Moldeo por inyección: logre una supervisión de la producción efectiva
Descubra los elementos clave para implementar un sistema MES eficaz. Aprenda a abordar los desafíos y optimizar la supervisión de la producción en tiempo real.
Hasta la fecha he escrito algunos artículos sobre la supervisión eficaz de los procesos, defendiendo la supervisión por parte de terceros como la opción más sólida para conseguirlo.
Dicho esto, no estoy seguro de haber transmitido lo importante que es tener también un sistema de supervisión de la producción en tiempo real. Lo ideal es que se trate de un sistema MES que pueda utilizarse junto con la supervisión del proceso.
Hace algún tiempo trabajé en una empresa donde formé parte de un equipo encargado de identificar e integrar con éxito un sistema de este tipo en la operación. Espero que esta columna explique mi proceso de pensamiento y lo que buscaba en este tipo de sistema para gestionar la producción y proporcionar una supervisión eficaz del proceso.
También compartiré algunos de los obstáculos a los que podría enfrentarse con este tipo de proyecto, o al menos, a los que mi equipo y yo pudimos dar solución.
Encontrar el mejor ajuste
Mientras trabajaba como director de servicios técnicos compartidos en el sector médico de nuestra industria, se me encargó la tarea de identificar un sistema de supervisión de la producción en tiempo real, el mencionado MES.
Esta tarea se había intentado muchas veces a lo largo de los años en esta empresa y se había topado continuamente con obstáculos debido a que los sistemas no proporcionaban lo que todo el mundo quería. Se habían propuesto muchos sistemas al personal directivo, y cada uno de ellos fue rechazado porque ninguno cumplía las expectativas o los requisitos de todos.
Lo primero que comprendí fue que ningún sistema out-of-the-box sería perfecto para todo el mundo, pero si consiguiéramos identificar un sistema que se pudiera personalizar, lograríamos la meta.
El objetivo del proyecto debe ser permitir que todos los departamentos hagan sus aportes al sistema previsto. Dicho esto, tampoco hay que permitir que las exigencias de los demás paralicen el proyecto. Cuando esto ocurre, hay que tomar una decisión que puede no ser popular para todos, pero que es necesaria para que el proyecto siga adelante.
El programa de supervisión de la producción Intouch ofrece una vista de tablero de mando de una planta para obtener una rápida visión general de una empresa o planta de producción.
Créanme, tuve que tomar algunas decisiones, y sabía que el objetivo sería modificar el sistema o modificar nuestros procedimientos de producción, según fuese necesario, para aprovechar al máximo sus capacidades.
Por lo tanto, sin ignorar las necesidades o preocupaciones de mis colegas, entendía que el sistema o la empresa podrían evolucionar para satisfacerlas en el futuro. No quería que este proyecto se estancase de la misma manera y tuviera el mismo destino que los intentos anteriores.
La supervisión de los procesos sin la importancia que merecen
Muchos de los sistemas que ya se habían considerado eran predominantemente sistemas de supervisión de la producción que tenían algunas capacidades de supervisión del proceso. Puesto que mi experiencia ha sido casi exclusivamente en el moldeo científico, le di prioridad a la supervisión del proceso como un requisito crítico del sistema.
El problema que tenía con la mayoría de los sistemas de supervisión de la producción disponibles en el mercado era que no le daban la importancia merecida a sus capacidades de supervisión del proceso.
Este es un buen momento para señalar que el sistema que se requería para este moldeador en particular tenía que ser capaz de proporcionar una supervisión eficaz del proceso, por parte de terceros, para lograr uno de los principales objetivos establecidos para el proyecto.
Dado que el proceso de moldeo por inyección forma parte de la cualificación en el moldeo médico, se requiere la verificación del proceso a lo largo de un lote de fabricación. La práctica en ese momento era que un técnico de proceso documentara los resultados del proceso calificado, cuatro veces al día, en una lista de verificación.
Esto significaba que uno de nuestros recursos técnicos altamente capacitados dedicara el tiempo a hacer papeleo en lugar de utilizar sus habilidades en actividades de mayor valor agregado. Además, los errores tipográficos podían generar desperdicios importantes. Si el técnico de procesos anotaba accidentalmente un nueve en lugar de un seis en esta lista de verificación, podía dar lugar a que las piezas buenas fueran desechadas.
En el sector médico no podíamos confiar únicamente en la verificación de la forma, el ajuste y la función de la pieza para liberar el producto. Teníamos que demostrar que habíamos producido las piezas dentro de los límites del proceso verificado.
Para eliminar lo que Lean Manufacturing denominaría “desperdicio de habilidades”, el sistema de supervisión del proceso debe ser capaz de capturar, de forma independiente, estos resultados. Además, debe ser apto para segregar un disparo que no esté dentro de los límites de control aprobados y poder interrumpir el ciclo de la máquina si el número de disparos segregados supera un límite de umbral predeterminado.
Una gran lección que aprendí fue la importancia de desarrollar por adelantado los requisitos críticos del sistema con su equipo, basado en los procedimientos actuales de la operación, antes de empezar a evaluar los posibles sistemas de supervisión.
En este caso, merece la pena contar con miembros del equipo que realmente realicen el trabajo. Pueden aportar detalles que a menudo pasan por alto los que no están directamente en la operación. En cuanto a los requisitos del sistema, tenga en cuenta que, si su cliente no requiere este tipo de verificación del proceso, es posible que la supervisión del proceso no tenga que ser completamente independiente de las capacidades nativas de supervisión del proceso de la máquina.
Si este es el caso, los requisitos para su operación podrían reducirse a un sistema que utilice las capacidades de supervisión de la máquina y permita que las inyectoras se conecten en red al sistema. Dicho esto, recuerde que los sistemas eficaces de supervisión de procesos son sistemas complejos que requieren experiencia en procesos, máquinas y moldes para su desarrollo.
Las empresas dedicadas a la supervisión de la producción son expertas en sistemas MES, pero no suelen serlo en moldeo por inyección.
Esto se hizo evidente al revisar las capacidades de cada sistema. Las empresas que intentan ofrecer un producto “para todos los gustos”, normalmente no llegan a ser las mejores de su clase en nada. Esa es mi opinión, y diré que hay sistemas en el mercado que han aportado el conjunto de habilidades necesarias para mejorar la supervisión de los procesos, pero están muy por detrás de los líderes de la industria en cuanto a la supervisión eficaz de los procesos.
Al principio del proyecto se hizo evidente que, si el sistema iba a supervisar un proceso de moldeo de forma eficaz y gestionar la producción de forma efectiva, teníamos que buscar un sistema independiente para cada uno, en lugar de un enfoque “todo en uno”.
Cuando recomendé por primera vez este concepto, fue bastante controvertido. Los compañeros de la dirección plantearon su preocupación por conseguir que los miembros del equipo utilizaran un sistema, por no hablar de dos, lo cual es un temor legítimo. Sea cual sea el sistema elegido, si no se utiliza, no tiene ningún valor.
Una plataforma sólida de supervisión de la producción proporcionará una visión detallada de los lotes actuales y programados, y de su rendimiento. Crédito: Intouch Monitoring.
Por supuesto, el costo era una preocupación, así como la gestión de las infraestructuras de múltiples sistemas, pero me sentía tan convencido de este enfoque que decidí centrar el proyecto en la aplicación de múltiples sistemas, cada uno de los cuales proporcionaba las mejores soluciones para los requisitos de nuestra planta. Una vez enfocado el proyecto en esta dirección, rápidamente quedó claro qué sistema de monitorización de procesos cumpliría con nuestros requisitos.
Desde el punto de vista de la supervisión de procesos, RJG llevaba años optimizando la supervisión de procesos por parte de terceros y ofrecía varios niveles de software y hardware de supervisión de procesos.
Los invité a presentar su sistema eDart al equipo y, mientras terminaban la presentación, mencionaron una empresa inglesa que había desarrollado un software de supervisión de la producción que podía funcionar con el hardware eDart de RJG.
La clave es la personalización
Intouch Monitoring ofrece un software que puede ejecutarse en la HMI (interfaz hombre-máquina) eDart, de RJG. Al principio me preocupaba que esto pudiera ser un contraargumento con respecto a la supervisión de procesos en sistemas de supervisión de la producción, el polo opuesto de lo que habíamos estado evaluando.
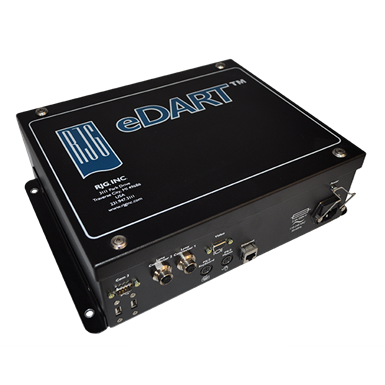
Lograr una “sincronización” entre el software de supervisión de la producción de Intouch y la supervisión del proceso del hardware eDART, de RJG, fue clave para el proyecto.
Invitamos a Intouch Monitoring (intouchmonitoring.com) a nuestras instalaciones para que nos presentara su sistema. Las diferencias entre su producto y los demás sistemas de monitorización de la producción eran evidentes. Se trataba de un sistema robusto, con un enfoque único.
Ofrecía múltiples herramientas, como programador, diagramas de Gantt y reportes de OEE, así como comunicación bidireccional con muchos sistemas ERP, incluidos los grandes del sector. Hasta ese momento estaba bastante decepcionado con los sistemas de supervisión de la producción que habíamos revisado.
En particular, me preocupaba cada vez más el hecho de que estos sistemas no tuvieran prácticamente ninguna posibilidad de personalización. Eso significaría que los procedimientos tendrían que cambiar en nuestras instalaciones para adaptarse al sistema, y el cambio podría ser problemático en la producción de piezas para la industria médica. No es solo que a la gente no le guste el cambio (a la mayoría no le gusta), sino que podría haber un costo o requerirse una aprobación del cliente, o más probablemente ambas cosas.
El enfoque de Intouch consistió en personalizar los informes, para imitar los nuestros y trabajar dentro de los procedimientos que requería nuestro cliente. Esto, así como la capacidad del software para funcionar con el hardware RJG eDart, nos convenció del sistema.
Así que ya habíamos identificado los sistemas que considerábamos nos ofrecían las mejores oportunidades de éxito, y me entusiasmó el hecho que encontráramos dos sistemas que se especializaban, cada uno, en un tipo de supervisión. Compartir el hardware aliviaría algunas de las preocupaciones mencionadas por otros miembros del equipo de gestión.
Integración de procesos y producción
Ya no había que preocuparse por el costo de las HMI de cada sistema, pero una vez que empecé a conocer mejor la integración del software Intouch con el hardware RJG eDart, me di cuenta de que seguiría el problema de conseguir que los miembros del equipo utilizaran dos sistemas.
Para empezar un nuevo lote, el operador tendría que comenzar en el software Intouch y luego regresar al eDart e iniciar el lote de nuevo. Aunque el software de monitorización de Intouch estaba instalado en el eDart, el software de Intouch no sabía que estaba en un eDart, y el eDart no tenía comunicación con el software de Intouch.
Me preocupaba la integración de los dos sistemas porque no estaban integrados en absoluto. Durante la primera reunión con ambas empresas dejé muy claro que, para que siguiéramos adelante, los sistemas debían estar integrados, y entonces este proyecto se volvió emocionante. Fue surrealista trabajar con ambos equipos, proponer ideas y desarrollar lo que finalmente se convertiría en un sistema premiado y de primera clase.
La integración en la máquina fue un éxito. El operario encontraba el siguiente lote en el software de interfaz de usuario de Intouch y, una vez seleccionado el botón de inicio, ese lote se cargaba en ambos sistemas. Las plantillas de proceso y los límites de control se llenaban automáticamente en el eDart y los estándares de ciclo se llenaban en el Intouch.
A medida que la integración evolucionaba, la necesidad de iniciar manualmente un trabajo se sustituyó por el hardware de etiquetas de molde de RJG.
Una vez que el eDart se conectaba al transductor de presión del molde o a la etiqueta del molde, Intouch cargaba de manera automática el lote en ambos sistemas: una sincronización de alta tecnología entre dos empresas líderes en supervisión.
Con el tiempo, el sistema se actualizó hasta el punto de que la máquina no se ponía en marcha si el lote no se iniciaba en el sistema de supervisión o si la temperatura del agua no se ajustaba correctamente. Hay muchas más cosas que estos sistemas podrían hacer, y podría extenderme eternamente, pero me gustaría hablar un poco del proceso de lanzamiento que utilizamos para ayudar a promover el uso del sistema.
La clave del éxito
Un sistema de control de la producción solo tiene éxito si la gente lo utiliza. Punto y aparte, fin de la frase. Si todo el mundo en su planta no está dispuesto a utilizar el sistema, entonces se convierte en una representación visual muy cara de la distribución de su planta. Esas grandes pantallas en toda la planta quedan bien, pero si eso es todo lo que quiere, se puede hacer mucho más barato.
La plataforma de Intouch proporciona un análisis detallado del OEE y gráficos Pareto de indicadores clave como el tiempo de inactividad y el rechazo.
Así que el gran reto era: ¿cómo conseguimos que todo el mundo esté dispuesto a utilizar este sistema? En primer lugar, elegir el equipo adecuado ayuda. Una de las cosas que más aprendí de mi formación en Lean fue el uso de SMEs ―expertos en materia― como parte de los proyectos de solución de problemas o de mejora continua.
Involucrar a los miembros del equipo que realmente hacen el trabajo, no solo ayuda a identificar las verdaderas causas raíz, sino que les da a esos miembros del equipo la responsabilidad de las soluciones. Soluciones que ellos mismos ayudarán a que se mantengan en el tiempo por parte sus compañeros de trabajo. La clave fue asegurarse de que los miembros de este proyecto utilizaran el sistema como parte de sus responsabilidades diarias.
La siguiente idea era tratar de afectar lo menos posible los procedimientos actuales, sobre todo si eran efectivos. Es una buena idea que el sistema se utilice junto con los procedimientos e informes que ya se están utilizando. ¿Y si los informes que genera el sistema fueran idénticos a los informes que los miembros del equipo han estado generando a mano?
Por lo tanto, este informe generado por el sistema es algo con lo que todo el mundo está ya familiarizado y se siente cómodo, pero podemos generarlo en menos tiempo, con menos recursos y, a menudo, se trata de datos en tiempo real, por lo que no hay que esperar doce horas para saber que se ha producido un 10 % de desechos.
No me malinterpreten: al final, hicimos muchas mejoras que requerían cambios, pero lo hicimos por etapas y pudimos hacerlo porque el sistema era muy versátil.
También intentamos hacer cambios que tuvieran el mínimo impacto posible en los requerimientos del cliente. El mejor ejemplo de ello fueron las listas de verificación que los técnicos de proceso completaban cuatro veces al día.
Llegamos, incluso, a realizar la calificación de la instalación en cada máquina cuando se montó el sistema para confirmar que los datos eran fiables, que un disparo fuera de especificación se rechazaba automáticamente y que los rechazos excesivos provocaban una interrupción del ciclo.
Aunque ahora podíamos proporcionar pruebas de que cada pieza empacada estaba dentro de los límites del proceso validado, el cliente seguía exigiendo la lista de verificación cuatro veces al día. Así que reté al equipo de Intouch a que nos proporcionara esta misma lista utilizando los datos de eDart que pudieran imprimirse y enviarse con cada despacho del cliente.
Como ya habíamos integrado por completo ambos sistemas, pudimos completar esta acción y liberar recursos técnicos cualificados para que se centraran en actividades de valor agregado. Esta era la parte divertida del proyecto, pero el verdadero éxito de este sistema seguía en manos de los miembros del equipo que debían utilizarlo a diario. ¿Y cómo lo hicimos? Tengo que decir que fue un plan establecido por uno de los fundadores de Intouch Monitoring. Su experiencia en la fabricación y el lanzamiento del sistema representó un plan de “gatear antes de caminar”.
Parece obvio, ¿verdad? Usamos esa frase todo el tiempo, pero si gastas un millón de dólares del presupuesto de tu jefe, verás cómo están dispuestos a ver este sistema gateando. Definitivamente es un poco más difícil cuando lo piensas de esa manera. Para nosotros no fue tan dramático, pero hubo mucha presión para que se utilizara, como debía ser.
El primer paso fue pedir al equipo que introdujera un código de tiempo de inactividad. Eso es todo. Introducir un código de tiempo de inactividad cada vez que la HMI lo solicitara. Todas las mañanas hacíamos un seguimiento del tiempo de inactividad global y del tiempo de inactividad codificado y comunicábamos los resultados a los miembros del equipo. Dedicábamos tiempo adicional a formar a los miembros del equipo con mayores deltas, y desarrollábamos un flujo de procesos y un procedimiento.
Estos flujos de procesos y procedimientos se combinarían finalmente para crear el manual del sistema de nuestra planta.
A continuación conseguimos que los montadores de moldes y los técnicos de proceso introdujeran sus propios tiempos de inactividad. La introducción de los tiempos de inactividad correctos se convirtió en algo natural.
Un técnico de proceso detendría una máquina para un cambio de molde, e inmediatamente seleccionaría detenida por “material”. Un manipulador de materiales cambiaría el material e inmediatamente cambiaría el tiempo de inactividad a “cambio”. El montador de moldes terminaría el cambio de molde y cambiaría el tiempo de inactividad a “técnico de procesos”, y así sucesivamente.
Piense en los datos que esto nos proporcionó para ayudar a reducir los tiempos de cambio. Pronto identificamos las áreas de desperdicio durante un cambio y realizamos mejoras. Una vez dominado el tiempo de inactividad, empezamos con la clasificación de los residuos. Cada nueva tarea se dominaba mucho más rápidamente que la anterior y, aunque nos llevara un poco más de tiempo que pulsar un interruptor, los resultados merecían la pena.
Puedo decir, sin ninguna duda, que participar en un proyecto como este ha sido uno de los momentos más destacados de mi carrera. Empujar al equipo a resolver problemas para añadir funcionalidad a este sistema ―algo que no se había hecho antes― y luego ver que funcionaba fue muy gratificante.
Estoy seguro de que hubo un momento en el que el equipo de Intouch se hartó de oírme decir: “Necesito (inserte aquí una petición poco razonable), ¿cuándo puede tenerlo listo?”. O que el equipo de RJG me mirara como a un loco cuando les pedí que demostraran que un recién comprado transductor de presión de cavidades sería preciso, pero que me sorprenderían unas semanas después con un equipo de verificación de transductores.
Estos sistemas pueden ser tremendamente exitosos y proporcionar ahorros en dólares. El mayor reto puede ser conseguir que todo el mundo esté de acuerdo con un sistema, y a veces solo hay que agradecer a todo el mundo sus aportes y luego tomar una decisión.
Robert Gattshall
Robert Gattshall tiene más de 22 años de experiencia en la industria del moldeo por inyección y posee múltiples certificaciones en Moldeo Científico y en las herramientas de Lean Six Sigma. Gattshall ha desarrollado varios sistemas Poka Yoke “Best in Class” con monitoreo de procesos y producción de terceros como Intouch Monitoring Ltd. y RJG Inc. Ha ocupado múltiples puestos de gestión e ingeniería en las industrias automotriz, médica, eléctrica y de producción de empaques. Gattshall también es miembro del Comité de Políticas Públicas de la Asociación de la Industria del Plástico. En enero de 2018 se unió a IPL Plastics como gerente de ingeniería de procesos. Contacto: (262) 909-5648; rgattshall@gmail.com.
Contenido relacionado
Moldeo por inyección de plásticos: inyectoras, materiales y tendencias
Desde los fundamentos hasta las mejores prácticas y últimas tendencias, desglosamos todo lo que debe saber sobre el moldeo por inyección para la producción de piezas plásticas.
Leer MásParámetros de proceso en moldeo por inyección
Conozca la importancia del primer ensayo de molde y cómo un enfoque científico puede mejorar la calidad del producto.
Leer MásPuntas de boquilla: impacto y selección en moldeo por inyección
Descubra la relevancia de las puntas de boquilla en moldeo por inyección. Aprenda sobre tipos comunes, problemas y técnicas de reemplazo.
Leer MásClaves para seleccionar el cañón correcto en inyección de plásticos
Análisis técnico sobre la elección del cañón de plastificación. Conozca las ventajas de utilizar dos cilindros y cómo maximizar la eficiencia en el moldeo.
Leer MásLea a continuación
Moldeo por soplado: guía completa y preguntas frecuentes
¿Está interesado en el moldeo por soplado? Conozca las ventajas, desventajas y fundamentos de este proceso de transformación de plásticos.
Leer MásEconomía circular de los plásticos en la realidad comercial
Estas son algunas tecnologías, ya disponibles en el mercado, que buscan ayudar a mejorar e implementar la circularidad de los plásticos.
Leer MásAsí van las proyecciones en economía circular para los plásticos
¿Qué tan cerca estamos de alcanzar la meta de lograr empaques plásticos 100 % reusables, reciclables y compostables para 2025? ¿Qué acciones vienen en curso para cumplirlas? Entrevista exclusiva con la Fundación Ellen MacArthur sobre el panorama de los plásticos en la economía circular en el mundo y en América Latina.
Leer Más