En la actualidad, los retos que afronta la industria del reciclado son enormes y desafiantes, por lo cual es necesario el desarrollo de nuevas tecnologías para solucionarlos. Entre estos retos destaca la reutilización de llantas fuera de uso, ya que se han alcanzado niveles alarmantes, que sobrepasan los 17 millones de toneladas generadas por año. Debido a su estructura entrecruzada altamente estable, su proceso de descomposición es lento y se lleva a cabo en varios cientos de años.
Soluciones posibles: polvo de llanta en polímeros
Una posible solución para disminuir esta problemática radica en convertir las llantas trituradas en polvo, con la posibilidad de utilizarlo como fase elastomérica en diferentes polímeros. Sin embargo, el alto grado de reticulación del polvo de llanta tiene un efecto negativo sobre las propiedades finales de los materiales compuestos obtenidos, debido a las malas interacciones interfaciales entre el polímero y las partículas de caucho. Entre las posibles soluciones a esta problemática aparecen los procesos adecuados de extrusión y de espumado.
Desarrollo en el CIQA: obtención de espumas de EVA con polvo de llanta
Actualmente, en el Centro de Investigación en Química Aplicada (CIQA) en el grupo de trabajo LANIAUTO (Laboratorio Nacional en Innovación y Desarrollo de Materiales Ligeros para la Industria Automotriz) se avanza en el proceso de obtención de espumas de EVA hasta con 40 % de polvo de llanta, que se realiza en tres pasos principales:
- En primer lugar se extruye un concentrado de aditivos en el que se mezclan los agentes espumantes, entrecruzantes y activadores con el polímero EVA.
- En segundo lugar se procesa un concentrado de polvo de llanta en la que se mezcla 80 % de este material con 20 % de EVA.
- Por último, se diluyen los concentrados obtenidos en el polímero para obtener las proporciones finales deseadas.
Selección de elementos para la extrusión de EVA-polvo de llanta
Debido a que los componentes de la formulación se encuentran en forma de polvo, es importante seleccionar de manera adecuada los elementos necesarios para proveer la mejor configuración de los husillos, que promuevan una adecuada dispersión y homogenización de los componentes presentes en la formulación, en especial, para evitar la activación del agente entrecruzante que promueva el espumado del compuesto dentro del barril.
En este sentido se seleccionaron diversos elementos principales que cumplen esta función, como lo muestra la Fig. 1, y de los cuales se proporcionan más detalles a continuación:
Inicialmente se transportan los ingredientes hacia la zona de fusión, donde se suavizan los ingredientes fusibles; debido a la adecuada secuencia y tipo de elementos (RFV y RSE) se lleva a cabo la fusión de los ingredientes sin generar excesiva fricción y presión, lo cual minimiza o evita que el agente entrecruzante sea activado en esta zona. Los elementos RFV promueven una alimentación mejorada, tipo pala, diseño y patente de STEER, una evolución de los elementos SK del sistema Werner & Pfleiderer.
Por otro lado, los elementos LKB (Left Kneading Block) en combinación con los otros elementos de mezclado normales en la zona de fusión, y al no tener como “cierre” de esta zona un elemento de flujo inverso de transporte generador de fricción y presión, se inserta en la configuración un elemento de flujo inverso de mezclado con poco efecto de mezclado dispersivo y más efectos de transporte y distribución, lo cual también ayuda a minimizar la activación del agente entrecruzante.
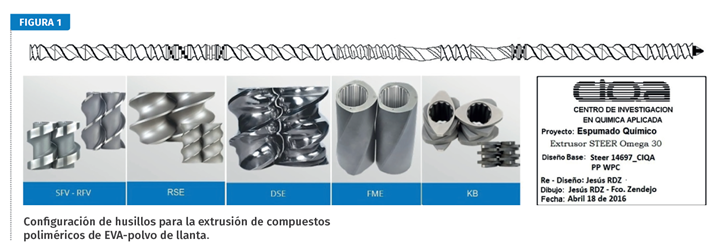
Figura 1. Configuración de husillos para la extrusión de compuestos poliméricos de EVA-polvo de llanta.
Los elementos de agitación dinámica DSE, por sus siglas en inglés (Dynamic Stirring Element), gracias a su diseño empatan el mezclado con el transporte, previendo la generación de calor y esfuerzos de corte excesivos, que por lo general sucede cuando una resina con carga entra en contacto con elementos de mezclado convencional.
La posición y diseño de los elementos fraccionales FME (Fractional Mixing Element) evitan los picos de esfuerzo y presión e imparten a la vez un alto grado de mezclado elongacional en un espacio confinado. Los materiales procesados a través de los elementos FME obtienen un uniforme y muy efectivo suministro de energía, de manera que no se necesita extender las zonas de mezclado para asegurar que los materiales han sido expuestos a la energía de mezclado adecuada.
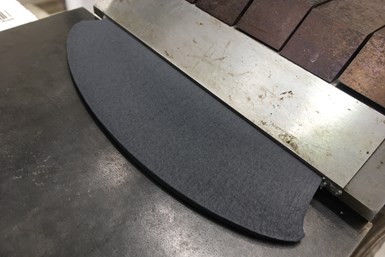
Figura 2. Placas extruidas de EVA-polvo de llanta.
Resultados y aplicaciones potenciales
Por todo esto, la combinación adecuada de los elementos provee un mezclado distributivo y elongacional aunado a un mejor control de la temperatura del fundido, que permite el extruido de este tipo de compuestos en continuo (Fig. 2), con una distribución homogénea y óptima de los ingredientes sin activar el agente entrecruzante, para lograr que se active eficientemente en el proceso de espumado del compuesto (Fig. 3).
Aún falta gran trabajo por realizar, sobre todo en el mejoramiento de la calidad de los productos finales a través del proceso de espumado; sin embargo, los resultados de los prototipos obtenidos hasta el momento son alentadores y tienen un gran potencial para aplicarse como tapetes antifatiga.
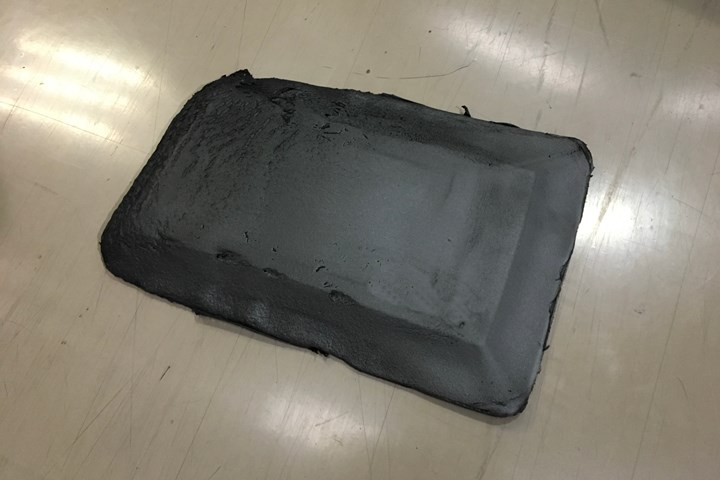
Figura 3. Prototipo de tapete antifatiga espumado con EVA y polvo de llanta (70/30).
Sobre los autores
Ing. Jesús Gilberto Rodríguez Velázquez
Técnico laboratorista químico, diplomado en Polímeros e ingeniero en Sistemas Computacionales, con experiencia de treinta años en el ámbito de la elaboración de mezclas, concentrados y compuestos de matriz polimérica principalmente, en proyectos de investigación y desarrollo de nuevos materiales. Actualmente trabaja en el Departamento de Procesos de Transformación del CIQA como técnico titular C.
Contacto: jesus.rodriguez@ciqa.edu.mx
Dr. José Francisco Hernández Gámez
Ingeniero en Materiales, con maestría y doctorado en el mismo ramo, tiene experiencia en el área de investigación y desarrollo en temas de procesamiento y reciclaje de plásticos. Se incorporó al Centro de Investigación en Química Aplicada en el año 2015 y actualmente se desempeña como investigador titular A, adscrito al Departamento de Procesos de Transformación de Plásticos.
Contacto: jose.hernandez@ciqa.edu.mx
Contenido relacionado
ANIPAC lanza Directorio de Empresas Recicladoras 2023
ANIPAC presenta este directorio virtual que proporciona información detallada y datos de contacto de más de 40 empresas dedicadas al reciclaje de plásticos.
Leer MásSíntesis y polimerización del PET: métodos y factores
Explore los diferentes métodos y factores en la producción de PET, desde la síntesis del monómero hasta la policondensación en estado sólido.
Leer Más¿Qué es y cómo funciona el reciclaje mecánico de plásticos?
El reciclaje mecánico de plásticos es un proceso clave para enfrentar desafíos ambientales y económicos. Este enfoque sostenible y eficiente disminuye la contaminación y promueve una economía circular al reutilizar materiales como el polipropileno, el polietileno y el PET.
Leer MásClaves sobre poliestireno expandido (EPS): fabricación, usos y reciclaje
El poliestireno expandido (EPS), unicel o espuma de poliestireno es un material versátil con una amplia gama de aplicaciones que se destaca por su ligereza y capacidad de aislamiento. Conozca su historia, proceso de fabricación, propiedades, usos y avances en reciclaje.
Leer MásLea a continuación
Reciclaje y producción sustentable de llantas: la apuesta de Lanxess
Con agentes desmoldeantes sin silicona y soluciones para el reciclaje de neumáticos mediante devulcanización, Lanxess impulsa la producción sostenible de llantas.
Leer MásCambio de paradigma en la inyección de cubetas
StackTeck y Avance Industrial unieron su conocimiento técnico en moldeo por inyección para romper paradigmas en la fabricación de cubetas. Así, demostraron una poderosa combinación de tecnologías de molde, máquina y enfriamiento que les permitió llegar a un ciclo de producción de tan solo 13 segundos para cubetas estándar.
Leer Más¿Por qué se necesitan reglas globales para el uso de polímeros?
La legislación de la ONU tiene el potencial de reducir la contaminación por plásticos a escala mundial a través de un lenguaje firme y claro y de objetivos jurídicamente vinculantes.
Leer Más