Optimice los tiempos de empaque y sostenimiento para moldes de colada caliente
El uso de procedimientos científicos le ayudará a ponerle fin a la técnica de ensayo y error que consume mucho tiempo. Este artículo se centra en la fase de sostenimiento y cubre la técnica de optimización.
Con la mayoría de las herramientas, los moldeadores usan solo una fase después de la inyección volumétrica, para empacar y mantener el plástico en el molde, esta se denomina fase de sostenimiento. Sin embargo, el moldeador debe diferenciar entre las fases de empaque y de sostenimiento.
Para simplificar las cosas, en este artículo nos referiremos a la segunda fase como fase de sostenimiento y cubriremos la técnica de optimización. Luego, se diferenciarán las dos en la segunda parte de este artículo, que publicaremos en nuestra edición de agosto.
Para moldes de colada fría, los tiempos de sostenimiento se optimizan mediante un estudio de enfriamiento o sellado del punto de inyección, en el que el peso de la pieza se registra como una función del tiempo de sostenimiento. Cuando el punto se congela o sella, el peso de la pieza permanece constante en el tiempo. Para el ajuste del tiempo de sostenimiento, se toma como tiempo total, el tiempo más bajo en el que el peso de la pieza permanece constante y se adiciona un segundo.
En los sistemas de colada caliente o con válvula de cierre, por otro lado, el área del punto de inyección siempre tiene plástico fundido, y por lo tanto la curva de peso de la pieza no se aplana. Por esta razón, el método anterior no produce resultados aceptables.
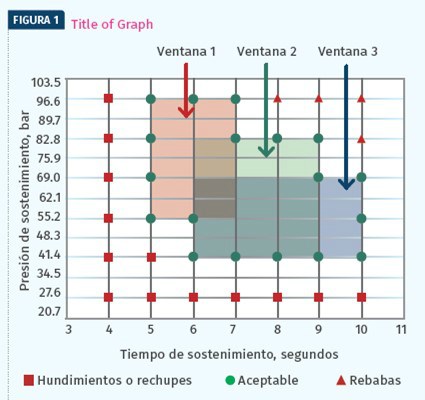
Los cuadrados rojos representan una parte con un defecto a presiones bajas y tiempos cortos; los triángulos rojos indican una parte con un defecto en el extremo superior de las presiones y tiempos; y los círculos verdes muestran una parte que es cosméticamente aceptable.
El tiempo y la presión de sostenimiento excesivos pueden causar defectos tales como rebabas, tensiones internas, y piezas que se adhieren al lado incorrecto del molde. Una presión insuficiente, por otro lado, puede causar piezas incompletas, hundimientos o rechupes y problemas dimensionales. Los moldeadores necesitan encontrar una combinación óptima de los tiempos y presiones de sostenimiento, y después llevan a cabo un DOE (Diseño de Experimentos) para optimizar los parámetros dentro de los límites disponibles.
Adicionalmente hay otros dos términos que necesitan explicación. El primero es la ventana de proceso cosmética (CPW) y el segundo es la ventana de proceso dimensional (DPW). La CPW se refiere a los límites del proceso dentro de los cuales pueden ser moldeadas piezas cosméticamente aceptables. Por otro lado, la DPW refleja los límites del proceso dentro de los cuales las piezas se pueden moldear de manera que sean dimensionalmente aceptables. La DPW está siempre dentro de la CPW.
A continuación se presenta el procedimiento para optimizar los tiempos de sostenimiento en moldes de colada caliente y sistemas con válvula de cierre. Se usará como ejemplo un molde de mallas de dos cavidades utilizado para hacer piezas para la industria del riego.
En primer lugar, se preparó una plantilla para generar una CPW. El eje X corresponde al tiempo de sostenimiento y el eje Y corresponde a la presión de sostenimiento. Dicha plantilla se llama plantilla de inspección visual (VIT). Una VIT completa se muestra en la Fig. 1.
Los cuadrados rojos representan una pieza con al menos un defecto a presiones y tiempos insuficientes (hundimientos, piezas incompletas, etc.); los triángulos rojos muestran una pieza con al menos un defecto a presiones y tiempos excesivos (rebabas, piezas sobre-empacadas, etc.); y los círculos verdes representan una pieza cosméticamente aceptable.
Comenzando con una presión de sostenimiento de 27,6 bar (400 psi), las piezas se moldearon desde 27,6 bar hasta 96,6 bar (1400 psi) con incrementos de 13,8 bar (200 psi) y con tiempos de sostenimiento de 4 a 10 segundos con incrementos de 1 segundo. Los datos fueron recolectados y registrados en la VIT. A presiones y tiempos insuficientes el defecto encontrado fue hundimiento, mientras que para presión y tiempo excesivos, se encontraron rebabas en el área de la malla. Finalmente es posible graficar varias CPWs en la VIT.
Una vez que estas ventanas han sido determinadas, el siguiente paso es buscar las dimensiones de la pieza utilizando la técnica de DOE. Los parámetros de proceso varían entre los límites de las ventanas y las dimensiones que son evaluadas. Después de considerar las tres CPWs y otros requisitos de producción, se decidió escoger la Ventana 3 para establecer los límites del DOE. La matriz DOE se muestra en la tabla adjunta.
Las piezas se moldearon con las cuatro configuraciones que se indican en la tabla y se realizaron mediciones de las dimensiones. El requisito dimensional en esta parte era la longitud, que se especificó en 126.80 ± 0.07 mm. El análisis se llevó a cabo con el módulo DOE del Software Nautilus. Los resultados se muestran en las Figs. 2 a 4.
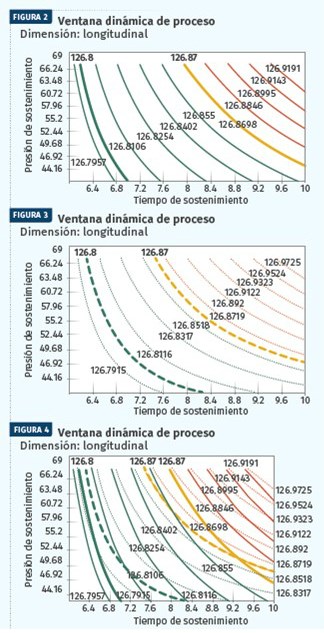
En las Figs. 2 y 3, las líneas sólidas de contorno verdes representan la cavidad uno y las líneas punteadas de contorno representan la cavidad dos. Las líneas verdes representan los ajustes donde las partes son dimensionalmente aceptables, y las líneas rojas indican los entornos donde las partes son dimensionalmente inaceptables. Las líneas naranjas son los límites de especificaciones superiores. En la Fig. 4, los dos trazados de contorno se sobreponen en un gráfico de contorno combinado. El área donde los contornos verdes para cada cavidad se cruzan representa la configuración donde ambas cavidades pueden ser moldeadas con unas dimensiones aceptables.
Las figuras 2 y 3 muestran la DPW para la cavidad uno y dos, respectivamente. Las líneas de contorno sólidas verdes representan la cavidad uno y las curvas punteadas representan la cavidad dos. Las líneas verdes representan los parámetros en los que las piezas son dimensionalmente aceptables, y las líneas rojas representan los parámetros en los que las piezas no son dimensionalmente aceptables. Las líneas de color naranja son los límites superiores de la especificación.
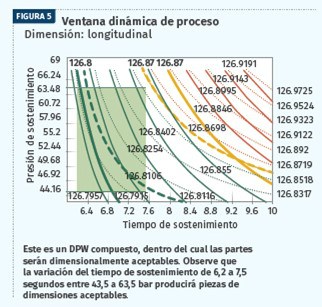
Este es un DPW compuesto, dentro del cual las partes serán dimensionalmente aceptables. Observe que la variación del tiempo de sostenimiento de 6,2 a 7,5 segundos entre 43,5 a 63,5 bar producirá piezas de dimensiones aceptables.
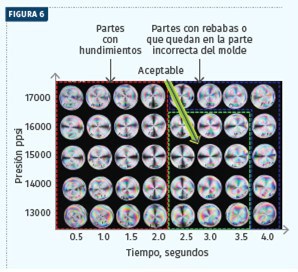
La luz polarizada bajo una cubierta óptica revela un hundimiento o rechupe en la zona del punto de inyección. Se generó un VIT usando estas fotos, seguido de un DOE.
Puesto que hay dos cavidades, los dos gráficos de contorno deben ser superpuestos para determinar un gráfico de contorno combinado como se muestra en la Fig. 4. El área donde se cruzan los contornos verdes para cada cavidad representa la configuración donde ambas cavidades pueden ser moldeadas con unas dimensiones aceptables.
Ahora se puede dibujar una DPW compuesta dentro de la cual las piezas serán dimensionalmente aceptables. Tal ventana se muestra en la Fig. 5 para los datos experimentales anteriores. Al analizar la ventana, se puede observar que variando el tiempo de sostenimiento de 6,2 a 7,5 segundos con presiones entre 43.5 y 63.5 bar, se producirán partes dimensionalmente aceptables. Naturalmente, cuanto más grande es esta ventana, el proceso va a ser más robusto.
La robustez del proceso es la meta de cada moldeador. Por esto, se recomienda que se utilice el centro de la DPW (Fig. 5) para la configuración del proceso. Una presión de sostenimiento de 55 bar y un tiempo de sostenimiento de 7 segundos fueron elegidos como los ajustes del proceso.
Al variar el tiempo de sostenimiento de 6,2 a 7,5 segundos entre 43,5 a 63,5 bar se van a obtener piezas con dimensiones aceptables. Esto es un indicador de un proceso robusto y por lo tanto se producirán piezas no sólo dentro de las especificaciones, sino también con una mejor capacidad estadística de proceso. Una vez más, aquí son posibles varias DPWs. En las máquinas de moldeo, el grado de variación de la presión es mayor que la variación del tiempo, y por lo tanto siempre se prefiere maximizar la ventana de presión.
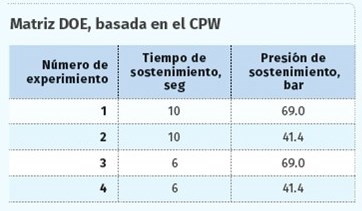
El molde anterior ha pasado por una iteración en donde se modificaron las dimensiones de las cavidades, resultando en una ventana de proceso aceptable. Durante la primera iteración, el molde no podía fabricar piezas que cumplieran con las especificaciones dimensionales. La CPW era amplia, pero la DPW era extremadamente pequeña. Considerando ambas cavidades, el proceso de moldeo no era robusto. Recuerde que moldear una pieza dentro de especificaciones no significa que todas las otras piezas estarán dentro de esas especificaciones; los moldeadores necesitan entender y medir la variación combinada en la máquina, el material, el proceso, y así sucesivamente.
Este procedimiento se aplica a los moldes de colada caliente, pero se puede extender fácilmente a los moldes con sistema de válvula de cierre. El procedimiento, de hecho, es un poco más sencillo puesto que el pasador de la válvula cierra la compuerta, eliminando la verdadera fase de sostenimiento de la discusión original de la fase de empaquetamiento y retención.
Hay otros parámetros que también deben tenerse en cuenta para el DOE. Para mantener las cosas simples, sólo fueron considerados dos factores y una dimensión. Sin embargo, ventanas dimensionales compuestas para múltiples dimensiones y cavidades deben ser consideradas.
La optimización de los tiempos y presiones de sostenimiento para moldes de colada caliente siempre ha sido un área de ensayo y error. El procedimiento descrito anteriormente es una manera científica para determinar la presión y el tiempo de sostenimiento en el caso de colada caliente y los sistemas de válvula de compuerta. Este procedimiento también evalúa y demuestra la robustez del proceso y su capacidad para moldear piezas de forma consistente.
Un interesante estudio se realizó utilizando luz polarizada en una cubierta óptica (ver Fig. 6). En este caso, el hundimiento o rechupe en el área del punto de inyección era visible bajo luz polarizada. Una VIT se generó usando estas fotos, seguido de un DOE como fue descrito anteriormente.
Contenido relacionado
Qué son los sistemas de colada caliente y cómo funcionan
Un experimentado transformador de plásticos aborda los beneficios, las mejoras y los problemas cotidianos de las coladas calientes, luego de trabajar por décadas con varias marcas en el mercado de estos sistemas.
Leer MásVamos a reconectar con innovación y tecnología en Meximold 2023
En un mundo que ha experimentado transformaciones inimaginables, en el que la virtualidad y la digitalización han sido protagonistas indiscutibles, nos entusiasma saber que los eventos presenciales son más necesarios que nunca, y qué mejor manera de reconectar que a través de un encuentro de vital importancia para la industria manufacturera: Meximold.
Leer MásCómo tratar con materiales extraños en un sistema de canal caliente
Comprender el flujo del plástico puede ayudarle a entender cómo se mueven (o no) los materiales extraños a través de su sistema de canal caliente.
Leer MásHasco inaugura centro de servicio técnico para colada caliente en México
Ante el crecimiento y dinamismo de la transformación de plásticos en México, Hasco invierte en ampliar sus capacidades de servicio al cliente para los sistemas de colada caliente en Querétaro, México.
Leer MásLea a continuación
Ventana cosmética: clave para el éxito en el moldeo por inyección
Descubra la importancia de la Ventana Cosmética de Proceso en moldeo por inyección y cómo puede garantizar piezas de calidad y un proceso eficiente.
Leer MásOptimice el proceso de moldeo por inyección con Cp y el Cpk
Aprenda a aplicar el Cp y el Cpk para mejorar el proceso de moldeo por inyección de plásticos y obtener piezas de alta calidad que cumplen con las especificaciones requeridas.
Leer MásTiempo de residencia en inyección de plástico: cálculo y factores clave
Aprenda sobre el tiempo de residencia en inyección de plástico, cómo calcularlo y los factores clave que afectan la cantidad de plástico fundido en el husillo.
Leer Más