El trabajo más importante de un procesador, parte 11
El trabajo de los procesadores es garantizar piezas moldeadas que contengan suficiente estabilizador para cumplir las expectativas del uso final.
Consulte otras columnas de la serie ‘El trabajo más importante de un procesador’:
El aspecto final del procesamiento diseñado para garantizar una buena retención de las propiedades mecánicas implica cuidar muy bien el paquete de aditivos. Todos los polímeros comerciales contienen un paquete de aditivos, una combinación de compuestos diseñados para proporcionar la estabilidad necesaria para permitir que ocurra el proceso de fusión sin degradar el polímero. Las resinas también pueden contener aditivos para mejorar el rendimiento final.
Los componentes en el paquete de aditivos pueden variar de compuesto a compuesto y pueden incluir estabilizadores UV, agentes de nucleación, agentes antiestáticos, agentes antimicrobianos, colorantes y retardantes a la llama. Pero es probable que incluyan al menos cierto nivel de lubricación y un cierto grado de estabilización contra la degradación térmica y oxidativa. Este es el conjunto de estabilizadores que más nos interesa para los propósitos de esta discusión.
Los antioxidantes, como se les conoce generalmente, se incorporan a un material con dos propósitos: permitir que el material sobreviva a las altas temperaturas y a los esfuerzos de cizalla del proceso de moldeo; y para proporcionar la estabilidad que puede ser necesaria para que la pieza pueda cumplir con sus requisitos de aplicación. Estas funciones se delegan a menudo a dos grupos diferentes de productos químicos, clasificados como antioxidantes primarios y secundarios. La química de estos materiales es fascinante y compleja. Pero cuando todo está dicho y hecho, el propósito de estas sustancias es proteger el polímero de la degradación que pueda ocurrir durante el procesamiento y el uso. Las cantidades exactas de estos aditivos dependerán del polímero que va a ser estabilizado y de las aplicaciones a las que está destinado el material. El polipropileno y el polietileno son buenos ejemplos de materiales que requieren protección contra la oxidación.
En general, el PE es más resistente a la oxidación que el PP y, por lo tanto, requiere cargas más bajas de aditivos. Pero todos los materiales comerciales de PE y PP exigen un nivel mínimo para superar el proceso de fusión.
Si después de que la pieza es moldeada se espera que la pieza soporte temperaturas elevadas, durante su aplicación, se necesitará un mayor nivel de estabilización para asegurar que el producto no falle. Para el PP, estos tipos de aplicaciones de alta temperatura pueden ser desde componentes de una cafetera a tanques para depositar el refrigerante de motor de un automóvil.
El proveedor del material va a incorporar una cierta cantidad del paquete de estabilización en el material, haciendo de este el punto de partida para ese material. Ahora, es trabajo del procesador manejar el material durante el proceso para que la pieza moldeada contenga suficiente estabilizador y cumpla con las expectativas del usuario final. El proceso de moldeo siempre consumirá cierta cantidad del antioxidante en el material. Eso es lo que se espera. Pero la cantidad de estabilizador que se consume dependerá de las condiciones del proceso, más notablemente de la temperatura de fusión y del tiempo que el material permanezca en estado fundido. Las bajas temperaturas de fusión y los tiempos de residencia más cortos producen piezas que retienen un mayor nivel de estabilización, y estas piezas serán más capaces de manejar el entorno de aplicación. Si las temperaturas de fusión son elevadas o se alargan los tiempos de residencia, la pieza moldeada será menos capaz de gestionar las demandas de aplicación.
En el laboratorio podemos medir la estabilidad de un material contra la oxidación. Utilizando una técnica analítica conocida como calorimetría de barrido diferencial (DSC), podemos exponer una muestra de material a una temperatura elevada constante en presencia de oxígeno y determinar el tiempo que tarda el material en sufrir oxidación.
La medida se conoce como tiempo de inducción de oxidación (OIT) y esta técnica primero fue utilizada para ayudar a los científicos de polímeros a comprender el fracaso prematuro en el aislamiento de cables en la década del sesenta. El gráfico adjunto muestra el resultado de esta prueba. El cambio brusco en la pendiente de la gráfica se asocia con el inicio de la oxidación. Esta materia prima puede soportar 77 minutos de exposición a estas condiciones antes de que se consuma el paquete de antioxidantes y el material falle rápidamente.
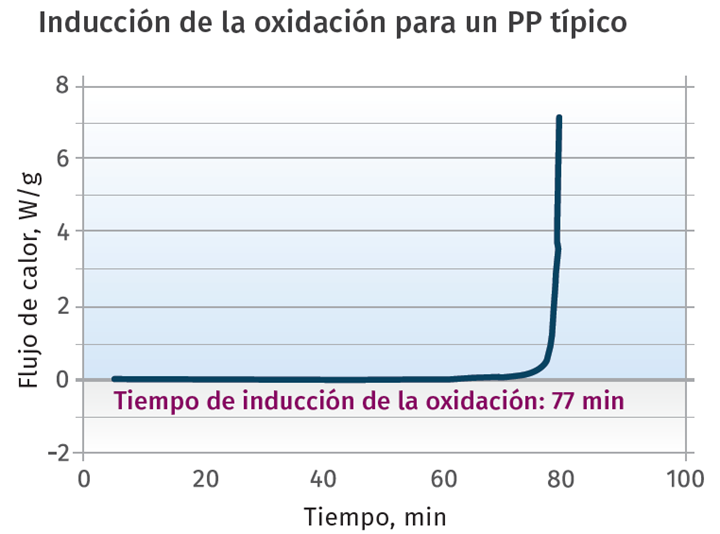
Con la DSC, una muestra de material puede ser expuesta a una temperatura elevada constante en presencia de oxígeno y determinar el tiempo que tarda el material en sufrir oxidación. Esto muestra un resultado de esta prueba. El cambio brusco en la pendiente de la gráfica se asocia con el inicio de la oxidación. Esta materia prima puede soportar 77 minutos de exposición a estas condiciones antes de que se consuma el paquete de antioxidantes y que el material falle rápidamente.
Si esta prueba se ejecuta en las piezas moldeadas de este material, el resultado puede utilizarse para determinar cómo el proceso influyó en la estabilidad del material a largo plazo. En la práctica, hemos observado piezas moldeadas que retienen el 75% de la OIT de la materia prima, y hemos visto piezas que conservan como mucho el 10% de este valor de referencia. La diferencia entre estos dos resultados se relaciona con la historia térmica del proceso. Y la vida útil de la pieza en el campo se regirá en gran medida por el nivel de estabilidad oxidativa que la pieza tiene cuando se va a utilizar.
Esto tiene implicaciones en el uso de retriturados. Es de esperarse que el retriturado exhiba cierto grado de agotamiento en el paquete de antioxidantes. El grado en que esto ocurra dependerá de las condiciones de proceso. A menudo me preguntan cuánto triturado debe ser utilizado o cuántas veces puede someterse un material al proceso de fusión. La respuesta es que depende de los esfuerzos térmicos a los que el material fue expuesto al pasar previamente por el proceso de moldeado. Este agotamiento puede también ocurrir cuando la pieza está en uso.
Recientemente, revisé un análisis de un material que tenía una OIT de 140 min en forma de pellets. Las piezas moldeadas retuvieron una OIT de 100 min, y las piezas que habían sido expuestas a una rutina prolongada de temperaturas elevadas, de 60-70 minutos.
A medida que avanzamos en la dirección de usar más material reciclado postconsumo, es cada vez más importante que tengamos en cuenta el ciclo de vida del producto inicial, así como los tipos de productos que se planean hacer con el material reciclado. Puede ser necesario reconstituir los estabilizadores al producir la materia prima regenerada.
Nos ha tomado tiempo revisar todos los aspectos del proceso relacionados con el mantenimiento de la integridad del polímero. Todos estos son factores que no son parte de la mayoría de los planes de calidad asociados con el moldeo de piezas. Los procesadores se centran típicamente en la producción de piezas en el tiempo de ciclo que les permita lograr un beneficio. El peso molecular, la estructura de polímero, el nivel de esfuerzo interno y la integridad de los refuerzos y aditivos rara vez son considerados como parte del trabajo.
Muchos procesadores pueden no ser siquiera conscientes de su papel en el logro de los óptimos resultados en estas áreas. Hay algunas interesantes estrategias comunes para hacerlo. Por ejemplo, el peso molecular y la retención de aditivos se optimizan mediante el procesamiento de materiales en el extremo inferior de la gama de temperaturas de fusión. Maximizar la cristalinidad y minimizar los esfuerzos en el molde se obtienen mediante el procesamiento con temperaturas altas del molde. Una vez que el procesador llega a ser consciente de su papel en estos asuntos, puede usar este conocimiento para informar sus estrategias de desarrollo del proceso. El mundo de los productos de plástico será un lugar mejor al haber pasado por este proceso de aprendizaje.
Acerca del autor
Michael Sepe
Consultor independiente sobre materiales y procesamiento, a nivel global, cuya compañía, Michael P. Sepe, LLC, tiene su sede en Sedona, Arizona. Tiene más de 40 años de experiencia en la industria del plástico y asesora sus clientes en selección de materiales, diseño para manufactura, optimización de procesos, solución de problemas y análisis de fallos. Contacto: (928) 203-0408 • mike@thematerialanalyst.com
Contenido relacionado
Entendiendo el recocido y el entrecruzamiento en polímeros
Descubra la ciencia detrás del recocido en termoplásticos y el entrecruzamiento en termoestables. Aprenda sobre la Tg y su impacto en la polimerización.
Leer MásANIPAC ofreció análisis actualizado del mercado de materias primas
Conozca las conclusiones clave del 10° Foro de Materias Primas organizado por la ANIPAC y cuál es el panorama del mercado de resinas, producción y transformación del plástico en México.
Leer MásPlásticos en la industria automotriz: aspectos clave de sustentabilidad
¿Sabía de la consideración de los materiales bioplásticos en el sector automotriz? ¿Conoce el potencial de reciclabilidad de los plásticos de componentes automotrices?
Leer MásFundamentos de la medición del color en plásticos
Conozca la importancia de la medición del color en la industria del plástico y una visión general de los instrumentos y tecnologías involucradas.
Leer MásLea a continuación
Control de procesos: retención de la longitud de fibra
Aprenda cómo la optimización de la longitud de fibra mejora las propiedades mecánicas de los materiales compuestos y las estrategias efectivas para su conservación
Leer MásControl de procesos: rendimiento de la pieza moldeada
La temperatura del molde y las estrategias de llenado influyen en la calidad de las piezas poliméricas. Aprenda técnicas para reducir el esfuerzo interno y optimizar la uniformidad de la presión.
Leer MásControl de procesos: cómo reducir esfuerzos en moldes de inyección
Conozca cómo ajustar la temperatura y enfriamiento en moldes de inyección para minimizar deformaciones y mejorar la calidad de piezas.
Leer Más