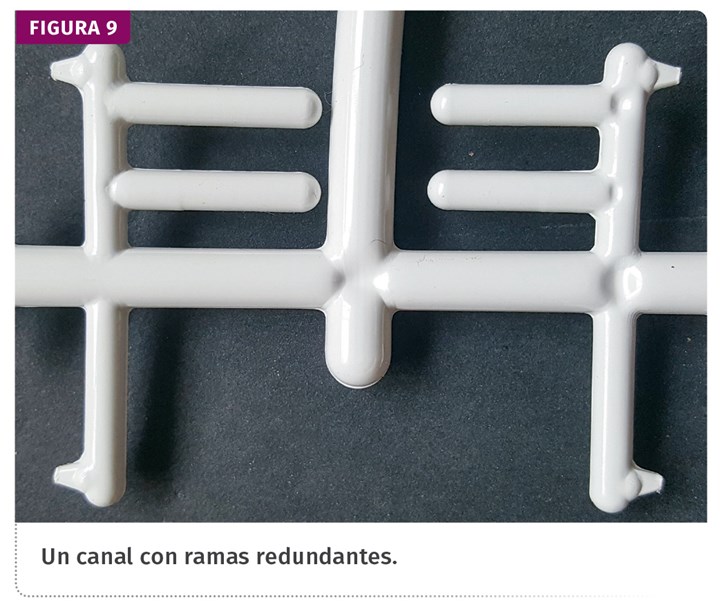
Fig. 9 Un canal con ramas redundantes.
Expulsión
- Los pines de expulsión deben estar a ras con la parte inferior del canal. Nunca deben entrar en el canal de flujo.
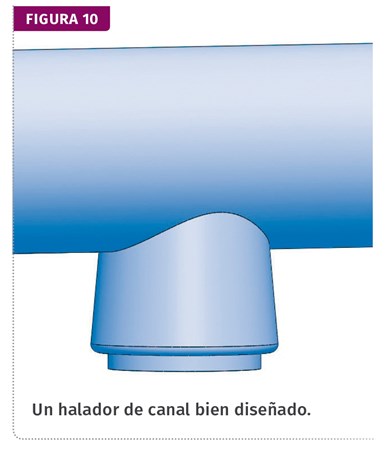
Fig. 10 Un halador de canal bien diseñado.
Se requiere un pin de expulsión recortado para expulsar un halador de canal cerca de un sub-gate mecanizado en el lado de la cavidad. En la Fig. 10 se muestra un buen diseño de halador. Observe cómo el pin de expulsión tiene un diámetro más pequeño que el halador y cómo este tiene un radio y un cilindro pequeño en la parte inferior. Este diseño minimizará el riesgo de que se formen escamas o virutas en la línea de partición.
• Los pines de expulsión recortados con punta cónica se utilizan para estabilizar el canal y evitar que se mueva o se vuelque durante la expulsión, como se muestra en la Fig. 11.
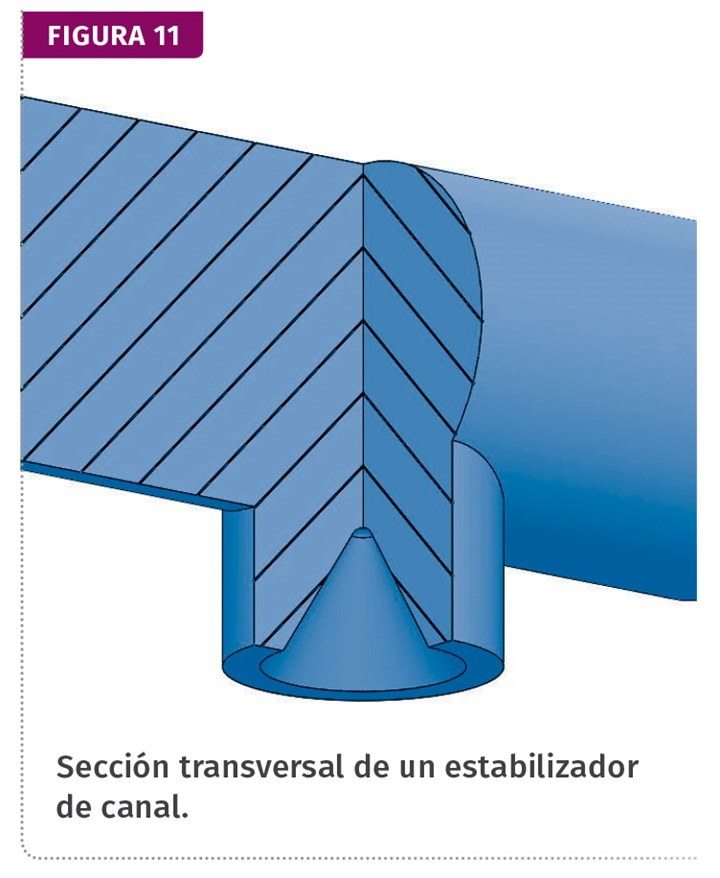
Fig. 11 Sección transversal de un estabilizador de canal.
- Idealmente se debe colocar un pin de expulsión en cada intersección del canal, porque a medida que el canal se contrae, intentará pegarse en las esquinas interiores.
- Si un canal circular se pega en el lado de la cavidad del molde, en lugar de usar haladores puede agregar cortes o contrasalidas en el lado de expulsión. Una contrasalida en forma de lágrima es mejor para prevenir escamas o virutas, como se muestra en la Fig. 12.
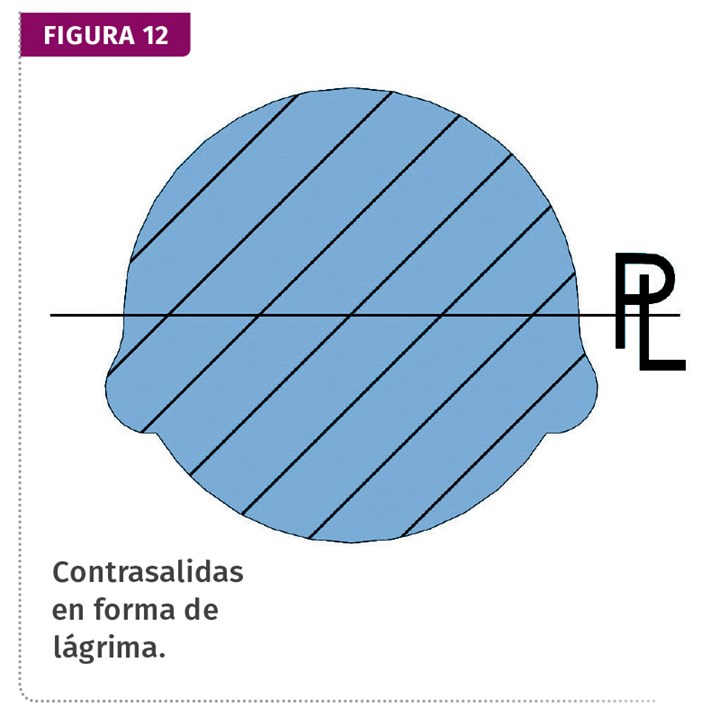
Fig. 12 Contrasalidas en forma de lágrima.
- Tenga en cuenta la ubicación de las retenciones o contrasalidas en el canal. Deben estar en o cerca de un pin de expulsión para evitar que el canal se doble o se reviente durante la expulsión.
- En la Fig. 13 se muestra una forma económica de retrasar la expulsión de un pin (o una pieza), sin tener que incorporar un sistema de expulsión de dos etapas. Los pasadores están bien soportados y tienen retorno positivo. Este diseño puede ayudar a reducir la descamación de las piezas con sub-gate.
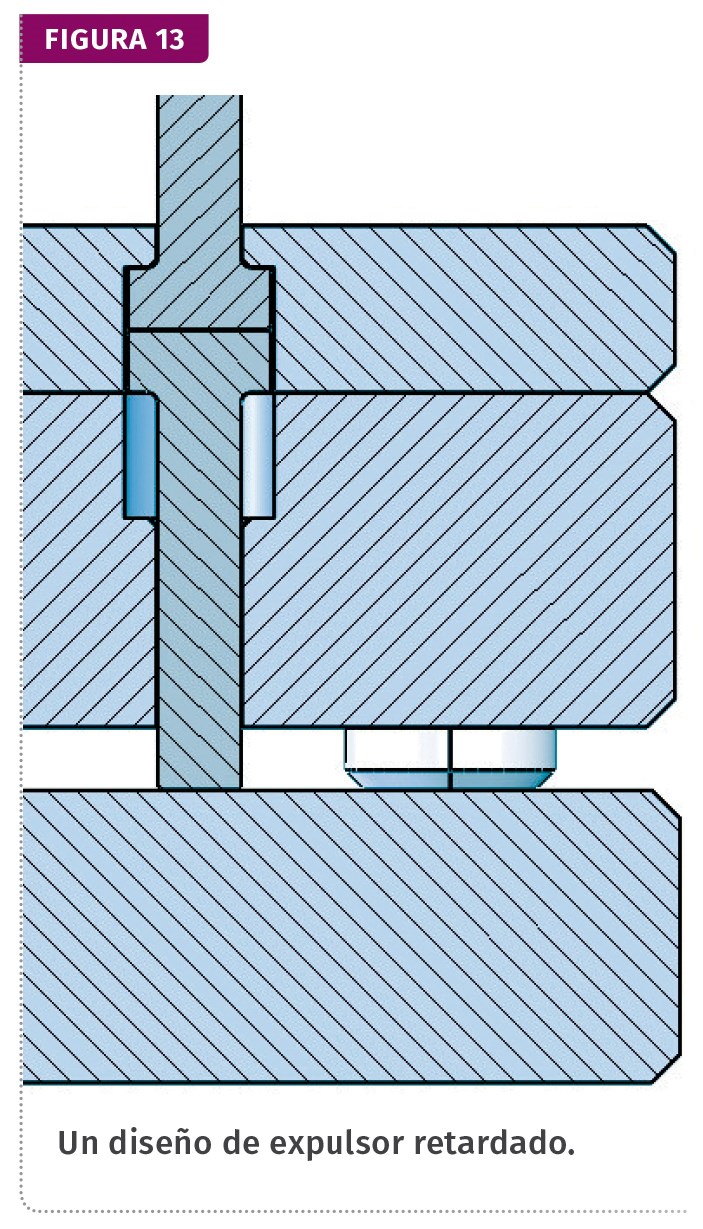
Fig. 13 Un diseño de expulsor retardado.
Venteo
• Especifique la ubicación, profundidad y ancho del sistema de venteo o ventilación en el plano del molde. No deje la ventilación a discreción del fabricante de moldes.
• A algunos fabricantes de moldes y moldeadores no les gusta agregar venteo hasta después del primer muestreo. Esto puede provocar un patrón de llenado erróneo. Como mínimo, agregue ventilación en el último lugar para llenar.
• Intente agregar un conducto de ventilación lo más cerca posible de la compuerta.
Nota. Un agradecimiento especial a Roy Glenn, diseñador y fabricante de moldes jubilado, por sus valiosos aportes a la columna de este mes.
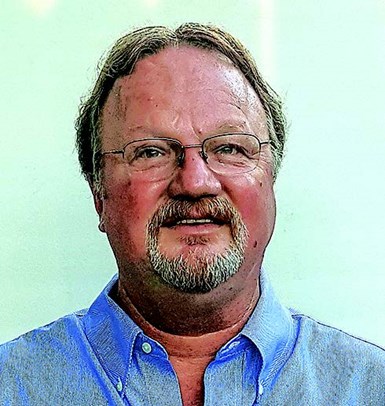
Jim Fattori
Jim Fattori es un moldeador de inyección de tercera generación con más de 40 años de experiencia en moldeo. Es el fundador de Injection Mold Consulting LLC, y también es ingeniero de proyectos para una gran moldeadora de múltiples plantas en Nueva Jersey. Contacto: jim@injectionmoldconsulting.com; injectionmoldconsulting.com.
Contenido relacionado
Clasificaciones de moldes de inyección de plásticos: análisis detallado
Examine los factores que influyen en la durabilidad de los moldes de inyección. Desde la complejidad del diseño hasta la selección de materiales, aprenda cómo optimizar la vida útil de los moldes.
Leer MásInyección y sistemas de colada caliente en Meximold Tech Preview
Conéctese en línea, y sin costo, los próximos 9 y 10 de agosto para ver un adelanto de las tecnologías y nuevos desarrollos que se verán en Meximold sobre inyección de plásticos y sistemas de colada caliente.
Leer MásEl costo de los productos de plástico inyectados
Análisis de los costos en productos inyectados de plástico y su relación con los aspectos tecnológicos involucrados en el proceso.
Leer MásEnfriamiento en moldes de inyección con CO2 líquido
Manufactura aditiva y enfriamiento localizado con CO2 son las nuevas soluciones que está empleando un moldeador de productos para las industrias médica y automotriz, con el fin de catapultar su productividad y calidad.
Leer MásLea a continuación
Cómo dimensionar compuertas, canales y bebederos, parte 4: acabado superficial de los canales
Cómo hacer que el tamaño del bebedero, canales y compuerta se acerquen a los valores ideales en el primer intento.
Leer MásCómo dimensionar compuertas, canales y bebederos, parte 3: compuertas de borde
Obtenga las dimensiones del bebedero y de las compuertas lo más cercano al tamaño ideal desde el primer intento.
Leer MásCómo optimizar el moldeo por inyección multicavidad
Explore los retos y las soluciones en canales calientes de moldeo por inyección para lograr un llenado uniforme y resultados consistentes.
Leer Más