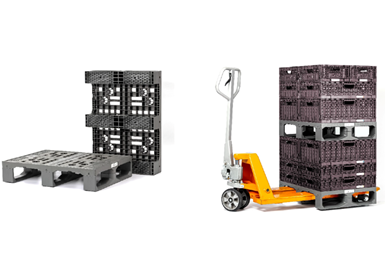
Productos que se fabrican con las tecnologías de las empresas del Grupo Haidlmair.
Crédito: Walther Faltsysteme
Productividad y eficiencia están entre las metas más importantes para que todas las empresas de fabricación tengan éxito y satisfagan a sus clientes. Esto es especialmente cierto en la industria del plástico, donde los plazos de producción cortos, los enfoques innovadores y los métodos de producción eficientes son especialmente importantes, debido a los volúmenes y niveles de calidad exigidos.
Por esta razón, el moldeador alemán Walther Faltsysteme optimiza constantemente estos factores. La tradicional empresa familiar es una de las pocas compañías de su sector que cuenta con su propio taller de moldes, utilizado principalmente para proyectos de desarrollo y la fabricación de moldes prototipo. Además, Walther lleva varios años confiando en la calidad de los moldes de inyección de Haidlmair, especialmente cuando se trata de moldes de alto rendimiento.
“Tenemos muchos moldes en uso, por supuesto no todos los pedimos a Haidlmair, pero si el tiempo de ciclo es un factor importante y decisivo o cuando nuestros clientes tienen un plazo de entrega corto, dirigimos nuestra mirada hacia ellos”, explica Dominik Lemken, director de proyectos y jefe de compras de Walther Faltsysteme.
Desde la primavera de 2020, Walther cuenta con dos moldes nuevos que, por primera vez, combinan el know-how de Haidlmair con dos tecnologías que provienen del departamento de desarrollo de la empresa familiar. La primera es el innovador sistema de canal caliente “Flat Die Unit” de la filial de Haidlmair, FDU Hotrunner GmbH, y la solución de digitalización Mould Monitoring de Digital Moulds GmbH (una empresa conjunta al 50 % entre Haidlmair y la empresa bávara de fabricación de moldes Siegfried Hofmann GmbH).
Los dos moldes, en los cuales ambos sistemas se encuentran instalados, se usan para producir estibas o pallets. El primer molde produce los tres largueros mientras que el segundo la cubierta. La razón de esta división se debe a los diferentes materiales utilizados para producir la estiba. En el caso de los largueros, se añade fibra de vidrio al plástico para conseguir un diseño más resistente al desgaste y a la flexión, mientras que para la cubierta se utiliza material reciclado.
Estos dos factores plantean varios retos a los productores. En el caso de los largueros, la fibra de vidrio debe estar distribuida uniformemente en el producto. Aquí entran en juego algunas de las ventajas del FDU. Este sistema favorece la distribución uniforme del material y aumenta así la calidad y durabilidad de los largueros.
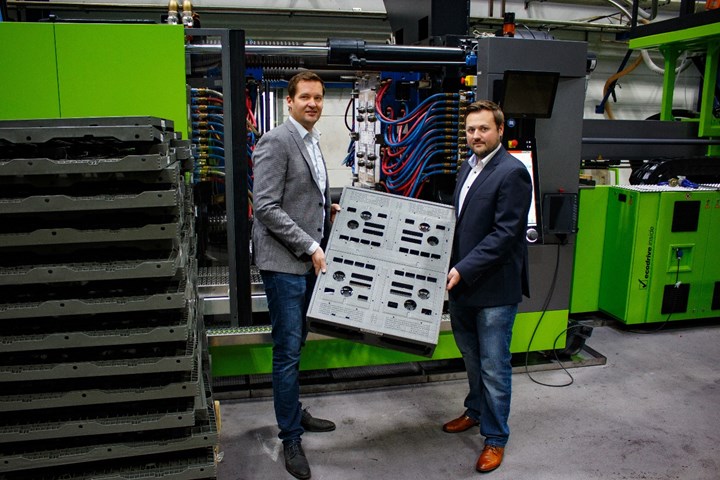
Dominik Lemken con el director del proyecto, Florian Herkenrath, y una estiba o pallet.
Crédito: Walther Faltsysteme.
En el pasado, el material reciclado generaba muchos problemas en el proceso. La fricción en el molde, especialmente en las proximidades de los puntos de inyección, provocaba picos locales de temperatura, degradación y, como resultado, la adherencia del material. Ahora, Walther soluciona este problema con el uso del sistema FDU, ya que la boquilla de ranura introduce el material en el molde con más suavidad. Además, la proporción entre materias primas nuevas y material reciclado se puede desplazar a favor del material reciclado, para poder fabricar el producto de forma aún más sostenible.
Enfoque en el rendimiento
Los dos moldes funcionan actualmente de forma sincronizada uno al lado del otro en dos máquinas de Walther. En el medio, un robot de brazo articulado ensambla las piezas para formar la estiba. Por supuesto, también se trata del rendimiento de los dos moldes. Hace cuatro años, Walther encargó este juego de moldes a Haidlmair. Desde entonces, estos moldes, equipados con boquillas redondas convencionales, han funcionado sin problemas y con un rendimiento excelente.
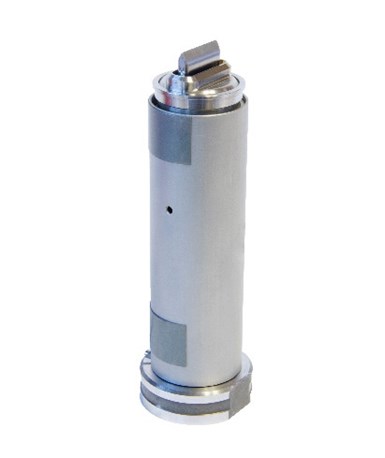
A finales del 2019, Walther decidió ampliar su capacidad con otra línea de producción. Los especialistas del fabricante examinaron muy de cerca el molde y trataron de optimizar el rendimiento en cuanto a la construcción del molde y mediante pequeños cambios en el producto. Pero después de todo el análisis, se encontró un cuello de botella con las compuertas. Hay que inyectar aproximadamente 6,5 kg de material por estiba lo más rápido posible. Con las boquillas de válvula de aguja convencionales se llega rápidamente al límite.
El sistema FDU, con su sección transversal significativamente mayor (en este caso un Midi FDU con un ancho de cuchilla de 22 mm), permite al usuario introducir una mayor cantidad de material en el molde en poco tiempo y amplía los límites de capacidad de inyección anteriores, entregando un mayor rendimiento. En el caso concreto de Walther, el tiempo de ciclo pudo reducirse en aproximadamente un 10 %.
Dominik Lemken está muy satisfecho con el rendimiento obtenido hasta ahora: “Ya hemos producido más de 100.000 unidades desde abril sin ningún problema digno de mención y me alegraría que pudiéramos utilizar el sistema FDU en otros moldes, por ejemplo, aplicarlo al proceso de producción de placas de rodillos o de diversas cajas plegables. La mejora en el rendimiento y la ventana de proceso ampliada so un claro argumento para hacerlo”.
Moldes digitales para la confiabilidad en la producción
Los requisitos de la segunda tecnología utilizada por Walther Faltsysteme (otra empresa del Grupo Haidlmair) eran completamente diferentes. El Mould Monitoring suministrado por la innovadora empresa Digital Moulds se centra menos en el rendimiento del molde y más en la verificabilidad de los procesos de producción, además del uso de la información obtenida, por ejemplo, para optimizar el consumo del material y poder ajustar el plan de producción en consecuencia.
La monitorización de moldes permite registrar los datos de producción y localización mediante un hardware que se monta directamente en el molde de inyección. Los datos se determinan mediante sensores internos y externos, se procesan previamente en el dispositivo y se transfieren a un sistema basado en la nube a través de la red celular. Esto significa que la producción se puede comprobar en tiempo real, incluso si no se está en el lugar. Además, los datos proporcionan información más precisa sobre el estado del molde y permiten identificar rápidamente desviaciones en los parámetros especificados, disminuyendo los problemas y pérdidas de producción.
En Walther, los mismos puntos fueron decisivos para utilizar el sistema. Además, vieron la necesidad en sus clientes por este tipo de información, especialmente en el negocio de proyectos. Hay que hacer declaraciones ad hoc sobre el estado actual de la producción y responder a las preguntas del cliente, lo que mejora enormemente la relación con ellos, aumenta adicionalmente la transparencia en el proceso y aumenta la confianza en la relación cliente-proveedor. En Walther, cinco moldes están ahora equipados con este sistema.
“Los moldes que están equipados con Mould Monitoring entregan información importante para nosotros como la cantidad de producción, los ciclos completados, la identificación de fallos, así como datos para planear un mejor mantenimiento a corto plazo (que puede reducir la producción diaria) y otros datos básicos. Principalmente ayuda a la gestión de proyectos, servicio al cliente y al departamento de compras", afirma Dominik Lemken como resumen de los principales ámbitos de aplicación del sistema.
Digital Moulds fue capaz de satisfacer plenamente todos los requisitos de Walther. En la práctica, los ejemplos positivos y preventivos de Mould Monitoring en la confiabilidad de la producción ya eran evidentes. Durante un lote de producción, un molde tuvo un aumento gradual del tiempo de ciclo y pudo reconocerse inmediatamente con el Mould Monitoring. Este aumento del tiempo de ciclo condujo gradualmente a una reducción del volumen de producción.
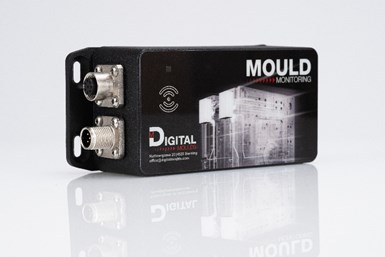
La caja de control para supervisión de moldes se monta directamente en el molde y es el corazón del sistema de control.
Crédito: Digital Moulds GmbH.
El sistema hizo sonar la alarma de inmediato y, al analizar los datos de Mould Monitoring, los especialistas de Walther pudieron reconocer con relativa rapidez que tenía que haber un problema con la refrigeración, que a su vez prolongaba el tiempo de refrigeración. La calidad de la pieza producida se seguía entregando, pero los valores reales de la duración del ciclo ya no coincidían con la planificación original de la producción, lo que habría provocado problemas. Gracias a la oportuna alarma de Mould Monitoring y a los datos que puso a disposición, los especialistas de Walther pudieron identificar el problema de forma rápida y clara. La solución consistió simplemente en desbloquear un orificio de refrigeración que permitió regresar al tiempo de ciclo especificado.
Sin embargo, en Walther se da con más frecuencia el caso contrario: “Si se producen problemas o averías en los moldes sin Mould Monitoring, tendremos paradas de producción hasta de varios días porque el problema no se reconoce a tiempo o no se reconoce durante mucho tiempo. Nuestros colegas ya afirman que esto no habría ocurrido con Mould Monitoring”, dice Lemken describiendo un replanteamiento en la empresa.
En cualquier caso, Walther tiene previsto aumentar el uso del FDU y Mould Monitoring en el futuro, porque la conclusión es que vale la pena, especialmente en producciones en las que son esenciales las cantidades elevadas y la disponibilidad estable.
Contenido relacionado
Hasco inaugura centro de servicio técnico para colada caliente en México
Ante el crecimiento y dinamismo de la transformación de plásticos en México, Hasco invierte en ampliar sus capacidades de servicio al cliente para los sistemas de colada caliente en Querétaro, México.
Leer MásVamos a reconectar con innovación y tecnología en Meximold 2023
En un mundo que ha experimentado transformaciones inimaginables, en el que la virtualidad y la digitalización han sido protagonistas indiscutibles, nos entusiasma saber que los eventos presenciales son más necesarios que nunca, y qué mejor manera de reconectar que a través de un encuentro de vital importancia para la industria manufacturera: Meximold.
Leer MásQué son los sistemas de colada caliente y cómo funcionan
Un experimentado transformador de plásticos aborda los beneficios, las mejoras y los problemas cotidianos de las coladas calientes, luego de trabajar por décadas con varias marcas en el mercado de estos sistemas.
Leer MásMeusburger fortalece lazos con la industria colombiana
La compañía fabricante de sistemas normalizados para moldes y troqueles, Meusburger, realizó una jornada enfocada en los usuarios de moldes de inyección en Medellín. Conozca los temas clave abordados y la diversidad de sectores representados en este evento de intercambio de conocimientos.
Leer MásLea a continuación
Fabricante de moldes Haidlmair le apuesta a la sostenibilidad
Con el fin de hacer un aporte al medio ambiente, la compañía ha emprendido una serie de iniciativas para hacer ahorros significativos de CO2 en el proceso de producción de sus moldes.
Leer MásCOVID-19: Engel y Haidlmair desarrollan protectores de boca y nariz en tiempo récord
Engel ofrece máquinas de moldeo por inyección específicamente adaptadas al concepto de molde creado por Haidlmair.
Leer MásEl molde, como cerebro del proceso, es la visión de Haidlmair
Desde el monitoreo digital de moldes hasta la integración de tomografía computarizada e impresión 3D en sus procesos, el fabricante austriaco de moldes Haidlmair es un referente mundial. Haber visitado su planta, en Nußbach, fue como mirar por una ventana hacia el futuro y ver cuáles serán los estándares en la producción de moldes y herramentales.
Leer Más