Cálculos de escalamientos simples para fusión
Puede evitar complicadas ecuaciones de fusión al diseñar o evaluar un husillo mediante el uso de métodos más simples que ahorran tiempo y ofrecen buenos resultados.
El escalamiento (o disminución) de husillos simples para la salida implica algo más que aumentar la sección de dosificación. Cada sección del husillo debe ser considerada individualmente y luego debe equilibrarse con las otras secciones. Agregar longitud a una sección afecta a las otras, por ejemplo. La sección de dosificación/bombeo se puede analizar bastante bien mediante las ecuaciones de flujo principal/presión de flujo, como se indicó en la columna en la edición de enero.
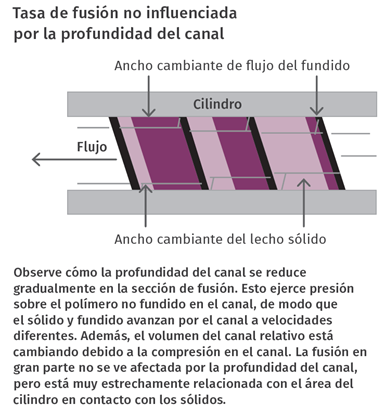
Aunque ocurre alguna fusión en todas las secciones del husillo, la gran mayoría sucede en la sección de compresión o en el diámetro de raíz cónica, que se conoce como sección de fusión. Para muchos es sorprendente que el efecto del calor conducido del cilindro tiene un efecto relativamente pequeño en la fusión, excepto a velocidades de husillo muy bajas, en comparación con la causada por disipación viscosa o por cizallamiento. Una vez que se forme una película fundida en la pared del cilindro, la temperatura en la película aumenta rápidamente, por lo que hay poca diferencia de temperatura para transferir el calor del cilindro al polímero. Además, el polímero mismo es un excelente aislante, que resiste la transferencia de calor al polímero no fundido debajo del fundido formado en la pared del cilindro.
El acero, por ejemplo, es 130 veces más conductivo que el LDPE. Con la misma geometría de husillo, polímero y velocidad periférica del husillo, la tasa de fusión es en gran medida proporcional al área del polímero no fundido, o lecho sólido, que está en contacto con el cilindro para fundir por disipación viscosa o por cizallamiento.
Determinar la tasa de fusión de un husillo con filetes convencionales para que se pueda determinar la longitud de fusión y el ángulo de conicidad requiere un análisis muy complejo y largo. Puede utilizarse un enfoque más sencillo para muchos requisitos de escalamiento. Se ha encontrado que este enfoque da buenos resultados cuando se aumenta el tamaño de un husillo existente con un rendimiento satisfactorio a otro tamaño.
En su libro Engineering Principles of Plasticating Extrusion, Zhev Tadmor y Imrich Klein mostraron que la tasa promedio de fusión en un canal cónico es:
ω = (ΦW0.5)/(2-(A/ψ))
Traduciendo esta ecuación en palabras: la tasa de fusión por la distancia de canal descendente en un canal cónico es la tasa de fusión multiplicada por la raíz cuadrada del ancho del lecho sólido, dividido por la cantidad de dos, menos la tasa de conicidad, dividida por la tasa de fusión de la unidad por la tasa de flujo de masa por la profundidad del canal de la unidad. A pesar de esa complejidad, todos los datos a rellenar para Φ, A y ψ en esta ecuación están disponibles o se calculan fácilmente, excepto "W", que es el ancho de los sólidos en el canal que están en contacto con el cilindro. Determinar el ancho de los sólidos en contacto con el cilindro en cualquier ubicación es un análisis particularmente difícil y es principalmente una cuestión de estimados o de análisis de los datos de presión precisos en distintos puntos a lo largo de la sección de fusión.
Como se muestra en la imagen, la profundidad del canal se reduce gradualmente en la sección de fusión, ejerciendo presión sobre el polímero fundido y no fundido en el canal. Como resultado, el sólido y el fundido generalmente no avanzan por el canal a la misma velocidad. Además, el volumen relativo del canal está cambiando debido a la compresión en el canal. La tasa de fusión en gran parte no se ve afectada por la profundidad del canal, pero está muy estrechamente vinculada con el área del cilindro en contacto con los sólidos. En consecuencia, la tasa de fusión no está directamente relacionada con la tasa de flujo o la salida.
Se puede utilizar un enfoque simplificado para determinar el área de contacto sólido, que realmente no calcula la tasa de fusión, sino que solo compara el rendimiento de fusión de un husillo a otro. Por supuesto, esto se aplica solo si se procesa el mismo polímero. Si el primer husillo funciona satisfactoriamente con las adecuadas temperaturas de fusión, estabilidad, calidad del fundido y tiempo de uso del husillo, entonces se puede usar un segundo tamaño de husillo con buenos resultados. Debe respetarse, por supuesto, la misma geometría del husillo general para que funcione satisfactoriamente. También es recomendable limitar el aumento a un diámetro tan pequeño como sea posible.
La relación de los diámetros al cuadrado con las mismas profundidades de canal describe el cambio en la salida en la sección de dosificación (D2/D1)2 para dos tamaños diferentes de husillos con las mismas profundidades de canal y geometría. Sin embargo, para mantener una calidad de fusión y temperatura de fusión similares, la relación de profundidad del canal debe aumentarse en una segunda relación.
Normalmente he utilizado con buenos resultados (D2/D1)0.7 como un factor de escala general, como se señaló en un artículo anterior. Puesto que el área del canal es naturalmente la relación del cuadrado de los diámetros cuando se cambia el tamaño del husillo, si el campo del filete y el ancho del filete se mantienen proporcionales, el aumento en la longitud requerida de fusión llega a ser, en gran medida, proporcional al aumento en la profundidad de la sección de dosificación o (D2/D1)0.7. Esto significa que el aumento de la salida debe ser aproximadamente proporcional al aumento en la zona de fusión o [(D2/D1)2 x (D2/D1)0.7]. Esto se puede medir en longitud helicoidal o simplemente multiplicando el número de filetes en el mismo ángulo de hélice. Por ejemplo, al aumentar de un husillo de 4.5-pulgadas a uno de 6 pulgadas, la nueva longitud de fusión puede aproximarse así:
(6.0/4.5)0.7 = 1.223 × el número de filetes anterior.
Para husillos de barrera, es sencilla la determinación de "W" (ancho de lecho sólido). Se espera que el canal principal permanezca esencialmente lleno de sólidos, y el fundido se arrastre a medida que se forma a través de la barrera hacia el canal de fusión (suponiendo que el primer husillo está bien diseñado). Esto elimina en gran parte el complejo cálculo del ancho variable del lecho sólido y del ángulo cónico apropiado o la velocidad de compresión para la sección de fusión y permite aumentar de manera más precisa los husillos de barrera con cálculos de fusión simplificados.
Aunque ciertamente no es un análisis riguroso, estas aproximaciones han funcionado bien a través de cientos de ampliaciones (y disminuciones) del husillo una vez que se encuentra un buen diseño con buenos resultados, lo que ahorra mucho tiempo. Incluso si no diseña un nuevo husillo, sino que solo evalúan varios husillos diferentes, es un punto de referencia útil.
Acerca del autor
Jim Frankland
Jim Frankland es un ingeniero mecánico que ha estado involucrado en todo tipo de procesos de extrusión durante más de 40 años. Ahora es presidente de Frankland Plastics Consulting, LLC. Contacto: jim.frankland@comcast.net o (724) 651-9196.
Contenido relacionado
Extrusión de plásticos: entienda la viscosidad y temperatura de fusión
Comprenda cómo la viscosidad y la temperatura influyen en la extrusión de plásticos y su relación con las curvas de velocidad de cizallamiento.
Leer MásExtrusión: viscosidad en polímeros no newtonianos
Explore cómo la viscosidad, cizallamiento y temperatura interactúan en polímeros no newtonianos y su impacto en la extrusión
Leer MásExtrusión de plásticos: proceso, máquinas extrusoras y aplicaciones
Desde la elección del material hasta la producción final, descubra cómo funciona la extrusión de plásticos, los distintos procesos y máquinas extrusoras disponibles y cómo elegir el material ideal según la aplicación.
Leer MásExtrusión: solucione el flujo desigual o surging en husillos de dos etapas
Explore las causas de la inestabilidad en husillos de dos etapas y descubra soluciones prácticas para garantizar un funcionamiento óptimo en extrusión de plásticos.
Leer MásLea a continuación
Entender la complejidad en el escalamiento de un mono husillo
Variables como la rata de cizalladura, la velocidad de plastificación, el tiempo de residencia y el calentamiento conductivo se ven afectados al momento de escalar un husillo.
Leer MásExtrusión: resuelva problemas de estabilidad de salida
Aprenda cómo el ajuste de la longitud llena en la zona de dosificación y la presión del cabezal pueden mejorar el rendimiento de una extrusora.
Leer MásSeñales que indican desgaste del husillo
Determinar la causa del desgaste es el primer paso para eliminarlo.
Leer Más