Mejoras en refrigeración de moldes para eficiencia
Descubra cómo optimizar los sistemas de enfriamiento en el moldeo por inyección para aumentar la eficiencia térmica y calidad de las piezas.
Burger & Brown Engineering, Inc. es una empresa reconocida en la industria plástica por los productos Smartflow para moldeo por inyección y por sus cursos de refrigeración científica. Sin embargo, Burger and Brown también es convertidor de plásticos y cuenta con un departamento de moldeo muy moderno y altamente automatizado.
Nuestro departamento de moldeo comenzó con una inyectora eléctrica diseñada para servir como una herramienta de laboratorio para el desarrollo de nuestros accesorios, y no pasó mucho tiempo hasta que estuvimos moldeando piezas de producción para nosotros y para otros.
En 2003, un cliente local nos contrató para desarrollar un dispensador para líquidos. Ayudamos en el diseño del artículo y el suministro de un molde con cuatro cavidades, inyección submarina y expulsión por camisa. Fue una buena oportunidad para nuestra pequeña operación de moldeo.
El artículo es de 4 pulgadas de largo con 1 pulgada de diámetro en el extremo grande. Tiene un espesor de pared de 0,033 pulgadas en el extremo chico y 0,048 pulgadas en el extremo grande. El sistema de enfriamiento consiste en canales anulares de agua en insertos de cavidad redonda y bafles o divisores de 13 pulgadas en los núcleos. El refrigerante se envía a los núcleos y cavidades a través de orificios perforados en las placas del molde, cada circuito sirve a una pareja de núcleos o cavidades.
El lanzamiento de este nuevo producto salió muy bien. Después de aproximadamente 4 años comenzamos a tener dificultades para moldear las piezas. Notamos que los circuitos de enfriamiento del núcleo solo permitían un flujo mínimo y los núcleos estaban extremadamente calientes. Durante la expulsión, las piezas tendían a enrollarse en los núcleos calientes, incluso con un tiempo de enfriamiento muy largo. Enviamos el molde a nuestro taller interno para investigar el problema.
Identificación y solución de problemas de refrigeración
El problema no fue difícil de encontrar. Los circuitos de los bafles estaban severamente obstruidos, tanto que era imposible quitar elementos de división de los núcleos. Perforamos los bafles largos, limpiamos los conductos de refrigeración e instalamos nuevos bafles.
Habíamos aprendido una lección útil sobre el mantenimiento del molde y el sistema de agua de refrigeración. Desde entonces, hemos mejorado el mantenimiento del molde y del refrigerante y hemos producido piezas con un buen ciclo desde el 2007.
Recordar esta experiencia de hace años nos hizo pensar en diseñar algunos experimentos para cuantificar los efectos de los depósitos de calcio en los canales de refrigeración. Construimos un núcleo redondo simulado, un cilindro de acero P-20 con un diámetro de 1,5 pulgadas y 6 pulgadas de largo con un canal ciego de 7/16 pulgadas de diámetro que se puede configurar para funcionar como un circuito tipo bafle o fuente. Los ensayos se realizaron con un circuito tipo fuente estándar.
Utilizamos sensores de temperatura RTD de precisión a medio camino entre el diámetro externo del núcleo y la pared del conducto de enfriamiento para medir la temperatura del acero. Proporcionamos una entrada de calor a la “superficie de moldeo” utilizando tres bandas de calefacción y un voltaje controlable para simular la inyección de plástico a diferentes velocidades. El aumento de la entrada de calor corresponde a la aceleración del ciclo.
En nuestro laboratorio tenemos los medios para proporcionar flujo de refrigerante a diferentes temperaturas y caudales precisos. Utilizamos un sistema automatizado de adquisición de datos multicanal para registrar el flujo de refrigerante, la temperatura del refrigerante dentro y fuera y las temperaturas del acero en dos profundidades diferentes. Los datos se convierten automáticamente en una hoja de cálculo de Excel para permitir el estudio y la manipulación de los datos para la creación de gráficos y similares.
Nuestra primera serie de ensayos se realizó con un canal de enfriamiento limpio para establecer una línea base de rendimiento. La Figura 1 muestra la temperatura del acero vs la entrada de calor a una temperatura constante de refrigerante de 75°F (24°C) y un caudal de 1 GPM, muy por encima de la transición turbulenta. Recuerde que una mayor entrada de calor es lo mismo que acelerar el ciclo: más entrada de plástico por hora equivale a más BTU/h. Tenga en cuenta que incluso con una entrada de calor muy grande (2500 BTU / h), la temperatura del núcleo aumenta solo a aproximadamente 144°F (60°C).
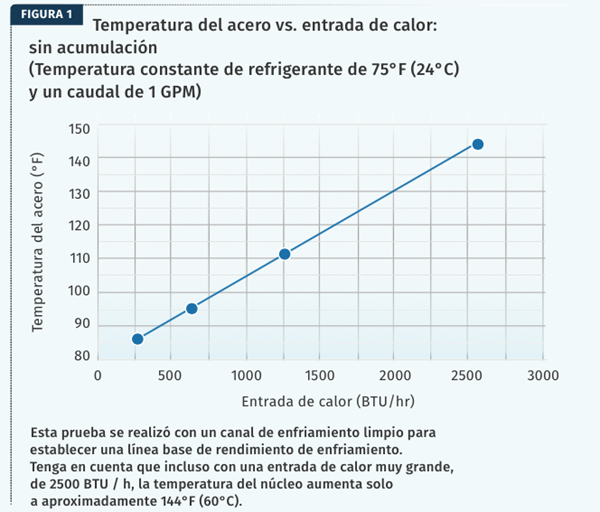
Para simular la acumulación de escamas en el canal de refrigeración, presionamos una camisa de acrílico en el diámetro interno del canal de refrigeración. El polímero acrílico tiene un coeficiente de transferencia de calor similar a los depósitos de calcio. Realizamos ensayos con dos espesores diferentes: 0,030 y 0,015 pulgadas.
La Figura 2 muestra la temperatura del acero frente al espesor del depósito en pulgadas. Usamos dos entradas de calor que están dentro del rango de las condiciones del molde del dispensador. Las condiciones de enfriamiento son las mismas que en la Figura 1.
Como comparación, calculamos la refrigeración real lograda en el lado B del molde del dispensador durante la producción, utilizando el caudal de refrigerante y el cambio en la temperatura del refrigerante que fluyen a través de los núcleos. El valor resultante fue de 1892 BTU / h para 4 núcleos o 473 BTU / h por núcleo. Con referencia a la Figura 1, podemos ver que con canales de refrigeración limpios las temperaturas del núcleo deben ser de aproximadamente 90°F (30°C).
La Figura 2 muestra que para un aporte de calor dado (tiempo de ciclo) las temperaturas del núcleo aumentarán a medida que aumente el espesor de la acumulación o depósito. Estas condiciones llevarán a temperaturas centrales excesivas y dificultad para producir piezas buenas. En este punto, las opciones son: reducir la entrada de calor (aumentar tiempo de ciclo) o restaurar los canales de enfriamiento a una condición limpia.
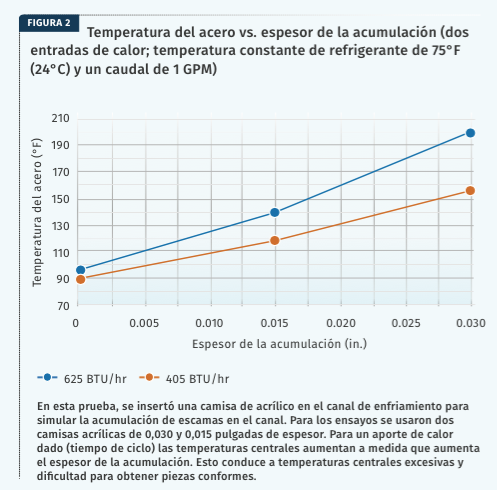
En nuestro curso de Enfriamiento Científico enseñamos sobre los efectos de la acumulación de escamas, y los estudiantes practican los cálculos que muestran la diferencia en la tasa de transferencia de calor entre los metales de construcción de moldes y las escamas de calcio. Pero el grado de deterioro del enfriamiento ilustrado por estos experimentos fue sorprendente.
Las lecciones aprendidas son claras. Establezca datos de rendimiento de referencia para el flujo de refrigerante y ΔT (cambio de temperatura) a través de los circuitos cuando el molde esté limpio. Los incrementos significativos en los valores de ΔT o la disminución del flujo para una presión dada del sistema indican problemas de enfriamiento o tal vez una obstrucción.
Dele a su sistema de agua de refrigeración la atención que se merece para que la química no funcione en su contra. Cree y use hojas de configuración y observe los cambios que se producen en cada lote de producción. Realice una limpieza mecánica o química periódica de los circuitos de refrigeración. Preste atención a estas cosas y "mantenga la calma".
Acerca del autor
Phil Burger, P.E., fundó Burger & Brown Engineering Inc. en 1978 y se desempeñó como presidente hasta 2005. Burger & Brown fabrica productos de ingeniería relacionados con el enfriamiento y sensores al interior de los moldes, además de poseer 10 patentes para sus productos. Burger actualmente trabaja medio tiempo para la firma y recientemente desarrolló un programa educativo llamado Scientific Cooling que se lanzó en octubre de 2013. Contacto: (816) 878-6675; pburger44@gmail.com; www.smartflow-usa.com.
Contenido relacionado
Inyección y sistemas de colada caliente en Meximold Tech Preview
Conéctese en línea, y sin costo, los próximos 9 y 10 de agosto para ver un adelanto de las tecnologías y nuevos desarrollos que se verán en Meximold sobre inyección de plásticos y sistemas de colada caliente.
Leer MásSimulación avanzada vs. tradicional en moldeo por inyección
Explore el impacto del moldeo virtual en la producción de plásticos. ¿Cómo anticipar defectos y adaptar procesos de inyección? Encuentre respuestas aquí.
Leer MásTratamientos químicos en sistemas de transferencia de calor
Entienda el riesgo de biofilmes y corrosión en sistemas de agua y cómo un tratamiento químico adecuado puede extender la vida útil de su equipo.
Leer MásDesafíos en la ventilación de moldes: velocidad de flujo y calidad
Descubra la ciencia detrás del sistema de venteo en el moldeado de plástico. Desde su funcionamiento básico hasta cómo el aire y el plástico interactúan para obtener piezas de calidad.
Leer MásLea a continuación
Moldes, de vuelta a lo básico: resortes de compresión
Algunos talleres de moldes insisten en que todos sus moldes tengan resortes para devolver las placas de expulsión. Afortunadamente, hay muchos para elegir. Este artículo se centra en los resortes de compresión para moldes de inyección.
Leer MásUna mirada seria a la refrigeración del molde
El enfriamiento es crucial para el proceso de inyección, pero frecuentemente se pasa por alto. Aquí hay algunas ideas a considerar.
Leer MásMoldeo por soplado: guía completa y preguntas frecuentes
¿Está interesado en el moldeo por soplado? Conozca las ventajas, desventajas y fundamentos de este proceso de transformación de plásticos.
Leer Más