Cómo dimensionar compuertas, canales y bebederos, parte 2: tipos de compuertas
El mes pasado, hablé sobre la importancia de la profundidad y ancho de compuerta. Este mes, me centraré en dos tipos diferentes de compuertas, así como en la longitud y el tiempo de congelación o sellado.
Compartir
Nota del editor: Esta es la segunda parte de un especial con cinco entregas. Puede encontrar las ligas de la serie completa a continuación:
Parte 4: acabado superficial de los canales.
Hay diferentes tipos de compuertas. Las más comunes son las cónicas porque son los menos costosas de mecanizar. Los sub-gates o compuertas submarinas en forma de "D" y cincel también son muy comunes.
Para determinar el tamaño de una compuerta submarina cónica, comience suponiendo que la parte se va a inyectar por el borde. Usando las pautas discutidas en la columna del mes pasado, calcule la profundidad y el ancho de la compuerta. Multiplique la profundidad por el ancho para obtener el área de flujo. Luego convierta esta área en un diámetro. De esa manera, el diámetro de la compuerta tiene un área equivalente a una compuerta de borde. La fórmula es:
Diámetro de compuerta = √ (profundidad de la compuerta de borde × ancho ÷ π) × 2
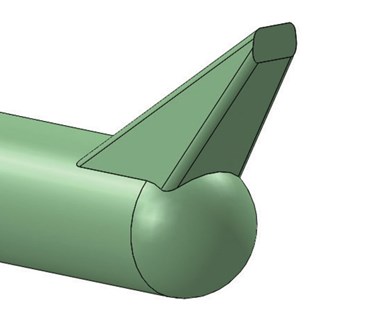
Fig. 1 Compuerta submarina tipo cincel o cuña.
Para compuertas cónicas o en forma de "D", este diámetro es del tamaño de un pin de medición que puede pasar a través del orificio. Es el diámetro menor compuerta elíptica. No es el diámetro principal de la elipse, ni el área completa de la elipse, ni la forma en "D". Si lo piensa, esto es similar a comparar el área de flujo de un canal completo con uno trapezoidal, parabólico o cualquier otra forma de canal.
Si bien las compuertas submarinas cónicas y en "D" son las más comunes, no son las más deseables. No se puede controlar el tiempo de congelación o sellado de la compuerta y el flujo de forma independiente. Si tiene una longitud de flujo larga, la compuerta debería ser más grande para llenar la cavidad. Esto hace que el tiempo de sellado sea innecesariamente más largo. El tipo preferido de compuerta submarina tiene forma de cincel o cuña (Figura 1). La profundidad y el ancho deseables son las mismas dimensiones que usaría para una compuerta de borde. Esto le permite controlar el tiempo de sellado y la longitud del flujo de forma independiente sin tener que extender el tiempo del ciclo. Otra ventaja de esta compuerta es que deja un vestigio más pequeño que una compuerta submarina cónica, especialmente cuando la compuerta se encuentra en una pared que tiene una inclinación pronunciada o una superficie redondeada. También tiene menos posibilidades de producir escamas que dañen el molde.
Compuertas directas
La compuerta directa se utiliza en moldes de una sola cavidad. No hay canal o compuerta tradicional. El orificio del buje o bebedero es efectivamente la compuerta. El tamaño del orificio del buje es una de las dimensiones menos entendidas en los diseños de moldes, especialmente con piezas de compuerta directa.
El dimensionamiento de una parte con compuerta directa puede ser un desafío difícil. Idealmente, se desea que el diámetro de salida del bebedero donde se encuentra con la pieza sea aproximadamente 1,5 veces el espesor de la pared de la pieza. Por ejemplo, si la pieza tuviera un espesor de pared de 0.100 pulgadas, el diámetro de salida del bebedero sería de aproximadamente 0.150 pulgadas. Si es mucho más grande que eso, se extenderá el tiempo del ciclo debido a que la presión y tiempo de sostenimiento deben ser lo suficientemente grandes como para evitar un rechupe o hundimiento en la superficie opuesta a la inyección. También puede ser un desafío evitar manchas en la superficie, especialmente porque las piezas con compuerta directa generalmente no tienen un pozo frío para atrapar y retener el material frío en la punta de la boquilla de la máquina.
Cuando considero cuál debería ser el diámetro del orificio de entrada u "O", empiezo por considerar qué tamaño usaría si la pieza tuviera una compuerta de borde, tal como lo hice en el ejemplo anterior Eso facilita determinar cuál debería ser el tamaño mínimo del orificio. Supongamos que la parte tienen una compuerta de borde y tiene 0.050 pulgadas de profundidad × 0.200 pulgadas de ancho. Por lo tanto, el área de flujo es igual a 0.050 × 0.200 pulgadas. = 0.100 pulgadas^2. Entonces un diámetro equivalente sería la raíz cuadrada de (0.100 ÷ π) × 2 = 0.113 pulgadas.
Por lo tanto, ahora conocemos los diámetros ideales de entrada y salida del bebedero para esta parte con compuerta directa. Lograr estos valores se basará en la longitud y el cono interno del bebedero y ahí es donde las cosas se ponen difíciles, si no imposibles. En este ejemplo, para lograr un diámetro de entrada de 0.113 pulgadas y un diámetro de salida de 0.150 pulgadas con un estándar industrial de ½ pulgadas/pie (2.386°) se necesitarían solo 0.89 pulgadas de longitud. Probablemente no sea lo suficientemente largo como para ir desde la cara de la placa de sujeción hasta la parte. A menudo, puede minimizar la longitud total del buje del bebedero perforando la placa de sujeción y, a veces, una parte de la placa de cavidad.
Una vez monté la parte inferior de la cabeza de un buje de bebedero directamente contra la parte posterior de un inserto de cavidad. La presión de contacto de la boquilla desde el barril de la máquina fue lo suficientemente fuerte como para romper los pernos y empujar el inserto de la cavidad fuera de su lugar y al suelo. Cuanto más grande es la máquina, mayor es la fuerza de contacto de la boquilla. Por lo tanto, si sigue esta ruta, seleccione el tamaño y la cantidad de tornillos que retienen el inserto con esto en mente.
También puede hacer un bebedero personalizado y reducir el cono interno del estándar de 2.38°, a solo 1° o 2°. Elija en ángulo que crea va a funcionar correctamente según el espesor del bebedero y la contracción del material. La mejor manera de hacerlo es comprar un buje con una dimensión "O" más pequeña. El orificio más pequeño se convierte en el orificio de inicio para el electroerosionado por hilo, al tamaño y cono deseados.
No es conveniente reducir o aumentar la dimensión "O" estimada del bebedero que controla la presión de inyección requerida y el tiempo de sellado. Si la longitud es un problema, lo único que puede hacer es vivir con un diámetro de salida más grande. Para minimizar el aumento en el tiempo del ciclo, el bebedero necesita enfriamiento directo. El enfriamiento indirecto a través de canales de agua cerca al bebedero generalmente no es muy efectivo, a menos que el bebedero se maquine directamente en el inserto de la cavidad, lo que significa que no hay un buje separado para el bebedero. Usar un buje hecho de una aleación de cobre, o uno que tenga enfriamiento conformal, sería muy útil.
Desafortunadamente, muchas partes con compuerta directa son inyectadas y expulsadas en el mismo lado (expulsión en reversa) y el buje del bebedero es extremadamente largo. La mejor solución en un caso como este es considerar el uso de un buje o bebedero caliente. Si cree que el costo de un bebedero caliente no es rentable, puede usar la tabla adjunta que detalla el número de ciclos que se necesitan para recuperar su costo promedio. El ROI se basa en la tarifa por máquina por hora y los ahorros esperados en el tiempo de ciclo. Una vez que alcanza los ciclos ROI, comenzará a ver las ganancias en su pieza moldeada.
Estos son números conservadores porque no tienen en cuenta el material ahorrado y la posibilidad de reducir los requisitos de mano de obra. Tampoco tiene en cuenta la tasa de rechazo reducida. Trate de pedir bebederos calientes que tengan un pequeño canal frío de alimentación y tengan una punta reemplazable. De esa manera, puede comprar puntas de diferente longitud para colocar el mismo buje en diferentes moldes y obtener aún más ahorros. Por último, ya sea que tenga un canal frío o caliente, agregue un radio de v0.005 a 0.025 pulgadas a la salida. A los termoplásticos no les gustan los filos o aristas vivas de ningún tipo.
Longitud de compuerta de borde
Para analizar las compuertas de borde, primero debemos analizar la longitud. La longitud en una compuerta de borde es una sección corta y recta que conecta la superficie exterior de la pieza al canal, como se muestra en la Figura 2. La longitud en una compuerta tiene un efecto directo sobre la viscosidad del material. Longitudes largas imparten más cizallamiento al material, lo que a su vez reduce la viscosidad del material. Eso puede ser beneficioso, si no es necesario, para ayudar a mejorar la longitud del flujo hacia la cavidad. Aunque largas longitudes también pueden ser perjudiciales y crear quemaduras en materiales sensibles como el PVC.
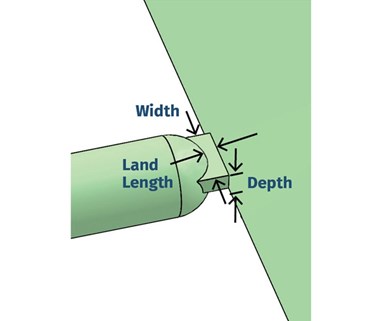
FIG 2. Terminología en compuertas de borde.
Cuanto más larga sea, mayor será la presión requerida para empujar el material a través de la compuerta, como respirar a través de un popote largo versus uno corto. Sin embargo, dado que mayores longitudes reducen la viscosidad del material, se necesita menos presión para llenar las cavidades, especialmente a altas velocidades de inyección.
Hay una regla general que dice que la longitud de la compuerta debe ser la mitad de la profundidad. Esta es otra "regla" que sería prudente olvidar. He visto moldes con longitudes de cero y he visto moldes con longitudes de más de 1½ pulgada. Ambos funcionaron bien para su aplicación particular. El consenso general entre los expertos de la industria es que la longitud debe estar entre 0.020 y 0.045 pulgadas. Esa es una regla general bastante buena, pero las reglas siempre tienen algunas excepciones, que desafortunadamente rara vez se mencionan.
Su decisión sobre qué tan larga debe ser la compuerta debe basarse en la velocidad de inyección esperada. Si va a inyectar extremadamente rápido, como con una parte de paredes delgadas que tiene una profundidad de compuerta poco profunda, generalmente es necesario una longitud de tierra corta. Si va a inyectar lentamente, como con una parte de pared gruesa que tiene una compuerta muy profunda, la longitud puede ser considerablemente más larga, porque hay muy poca pérdida de presión al pasar por esa compuerta. La longitud ideal también depende en cierta medida del material. Siempre revise las pautas de diseño del fabricante del material, pero tenga en cuenta que la mayoría de las guías de diseño son de naturaleza general.
Siempre es mejor comenzar con una longitud un poco más larga. Si hay un problema con la cizalladura o la presión de inyección, puede aumentarla o modificar el acero. No haga que el procesador tenga que trabajar con una compuerta de tamaño incorrecto. La ventana de procesamiento resultante será estrecha y la probabilidad de rechazos aumentará exponencialmente. Haga lo que haga, solo asegúrate de que todas las compuertas en un molde de múltiples cavidades tengan exactamente la misma profundidad, ancho y largo de tierra. De lo contrario, obtendrá un desequilibrio de la cavidad.
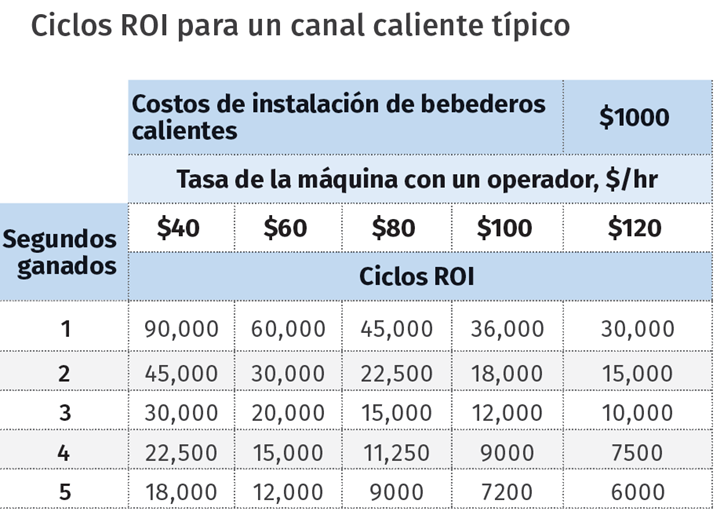
Ciclos ROI para un canal caliente típico.
Sellado de la compuerta
En mayo deL 2000, Bill Fierens (ahora Ingeniero senior de desarrollo técnico en M. Holland Co.) y Sean Mertes (ahora ingeniero de desarrollo de aplicaciones en Amco Polymer) presentaron un documento en la SPE ANTEC sobre “Longitud de las compuertas y sus efectos sobre la pérdida de presión en la compuerta y cavidad." El documento afirmó brevemente que las compuertas cortas pueden aumentar el tiempo de sellado. Hablé con ambos autores, y aunque no hay datos empíricos que respalden esta afirmación, todos creemos que es cierto por dos razones principales. Primero, las compuertas cortas tienen menos acero en el área de inyección y esta es una variable primaria en la ecuación matemática para calcular la tasa de transferencia de calor por conducción. En segundo lugar, cuanto más corta es la compuerta, más cerca estará el canal de la compuerta, entregando calor adicional en esta área crítica. Además, si la pared de la pieza moldeada es gruesa, también entrega calor adicional en el área crítica. Como se mencionó anteriormente, las partes de pared gruesa o las partes con canales grandes y redondos pueden requerir compuertas más largas.
Si bien estoy seguro de que una compuerta con una longitud de una pulgada se solidificará o sellará más rápido que una con 0.100 pulgadas de longitud, me resulta difícil creer que haya mucha diferencia en el tiempo de sellado entre una compuerta de 0.020 pulgadas de longitud y una con 0.045 pulgadas. Además, dado que a menores longitudes se desarrolla menos cizallamiento, habrá menos aumento de temperatura tanto en el material como en el acero. Si el tiempo de sellado fuera el culpable de un tiempo de ciclo extendido, creo que lo más probable que no sea porque la compuerta es demasiado corta, sino porque es demasiado profunda. Sin datos empíricos, nunca lo sabremos con certeza.
Esto trae a colación otro punto que vale la pena mencionar. Las empresas que han adoptado métodos científicos de moldeo realizan estudios de sellado en sus moldes. La columna de noviembre de 2015 de John Bozzelli, titulada "Como realizar el estudio de sellado correctamente", es una guía exhaustiva sobre cómo realizar este estudio. Básicamente, se comienza con un tiempo de sostenimiento muy corto en la segunda etapa, aproximadamente 1 segundo, y luego pesa la(s) parte(s). A continuación, se aumenta gradualmente el tiempo de sostenimiento mientras mantiene el tiempo del ciclo, hasta que el peso de la pieza ya no aumente más. Ahora ya sabe cuánto tiempo tarda la compuerta en solidificarse o sellarse, lo que evita que el material se devuelva al canal y no permite un buen empacado de la pieza. Si desea utilizar una condición de "compuerta no sellada", aún necesita realizar este estudio para saber en qué tiempo se sella la compuerta y usar un tiempo menor al encontrado. De cualquier manera, usted sabe cuánto debe ser el tiempo de sostenimiento antes de comenzar la rotación del husillo.
Lo que un estudio de sellado no dice es si la compuerta es poco o demasiado profunda. Tampoco te dice si la longitud es demasiado larga o corta. La parte, la máquina de moldeo y las pruebas físicas le dirán esas cosas. Si la parte aún tiene marcas visibles de hundimientos/rechupes, vacíos internos o si es dimensionalmente más pequeña después de que la compuerta se haya sellado, probablemente sea necesario aumentar la profundidad de la compuerta. Esto aumentará el tiempo de sellado y se podrá empaquetar más plástico en la cavidad. Como acabo de mencionar, si la compuerta tarda mucho tiempo en sellarse, probablemente es demasiado profunda. Pero también es posible que la presión de sostenimiento sea demasiado alta y el material semi-solidificado en la compuerta sea empujado continuamente hacia la cavidad. Si la pérdida de presión en la compuerta es extremadamente alta o se presenta efecto “jetting”, la compuerta podría ser poco profunda o demasiado larga.
Lea a continuación: Parte 3: compuertas de borde.
Acerca del autor
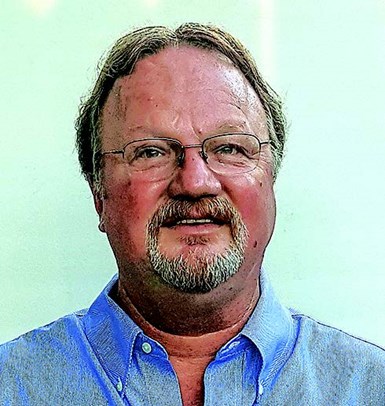
Jim Fattori
Jim Fattori es un moldeador de inyección de tercera generación con más de 40 años de experiencia en moldeo. Es el fundador de Injection Mold Consulting LLC, y también es ingeniero de proyectos para una gran moldeadora de múltiples plantas en Nueva Jersey. Contacto: jim@injectionmoldconsulting.com; injectionmoldconsulting.com.
Contenido relacionado
Métodos efectivos para retener pines en moldes de tres placas
En la fabricación de moldes de inyección, asegurar la correcta retención de las placas es crucial para evitar fallos y prolongar la vida útil del equipo. Desde el uso de resortes en moldes grandes hasta la implementación de pines retenedores con diseños avanzados, cada detalle cuenta para prevenir el desgaste y la formación de rebabas.
Leer MásTratamientos químicos en sistemas de transferencia de calor
Entienda el riesgo de biofilmes y corrosión en sistemas de agua y cómo un tratamiento químico adecuado puede extender la vida útil de su equipo.
Leer MásVamos a reconectar con innovación y tecnología en Meximold 2023
En un mundo que ha experimentado transformaciones inimaginables, en el que la virtualidad y la digitalización han sido protagonistas indiscutibles, nos entusiasma saber que los eventos presenciales son más necesarios que nunca, y qué mejor manera de reconectar que a través de un encuentro de vital importancia para la industria manufacturera: Meximold.
Leer MásEnfriamiento en moldes de inyección con CO2 líquido
Manufactura aditiva y enfriamiento localizado con CO2 son las nuevas soluciones que está empleando un moldeador de productos para las industrias médica y automotriz, con el fin de catapultar su productividad y calidad.
Leer MásLea a continuación
Tornillos guía en moldes de inyección: funciones y aplicaciones
Descubra las funciones clave de los tornillos guía en moldes de inyección, su impacto en el proceso y cómo elegir el tornillo adecuado para su proyecto.
Leer MásAhorre tiempo y dinero: use un checklist en el diseño de sus moldes
Aquí hay 15 ejemplos de problemas comunes de moldeo que ocurren durante una prueba inicial de molde. Muchos de ellos podrían evitarse o corregirse con una lista de verificación o checklist proactivo.
Leer MásCómo dimensionar compuertas, canales y bebederos, parte 1: paso a paso
Obtenga el tamaño ideal de la compuerta o punto de inyección, el canal y el bebedero en el primer intento, sin perder mucho tiempo en fórmulas extremadamente complicadas.
Leer Más