El uso generalizado de los sistemas de canal caliente, que ha dado lugar a importantes beneficios para los moldeadores, permite una fabricación de piezas más eficiente gracias a una optimización de la máquina y a la reducción de los residuos de material. Los moldeadores pueden aumentar aún más la eficiencia de sus sistemas de canal caliente si desarrollan un enfoque estratégico para abordar los cambios de resina y, o, color.
Con un procedimiento de purga planificado, los tiempos de cambio de material serán más cortos, se puede reducir el desperdicio de material y, con el tiempo, disminuir la necesidad de mantenimiento reactivo en todo el sistema de moldeo.
Los compuestos comerciales de purga (CPC) han demostrado ser los más eficaces para eliminar el color y la contaminación de los canales calientes, pero es muy importante seleccionar la purga correcta y seguir el procedimiento adecuado con el fin de obtener el resultado deseado.
Hay una amplia gama de CPC disponibles para diferentes aplicaciones según la resina base que se va a purgar, y los aditivos, el color, los modificadores, la temperatura y las capacidades de inyección de la máquina que se va a purgar. Algunos CPC tienen cargas que pueden no fundirse completamente durante el proceso de purga y generar bloqueos en las compuertas más pequeñas y en los canales o dañar los componentes del canal caliente.
Aumentar la temperatura de la boquilla mientras se purga puede ayudar a eliminar la acumulación de material por purgar (a) cuando la boquilla del bebedero no coincide con la punta de la boquilla de la máquina (b).
Los CPC químicamente activos pueden ser una excelente opción para los cambios rápidos de color, pero no ser lo suficientemente agresivos para purgar a fondo los sistemas de inyección muy contaminados o las resinas con alto contenido de relleno. En estos casos, puede ser necesaria una formulación de purga con una mayor viscosidad para desalojar una resina con alto contenido de relleno.
Además, para purgar un sistema de canal caliente hay que tener en cuenta el tamaño del distribuidor, las compuertas y los canales de masa fundida. No existe un compuesto de purga que sirva para todo. Un proveedor de CPC es su mejor recurso para ayudarle a identificar la formulación y el procedimiento de purga correctos para sus necesidades.
Procedimiento de dos etapas
En algunos casos, un moldeador puede necesitar un ciclo de purga para solucionar problemas de moldeo derivados de la degradación de la resina en el husillo y el barril, o de otros problemas de contaminación. En estos casos, es importante pensar en el proceso de purga como un procedimiento de dos pasos, en el que primero se purga el sistema de inyección y luego el sistema de canal caliente.
Este enfoque desacoplado puede ayudar a evitar la introducción involuntaria de contaminantes en el canal caliente, una situación en la que la purga puede no ser suficiente para eliminar por completo cualquier material no deseado en el sistema. Evitar esto es fundamental para garantizar el retorno a la producción lo antes posible.
Un proceso típico de purga del canal caliente puede incluir algunos de los siguientes pasos —o todos—, aunque ciertos factores pueden requerir más o menos tiempo. Los moldeadores deben tener en cuenta que siempre es aconsejable purgar primero el sistema de inyección para eliminar cualquier contaminante en el husillo, el barril y la boquilla, con el fin de evitar su transferencia al sistema de canal caliente.
Una vez que la unidad de inyección ha sido purgada por completo, todo el sistema de moldeo, incluido el canal caliente, puede ser purgado para completar el cambio de material. En todos los casos es fundamental que se sigan cuidadosamente las instrucciones proporcionadas por el proveedor del compuesto de purga comercial.
Estas pautas deben ser tenidas en cuenta:
- El equipo de manipulación de materia prima debe limpiarse completamente.
- El sistema de refrigeración en el lado de inyección se debe apagar, pero es necesario tener precaución para no sobrecalentar el molde.
- Las temperaturas del distribuidor, las boquillas y el sistema de canal caliente deben aumentarse, teniendo cuidado de no superar las especificaciones de temperatura máxima de la resina.
- A continuación, se introduce el compuesto de purga comercial en el sistema de manipulación de materia prima, según las instrucciones del proveedor para la purga de un sistema de canal caliente.
En este punto, la tolva o el equipo de manipulación de materia prima se puede limpiar y comienza la fase de pospurga. Con solo la rotación del husillo y la contrapresión, haga pasar el material nuevo por el barril y el sistema de canal caliente durante un mínimo de 60 segundos, o comience a realizar disparos completos. Una vez sea visible un flujo limpio de material nuevo en las compuertas, o se hayan completado varios ciclos de inyección, proceda así:
- Volver a ajustar los parámetros de la máquina y del canal caliente a las condiciones de moldeo deseadas. Siga las instrucciones del proveedor, si es necesario.
- Pase el nuevo material por todo el sistema de moldeo, incluido el canal caliente, durante 60 segundos, o realice varios ciclos hasta que el material salga limpio.
- Reinicie el proceso e inspeccione las piezas hasta que se verifique el cambio de material y se cumplan todos los requisitos de control de calidad.
Una consideración importante al purgar un sistema de canal caliente es el diseño del propio molde. Dado que el flujo de polímero en un sistema de canal caliente es laminar, el tiempo para completar un ciclo de purga depende del flujo de la masa fundida y de la velocidad de cizallamiento. En general, se pueden esperar tiempos de purga más rápidos y menos ciclos de purga para los sistemas de canal caliente con diámetros de flujo más pequeños.
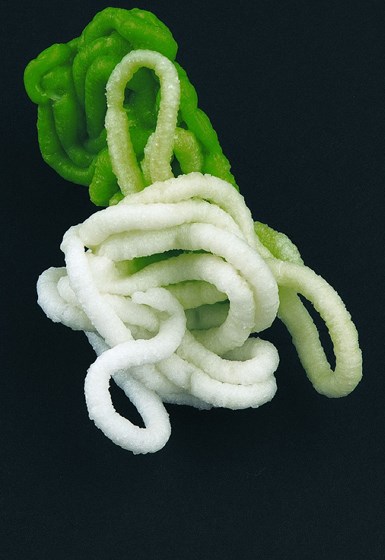
Seguir de cerca las instrucciones proporcionadas por su proveedor de compuesto de purga comercial le ayudará a acelerar el proceso de purga y a mejorar sus resultados.
Hay que tener en cuenta que los sistemas de canal caliente están optimizados para el tipo de resina que se va a moldear y no para las formulaciones comerciales de compuestos de purga. El canal caliente y todo el sistema de moldeo reaccionarán de forma diferente cuando el flujo de material del sistema cambie entre la resina y el compuesto de purga.
Una vez más, los pasos anteriores se ofrecen como guía general de los procedimientos que pueden ser necesarios para purgar con éxito una máquina de moldeo con un sistema de canal caliente. Muchas variables pueden afectar el tiempo y los pasos necesarios para realizar un ciclo de purga, incluidos el material por purgar, la temperatura de funcionamiento de la máquina, la edad, el estado del sistema de moldeo, el tamaño de la inyección, las dimensiones del husillo y barril, y las características específicas del sistema de canal caliente.
Es probable que cualquier régimen de purga deba ajustarse a una o más de estas variables. Seguir cuidadosamente las instrucciones del proveedor de CPC le ayudará a completar un ciclo de purga con la mínima cantidad de material y reducido tiempo de inactividad.
Los moldeadores que implementan un régimen de purga consistente, que incluye la formación de los operarios y la medición del rendimiento, pueden conseguir mejoras significativas en su proceso. Si se sigue un procedimiento de purga adecuado y se utiliza la fórmula de purga correcta para la aplicación, se obtienen importantes ahorros en forma de reducción de los tiempos de cambio y menos desechos o resina desperdiciada. Su proveedor de CPC y de canales calientes puede ser un valioso socio para ayudarle a establecer una estrategia de purga y formar a su personal sobre cómo purgar sus sistemas de moldeo con canales calientes de la forma más eficiente.
SOBRE LOS AUTORES:
Jim Bott es director de desarrollo de nuevos negocios para el sector automotriz en Incoe Corp. y cuenta con más de 36 años de experiencia en ventas de vehículos de motor. Contacto: 248-616-0220; jim.bott@incoe.com. incoe.com.
Robert Grzegorek es director de servicios técnicos globales de la división Dyna-Purge de Shuman Plastics, y tiene más de 30 años de experiencia en moldeo y operaciones de planta. Contacto: 317-600-9861; rgrzegorek@dynapurge.com; shuman-plastics.com.
Contenido relacionado
6 factores clave para evaluar un sistema de colada caliente
Aprenda cómo seleccionar un sistema de colada caliente que satisfaga las necesidades de fabricantes de moldes y moldeadores por inyección para mejorar la calidad y reducir costos.
Leer MásMeusburger realiza reunión de usuarios en México para su 60 aniversario
Meusburger conmemora su 60 aniversario con una reunión de usuarios en Querétaro, en la que subrayó la alta calidad de sus componentes para moldes y troqueles, la importancia de la cercanía con sus clientes y la inauguración de sus nuevas instalaciones en México.
Leer MásMeusburger fortalece lazos con la industria colombiana
La compañía fabricante de sistemas normalizados para moldes y troqueles, Meusburger, realizó una jornada enfocada en los usuarios de moldes de inyección en Medellín. Conozca los temas clave abordados y la diversidad de sectores representados en este evento de intercambio de conocimientos.
Leer MásQué son los sistemas de colada caliente y cómo funcionan
Un experimentado transformador de plásticos aborda los beneficios, las mejoras y los problemas cotidianos de las coladas calientes, luego de trabajar por décadas con varias marcas en el mercado de estos sistemas.
Leer MásLea a continuación
Add Some Science To Your Purging Practices
Applying scientific methodology to purging techniques is safer and more beneficial than operating ‘on-the-fly’ or using home-made remedies.
Leer MásFollow These Purging and Preventive Maintenance Tips for Your Screws and Barrels
Processors can extend the life of equipment and improve productivity by coupling a preventive-maintenance program for their screws and barrels with routine use of chemical purging compounds..
Leer MásTips and Techniques: Break the Taboo On Purging Hot Runners!
It’s safe to say that the concept of using a commercial purging compound (CPC) has largely been embraced by the plastics processing community.
Leer Más