Moldes, de vuelta a lo básico, parte 2: selección e instalación de resortes
Siga estos pasos para una correcta selección e instalación de los resortes en los moldes.
Compartir
Lea a continuación
Nota del editor: Esta es la segunda parte de un especial con dos entregas. Puede encontrar las ligas de la serie completa a continuación:
Al momento de seleccionar un resorte para un molde comience por determinar la longitud de operación, es decir, la cantidad que debe comprimir el resorte. A modo de ejemplo, digamos que un molde tiene una carrera de expulsión de 2 pulgadas. Quizás desee utilizar los resortes azules de servicio mediano, que tienen un rango operativo recomendado de 25 % a 35 % de compresión. Suponga que la producción anual del molde sea bastante baja, alrededor de 100,000 ciclos por año, y decide utilizar el 35 % del valor de compresión recomendado. Por lo tanto, la longitud libre de su resorte debe ser de aproximadamente 2 ÷ 0.35 = 5.7 pulgadas. Ahora redondee ese valor hasta una longitud estándar de 6 pulgadas.
Si su molde tiene pines de retorno con un diámetro de ¾ de pulgada y ahí le gustaría montar los resortes, necesitaría resortes para un agujero de 1½ pulgada. En la tabla del fabricante (ver tabla), un resorte de 6 pulgadas de largo con 1½ pulgada de diámetro tiene una deflexión de 1/10 pulgadas a una carga de 17 lb. Ahora supongamos que estimó que se necesitan 100 libras de fuerza para mantener las placas de expulsión firmemente contra los botones de parada. Supongamos también que el molde es de tamaño medio y que le gustaría utilizar un total de cuatro resortes. Por lo tanto, cada resorte debe tener 100 ÷ 4 = 25 lb de fuerza de precarga. En conclusión, la distancia de precarga debería ser 25 ÷ 17 = 1.47 décimas de pulgada o 0.147 pulgadas.
No se recomienda que el resorte sea demasiado débil o demasiado fuerte. Si es demasiado débil, los resortes podrían no realizar su función prevista. Si es demasiado fuerte, puede ocultar problemas en los pines de expulsión, elevadores o sistema de expulsión guiado. Si no está seguro de cuánta fuerza se requiere, es mejor estar en el lado bajo que en el lado alto, porque puede agregar espaciadores detrás de un resorte o cambiar a una clasificación (color) diferente para aumentar la fuerza. Nota: es muy poco probable, pero no completamente imposible, que la fuerza de resorte total utilizada en un molde exceda la fuerza de expulsión disponible de la máquina.
Ahora que ha seleccionado los resortes adecuados, debe agregarlos a su plano de molde. El primer paso es verificar si existe la posibilidad de que el resorte se doble cuando se comprime. Como regla general, si la longitud libre es más de cuatro veces el diámetro, podría presentarse un problema de pandeo. En el ejemplo anterior, la longitud libre fue de 6.0 pulgadas y el diámetro de 1½ pulgada. Dado que 6 ÷ 1.5 = 4, existe una pequeña posibilidad de que el resorte se doble durante la compresión.
Para evitar que esto suceda, monte el resorte sobre un vástago o pin de diámetro recomendado, guíelo en una cavidad de diámetro recomendado, o ambos, como se muestra en la Fig. 1. Nota: tanto el diámetro exterior del pin como el interior de la cavidad deben ser lisos para evitar la abrasión del resorte.
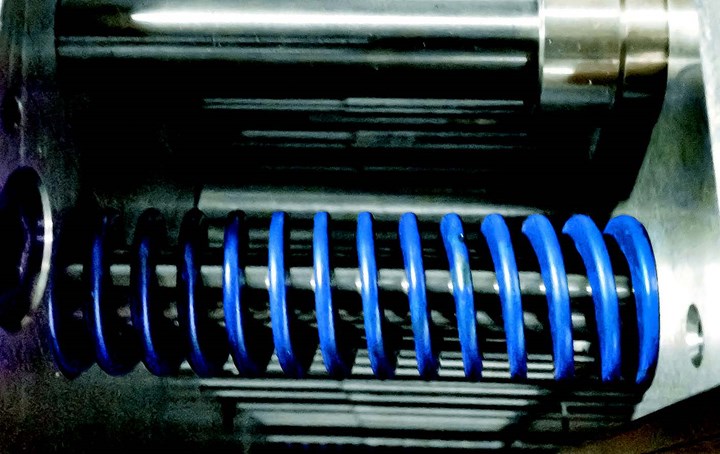
Resorte soportado por un pin y una cavidad.
Si el resorte está montado en una cavidad, la parte inferior de esta debe ser plana. Los resortes deben trabajar contra una superficie plana para proporcionar una tensión uniforme en las espiras cuando se comprimen. Mida el diámetro del resorte para determinar qué tamaño de radio puede agregar a la esquina interior. Incluso, si solo puede agregar un radio muy pequeño, es mejor que una esquina muy afilada.
Hay una ventaja al montar un resorte sobre un vástago o pin. Si el resorte se rompe, como se muestra en la Fig. 2, las pequeñas partes de acero endurecido quedarán retenidas y el molde no se dañará.
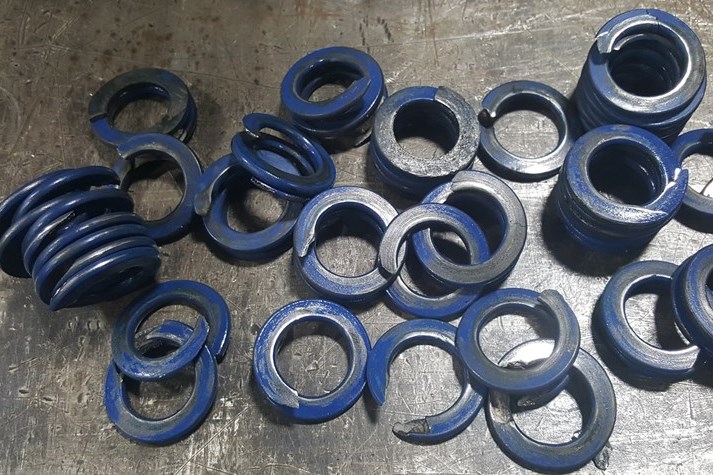
Fig. 2. Resortes rotos.
Es común que un diseñador de moldes monte un resorte sobre los pines de retorno. Una ventaja de esta ubicación es que normalmente hay un botón de parada debajo de la placa de expulsión, para evitar que las placas se doblen. Sin embargo, dependiendo del diámetro de los resortes, estos pueden extenderse más allá de los bordes exteriores del molde y requieren un alivio en la placa B, como se muestra en la Fig. 3.
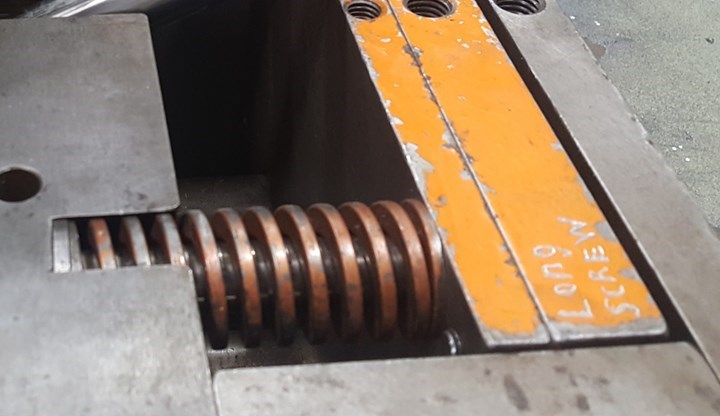
Fig. 3. Placa B con espacio para el resorte.
Si bien el montaje de resortes sobre los pines de retorno es muy común, a menudo resulta mejor montarlos sobre los pines de expulsión guiados o sobre su propio pin en las proximidades de donde las perforaciones de la máquina tocan la parte posterior de la placa de expulsión. Esto ayudará a evitar que las placas de expulsión se flecten.
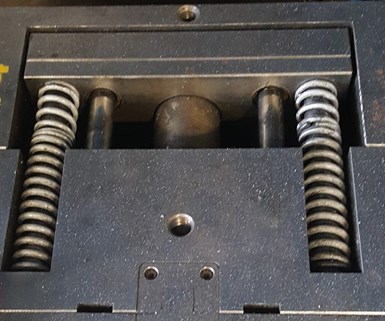
Fig. 4. Resortes apilados.
A veces, su proveedor no puede proporcionar la longitud del resorte que necesita. En un caso como este, es aceptable apilar los resortes uno encima del otro, como se muestra en la Fig. 4. Sin embargo, a diferencia de la Fig. 4, la pareja de resortes debe tener la misma longitud, para evitar comprimir en exceso los resortes más cortos. Los resortes apilados también son beneficiosos para evitar o minimizar los efectos de la frecuencia de resonancia y el rebote, que están fuera del alcance de este artículo y rara vez son un problema en las aplicaciones de moldes de inyección.
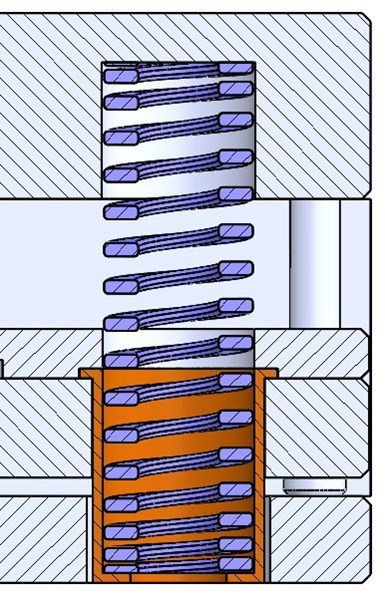
Fig. 5. Resorte con jaula.
En ocasiones, no hay suficiente espacio para instalar los resortes dentro del alojamiento del expulsor. En algunos casos es posible superar el problema mediante una jaula de resorte, como se muestra en la Fig. 5. El hombro de la jaula está atrapado entre las placas de expulsión. El cuerpo de la jaula puede extenderse hasta el lado posterior de la placa de expulsión. Las jaulas le permiten extender otras 2½ pulgadas.
A veces, simplemente, no hay suficiente espacio para instalar los resortes dentro del alojamiento del expulsor, incluso con una jaula de resortes. En un caso como este, puede instalar los resortes en la parte exterior del molde, como se muestra en la Fig. 6. Hay varias formas de hacerlo, limitadas únicamente por su imaginación. Algunos moldeadores prefieren el montaje exterior porque pueden ver fácilmente el estado de los resortes. A otros moldeadores no les gusta este método porque los resortes expuestos están sujetos a daños durante la manipulación del molde.
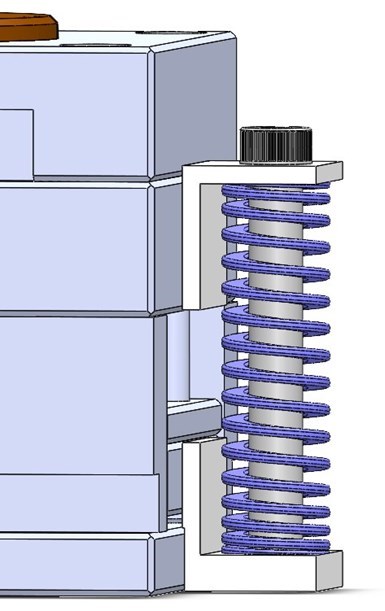
Fig. 6. Resorte montado externamente.
Debe tener cuidado al trabajar alrededor de resortes. Los espacios entre espiras son puntos de pellizco y los resortes comprimidos tienen una energía potencial significativa, lo que puede causar una variedad de situaciones peligrosas. Los moldes con placas de expulsión con resorte deben tener guardas para protección personal. Si alguna vez ha visto una placa expulsora volver a su posición mucho después de lo debido, ya sabe a qué me refiero.
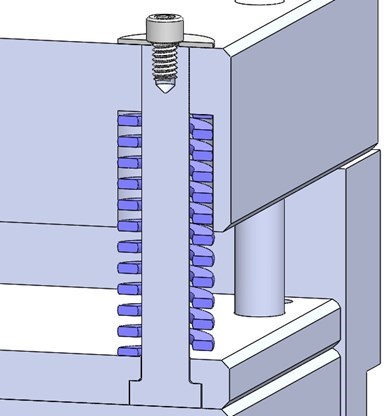
Fig. 7. Taladre y rosque las caras de dos pasadores de retorno diagonalmente opuestos para que los tornillos con arandelas puedan retener el sistema de expulsión en su posición.
Los resortes precargados que se utilizan para retener las placas de expulsión pueden ser un problema al ensamblar los alojamientos de expulsión en el banco de herramientas. Un truco consiste en perforar y roscar las caras de dos pines de retorno opuestos en diagonal, de modo que los tornillos con arandelas puedan retener el sistema de expulsión en su posición, como se muestra en la Fig. 7.
La mayoría de los problemas que surgen cuando se utilizan resortes suelen deberse a la aplicación y uso incorrectos. Aquí hay algunos consejos para asegurarse de que sus resortes funcionen adecuadamente:
• Trabaje siempre dentro de los límites físicos del resorte y las clasificaciones recomendadas.
• Nunca mezcle resortes de diferentes longitudes o clasificaciones.
• Nunca corte o maquine el extremo de un resorte a otra longitud deseada o el diámetro exterior e interior. Esto puede cambiar el temple del material y afectar negativamente el desempeño del resorte. La alteración de un resorte de su estado de fabricación conduce, casi inevitablemente, a un problema o falla.
• Nunca ponga una restricción al movimiento de las espiras. Esto puede causar una falla temprana en el resorte.
• Asegúrese de que los resortes estén libres de obstáculos. Algunos moldes expulsan piezas pequeñas con tanta fuerza que pueden terminar dentro de la carcasa del expulsor y entre las espiras de un resorte.
• Realice el mantenimiento preventivo de forma regular. Reemplace los resortes a intervalos apropiados para evitar tiempos de paro. Reemplace todos los resortes al mismo tiempo para asegurar una distribución uniforme de la carga.
• Inspeccione periódicamente los resortes en busca de corrosión. Esto puede hacer que pierdan su fuerza y fallen.
• La especificación típica de resistencia al calor de un resorte es 445 ºF (230 ºC). Después de eso comienzan a perder una cantidad considerable de fuerza debido a la relajación del resorte. Las temperaturas de los resortes aumentan por encima de la temperatura ambiente cuando se encuentran en funcionamiento (ciclando). Cuanto más rápidos sean los ciclos del molde, mayor será la cantidad de calor generado, especialmente cuando se utilizan múltiples impulsos de expulsión. Esto rara vez es un problema con la mayoría de los moldes. Sin embargo, puede tener problemas cuando el molde usa aceite caliente en lugar de agua de torre o enfriador, y el calor se transfiere con el tiempo del molde a los resortes. Consulte al fabricante de resortes en aplicaciones de altas temperaturas como esta.
Por último, debe considerar cuidadosamente la cantidad de fuerza de precarga cuando utilice resortes en moldes con 3 placas u otras situaciones similares. La máquina de moldeo debe superar la fuerza de precarga para entrar en una presión de cierre alta. Esto requiere un aumento en el valor de cierre a baja presión del molde. Infortunadamente, ese valor protege el molde de daños.
La mayoría de las pautas y recomendaciones mencionadas en este artículo también funcionan para otras aplicaciones dentro de un molde de inyección, como resortes en levas, insertos flotantes, válvulas de aire personalizadas, etc.
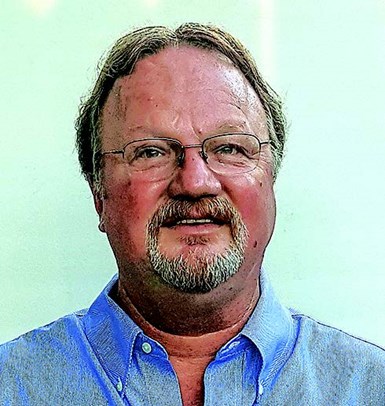
Jim Fattori
Jim Fattori es un moldeador de inyección de tercera generación con más de 40 años de experiencia en moldeo. Es el fundador de Injection Mold Consulting LLC, y también es ingeniero de proyectos para una gran moldeadora de múltiples plantas en Nueva Jersey. Contacto: jim@injectionmoldconsulting.com; injectionmoldconsulting.com.
Contenido relacionado
Enfriamiento en moldes de inyección con CO2 líquido
Manufactura aditiva y enfriamiento localizado con CO2 son las nuevas soluciones que está empleando un moldeador de productos para las industrias médica y automotriz, con el fin de catapultar su productividad y calidad.
Leer MásMétodos efectivos para retener pines en moldes de tres placas
En la fabricación de moldes de inyección, asegurar la correcta retención de las placas es crucial para evitar fallos y prolongar la vida útil del equipo. Desde el uso de resortes en moldes grandes hasta la implementación de pines retenedores con diseños avanzados, cada detalle cuenta para prevenir el desgaste y la formación de rebabas.
Leer MásSimulación avanzada vs. tradicional en moldeo por inyección
Explore el impacto del moldeo virtual en la producción de plásticos. ¿Cómo anticipar defectos y adaptar procesos de inyección? Encuentre respuestas aquí.
Leer MásMeximold 2024: la feria líder en moldes y moldeo regresa a Querétaro
Meximold 2024 se llevará a cabo los días 9 y 10 de octubre en el Querétaro Centro de Congresos, con la participación de más de 140 compañías expositoras, un programa de conferencias de alto nivel y oportunidades de networking y negocios B2B.
Leer MásLea a continuación
Cómo dimensionar compuertas, canales y bebederos, parte 4: acabado superficial de los canales
Cómo hacer que el tamaño del bebedero, canales y compuerta se acerquen a los valores ideales en el primer intento.
Leer MásCómo dimensionar compuertas, canales y bebederos, parte 5: consejos y trucos
Haga que el tamaño del bebedero, canales y compuerta del molde se acerquen a los ideales la primera vez.
Leer MásMoldes, de vuelta a lo básico: resortes de compresión
Algunos talleres de moldes insisten en que todos sus moldes tengan resortes para devolver las placas de expulsión. Afortunadamente, hay muchos para elegir. Este artículo se centra en los resortes de compresión para moldes de inyección.
Leer Más