Dónde y cómo ventilar los moldes de inyección
Cuestionamiento de varias “reglas generales” sobre la ventilación o venteo de moldes de inyección.
Venteos en el pozo frío
Una regla general sugiere ventilar el pozo frío opuesto al bebedero. A menos que le preocupe la posibilidad (casi inexistente) de obtener una marca de quemadura en el fondo del pozo frío, que podría remoler y reprocesar más tarde, no es necesario agregar un venteo allí. El “ajuste deslizante” entre el pin expulsor del pozo frío y su orificio es más que suficiente. Lo que puede hacer es cuestionar las reglas generales.
Venteos en la colada fría
Otra regla general sugiere que se debe agregar venteos a la colada en un molde de dos o tres placas. Eso parece tener sentido, debido a que a menudo hay mucho aire dentro de la misma y ayuda a expulsar la mayor cantidad posible para que no entre en la cavidad. Sin embargo, el aire, al igual que el plástico, toma el camino de menor resistencia. ¿Por qué querría pasar a través de un venteo de 0,0005 a 0,0020 pulgadas de profundidad, cuando puede fluir libremente a través de un canal que es 10, 20, incluso 50 veces más profundo?
La respuesta es que no lo hará, al menos hasta que el aire en todo el sistema (colada y cavidad) comience a comprimirse y acumule presión. Cuando la presión aumenta lo suficiente, es cuando los venteos en el canal se convierten en los caminos de menor resistencia. Se deben ubicar en donde se encuentre el frente de masa cuando la presión comienza a acumularse, cualquier venteo antes de esa posición es prácticamente inútil.
El volumen de aire es inversamente proporcional a la presión que se le aplica. Solo 150 psi de presión reducirán el volumen de aire en una cavidad en aproximadamente un factor de 10. Es por eso que lo más importante a considerar al tratar de decidir si necesita ventilar una colada o no, es la relación del volumen de aire en ella, dividido por el volumen total de aire en el molde (colada más todas las cavidades).
Muchos moldes tienen pequeñas coladas que alimentan solo una o dos partes grandes. Tienen una pequeña relación de volumen de aire, generalmente menos de 0.25. Ventilar cualquier parte de estos corredores es una pérdida de tiempo.
Otros moldes tienen grandes coladas, con varias ramas secundarias que alimentan numerosas piezas, como en un molde de ocho, 16 o 32 cavidades. Aquí es donde la relación de volumen de aire puede ser alta, aproximadamente 0,75 o más. Los venteos en estas coladas sí pueden ser beneficiosos.
Hay un truco efectivo para sacar una cantidad de aire significativamente mayor en un sistema de colada y es mecanizar una trampa de aire, como se
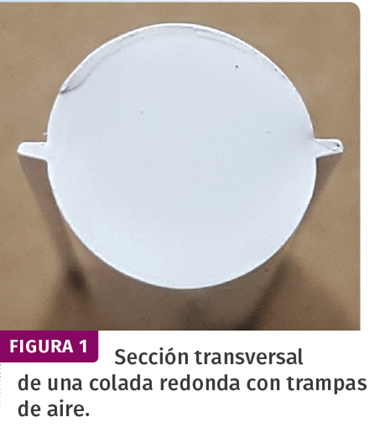
FIG 1. Sección transversal de una colada redonda con trampas de aire.
muestra en la Fig. 1. Las trampas de aire no solo ayudan a evitar daños en la línea de partición, sino que también son excelentes en la captura de aire. El material fundido fluirá primero por el centro del canal de la colada, dejando la mayor parte de la trampa vacía. Cuando la presión comienza a aumentar debido al aire comprimido o la resistencia del flujo de plástico hacia las cavidades, el material comenzará a meterse en la trampa. Si el frente de flujo no ha llegado al final de la trampa cuando la presión comienza a aumentar, el aire dentro de la trampa se comprimirá, lo que significa que se debe ventilar más volumen de aire rápidamente.
Los venteos para trampas de aire pueden ser mucho más profundos de lo que recomiendan los fabricantes, a menudo el doble o triple de su valor. Estos venteos más profundos tendrán ahora un camino de menor resistencia que los otros venteos en el molde. Las trampas de aire con venteos son tan efectivas en canales parabólicos y trapezoidales como en canales redondos.
Siempre que sea posible, trate de no ubicar un punto de inyección al final de la colada. Es preferible ubicarlo a un lado. Todos sabemos que es una buena idea hacer que una colada llene tenga espacios donde atrapar material frío en cada curva. La misma lógica se aplica al final de la colada. No es deseable que el material frío tape el punto de inyección o vaya directamente a la cavidad.
También querrás ventilar el final de la colada para sacar todo el aire posible, pero no demasiado cerca del punto de inyección, debido a que reduciría la cantidad de superficie crítica de contacto. El punto de inyección está sujeto a las mayores presiones en el molde. Es deseable maximizar el área de superficie alrededor del punto para garantizar un buen sellado y protegerlo del daño causado por las rebabas.
Idealmente, la colada debe estar perpendicular al punto de inyección, como se muestra en la Fig. 2. Extienda la colada más allá del punto en 1½ veces su diámetro, la longitud típica de una trampa de material frío. Ahora tiene una trampa para atrapar cualquier desecho en el frente de masa y puede agregar un venteo al final de la colada sin sacrificar la superficie de contacto cerca del punto de inyección.
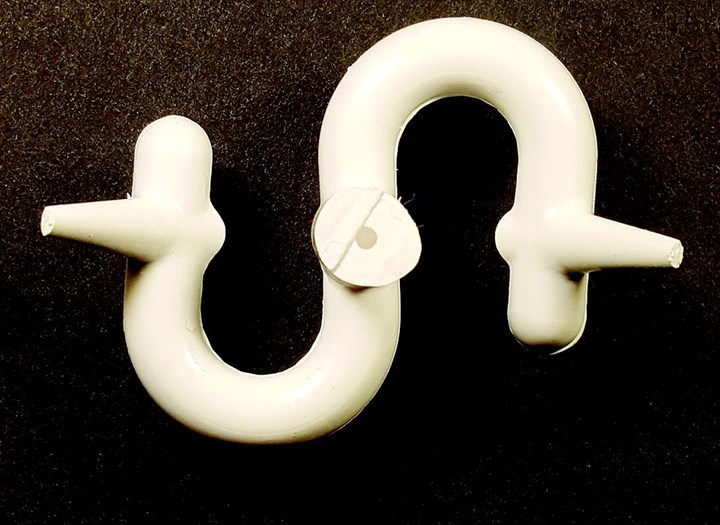
FIG 2. Es una buena práctica tener la colada perpendicular al punto de inyección.
Venteos al final del llenado
Hay otra regla general: "Siempre ubica venteos al final del llenado". Esa es una buena regla general, pero no la tome literalmente. Supongamos que tiene un molde que hace una simple probeta para de impacto por dardo. La práctica estándar es colocar un venteo en cada una de las dos esquinas opuestas al punto de inyección, los últimos lugares en llenar, como se muestra en la Fig. 3A.
Si observa de cerca el despeje del venteo en la Fig. 3A, puede ver que varía en longitud, más corta en el medio y más larga a medida que avanza hacia los bordes exteriores. Ese es un diseño realmente malo.
Si desea aumentar drásticamente la vida útil de los venteos en las esquinas, duplique la cantidad y colóquelos a aproximadamente 1/16 a ⅛ pulgada de distancia de las esquinas, como se muestra en la Fig. 3B. Si tiene en cuenta que el último volumen de aire atrapado en una cavidad generalmente está muy comprimido, extremadamente caliente y altamente saturado con volátiles corrosivos, este diseño ayudará a mitigar la erosión en los canales de venteo y el acero de la cavidad.
El mejor método de venteo para este tipo de pieza (Fig. 3C) es colocar un venteo a lo largo de todo el borde, pero justo por debajo de las esquinas. Esto da como resultado una cantidad mucho mayor de área de flujo de ventilación para que el aire comprimido escape, protegiendo a su vez las esquinas.
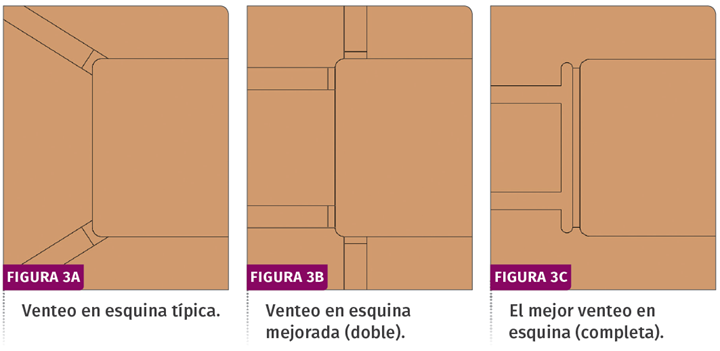
Venteo en esquina típica.
Las Figuras 3A, B, C representan diferentes ejemplos de venteos "puntuales", terminando con la Figura 3C que cuenta con unos venteos muy amplios. El siguiente tipo de venteos se llamada venteos continuos o periféricos. En pocas palabras, este tipo de ventilación funciona completamente, o casi completamente, alrededor de toda la parte. Si es una parte redonda, algunas personas llaman a esto un anillo de venteo. Si es una parte cuadrada, algunas personas lo llaman venteo perimetral. No importa si es redondo, cuadrado o cualquier forma imaginable.
Si el venteo corre alrededor del borde exterior de la pieza, es un venteo continuo. Si hay un pequeño espacio entre el cierre de la placa separadora y el núcleo, esto también es un venteo continuo. El propósito de los venteos continuos es maximizar el área de flujo de aire, lo cual es extremadamente importante si el proceso requiere un llenado muy rápido.
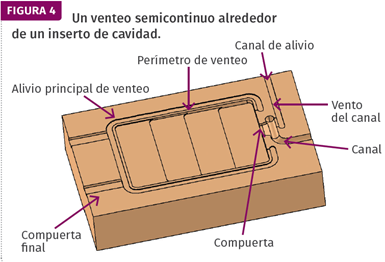
FIG 4. Un venteo semicontinuo alrededor de un inserto de cavidad.
La Figura 4 muestra un venteo continuo alrededor de la mayor parte de una cavidad para un molde simple. El único lugar donde no hay venteo es a ambos lados del punto de inyección. Si puede imaginar cómo fluye el material hacia la cavidad, o si realizó una simulación de flujo de molde, se daría cuenta de que las cuatro esquinas de la pieza son lugares donde el aire puede quedar atrapado, no solo las dos esquinas opuestas al punto de inyección.
Por eso es importante agregar venteos en las esquinas extremas de la entrada de material, así como enfrente. Además, observe cómo el extremo de la colada tiene una ventilación amplia y generosa a su lado, en lugar de un venteo estrecho al final.
Independiente del tipo de venteo que use, siga las pautas discutidas en el artículo del mes pasado, “Parte 2: Conceptos básicos sobre venteo en moldes”, especialmente aquellas sobre el rectificado y pulido de los venteos en la misma dirección del flujo de aire.
Una ubicación que con frecuencia tiene un problema de ventilación es la parte inferior de una costilla ciega u otro tipo de proyecciones independientes. Si una proyección es más de 1½ veces más profunda que gruesa, existe una buena posibilidad de que atrape el aire, lo que puede dificultar el llenado o causar que el aire atrapado se "gasifique" y deje una marca de quemado o efecto Diesel. Ese es un punto importante: no es la profundidad lo que causa los problemas, es la relación entre el espesor y la profundidad. Con las costillas, estos problemas empeoran cuando están situadas perpendiculares al flujo de material.
Una de las formas más comunes de ventilar una costilla profunda es instalar un inserto en el molde. El inserto forma una línea divisoria adyacente o preferiblemente en el medio de la costilla. Algunas personas llaman a esto un venteo "natural", que es una ranura creada por el espacio libre entre dos componentes del molde, como insertos de núcleo, levas, elevadores y pines expulsores.
Los insertos de molde se usan comúnmente para costillas profundas porque es mucho más fácil y menos costoso mecanizar y pulir un corte de costilla en el costado de un inserto que hacer una costilla ciega por EDM y luego pulirla para obtener un acabado fino después. Otra ventaja de incorporar un inserto de costilla es que elimina la posibilidad de que el núcleo se agriete en la parte inferior de la costilla.
Las costillas tienen mucha superficie y la presión de inyección intenta separar el acero como una espoleta en la cena de Acción de Gracias. Si el molde está sobreempacado, un inserto generalmente se alejará del núcleo un par de milésimas. Es por esta razón que la profundidad de los venteos en los insertos de molde debe estar en el lado bajo del valor recomendado.
A medida que el inserto "respira" durante la inyección, los venteos se hacen un poco más grandes. Sin embargo, puede agregar múltiples venteos, o ventilar todo el ancho del inserto al final de llenado para compensar la mayor profundidad.
Hay un inconveniente en tener una línea dividida a lo largo de una costilla: tratar de mantener limpios los venteos. Los venteos estáticos en la línea de partición son fáciles de limpiar en la inyectora. Los venteos estáticos en la parte inferior de una costilla profunda en un inserto generalmente requieren un desmontaje completo del molde.
Es por eso que algunas personas prefieren usar pines expulsores ventilados en la parte inferior de una costilla. Los pines expulsores son venteos dinámicos o "móviles". Se puede limpiar una buena parte de los pines con el molde aún en la máquina haciendo avanzar la placa expulsora completamente hacia adelante.
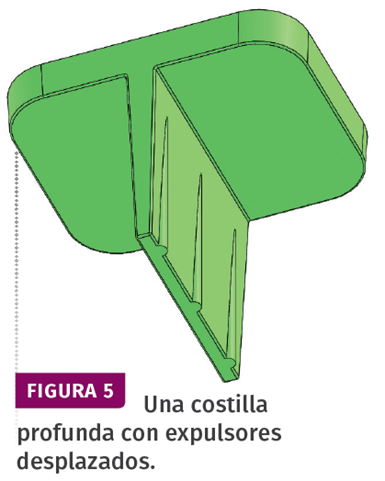
Los pines expulsores en la parte inferior de una costilla suelen ser una buena idea. Las costillas tienden a pegarse en el molde con una tremenda fuerza de sujeción. Los pines directamente debajo de las costillas son el mejor método para garantizar que las costillas se expulsen bajo diversas condiciones de moldeo.
Entonces, ¿cómo decide qué camino tomar: inserte el molde para mantener el costo bajo o mantenga el núcleo sólido y use pines expulsores para prolongar la operación del molde antes del mantenimiento? ¿Por qué no disfrutar de los beneficios de ambos métodos combinándolos, como se muestra en las Fig. 5 y 6?
La mayoría de los diseñadores suelen ubicar los pines expulsores en el centro
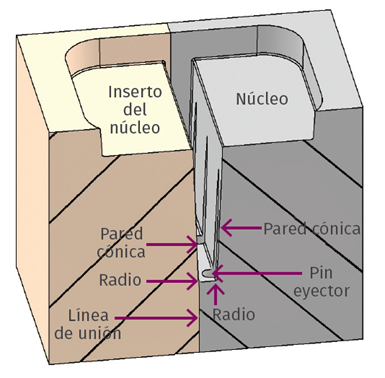
FIG 6. Un inserto en el núcleo para una costilla profunda con pines offset.
de una costilla. Eso está bien si la costilla está mecanizada en un sólido. Cuando se utiliza un inserto de molde, no puede colocar los pines expulsores el centro de la costilla, porque una parte del eje del pin estará en la línea de partición. Reducir el diámetro del pin expulsor es una mala solución. Los pines pequeños tienen la desagradable costumbre de desgastarse, bloquearse, doblarse y romperse. Si desfasa o mueve los pines, puede quedarse con un mayor diámetro. No invadirán la línea de partición y tiene una cantidad suficiente de acero entre el pin y el inserto.
Algunas personas se refieren a los pines expulsores ventilados como "autolimpiables". Al igual que los venteos fijos, no son auto limpiantes, simplemente eliminan obstrucciones grandes automáticamente. Cualquiera que haya limpiado el lodo o residuo de los pines ventilados mientras realiza un mantenimiento preventivo de rutina lo sabe muy bien.
Venteo en líneas de soldadura
En el libro Moldeo por inyección de plásticos de 1947, el difunto Dr. Islyn Thomas resumió la ubicación particular de los venteos mejor que nunca. Él dijo: “Ventile las cavidades en las líneas de soldadura o en los puntos de unión donde dos o más fuentes de material se unen y se fusionan en una masa sólida. La liberación de aire atrapado en esos casos permitirá un contacto íntimo entre las fuentes convergentes y dará como resultado una mayor resistencia y apariencia del artículo moldeado”. Eso fue hace 72 años y es absolutamente cierto hoy.
Las líneas de soldadura y las líneas de fusión están formadas por fuentes de masa fundida convergentes. Las causas más comunes de fuentes convergentes son: 1) Tener dos o más puntos de inyección por cavidad; 2) tener orificios en la parte por la que debe fluir el material; 3) tener espesores de pared variables o una ubicación del punto de inyección inadecuada que crea una condición de "desbalance o inestabilidad en el llenado".
Puede usar insertos de núcleo en cualquier lugar donde haya aire atrapado, como en el caso de fuentes de masa convergentes. Pueden ser cuadrados, redondos o de cualquier forma. Incluso un pin ventilado, ya sea estacionario o dinámico, es un tipo de inserto de núcleo cuando lo usa específicamente para dejar escapar el aire.
Cuando use un pin ventilado, no coloque el centro del pin en el centro de la ubicación del aire atrapado. Para lograr los mejores resultados, ubique un borde del pin en el centro donde confluye el aire. Cuando tiene dos o más puntos de inyección por cavidad, la ubicación del aire atrapado puede cambiar un poco, debido a las condiciones variables del proceso. Es posible que necesite usar un pin grande o múltiples pines para compensar esta variación.
Si puede tolerar una protuberancia pequeña en la parte inferior de la pieza, es mejor dejar el pin alrededor de ¼ pulgada o más por debajo de la superficie. Transforma una línea de soldadura débil en una línea de fusión más fuerte, porque el material continúa fluyendo hacia la protuberancia creada por el pin. Si este elemento interfiere con la función de la pieza, puede contornear el pin como un "Z-Puller" o retenedor para trampa de pozo frío. Dependiendo del tipo de material inyectado se puede quitar después de que se expulse la pieza.
Venteos en superficies de cierre
Si tiene una abertura en una parte, como en el caso de un marco de fotos, puede agregar respiraderos a la superficie de cierre central para evacuar el aire atrapado en los bordes internos de la parte. Los canales de alivio en estos venteos pueden ir a un orificio pasante perforado en el cierre. También puede usar este método de ventilación y alivio en las caras de levas y elevadores. En cualquier lugar donde haya contacto de acero sobre acero, generalmente existe la oportunidad de agregar un venteo.
Los venteos por lo general no necesitan tener un camino para que el aire escape a la atmósfera. En docenas de ocasiones, he usado venteos que expulsaban el aire en un bolsillo ciego. Por ejemplo, una vez tenía un pin de ½ pulgada de diámetro formando un orificio pasante en una parte gruesa. La corriente de material fluyó naturalmente alrededor del pin y convergió en el lado opuesto.
El venteo en el diámetro exterior del pin central hizo un buen trabajo expulsando la pequeña cantidad de aire atrapado en la parte inferior de la pieza, pero la parte superior de la pieza aún mostraba una marca ocasional de quemaduras. Perforé un agujero de 1/16 pulgadas de diámetro con una profundidad de ⅜ de pulgada en la cara del pin central, donde se cierra contra la cavidad. Se maquinó un venteo en la parte superior del pin, orientado en la dirección donde convergían las fuentes de masa.
El agujero ciego era lo suficientemente grande como para capturar la pequeña cantidad de aire atrapado. Cada vez que se abría el molde, se liberaba el aire comprimido dentro del pin. Los venteos ciegos son muy útiles cuando descubre un problema al ensayar un molde nuevo. Cuando no hay ningún lugar donde expulsar el aire debido a una línea de refrigeración, un elevador u otro obstáculo, es bueno tener un plan B.
Ventilación inversa
Incluso si no tiene un problema de llenado o efecto Diesel, ventilar las proyecciones independientes, ya sea en el lado central o en el lado de la cavidad, siempre es una buena idea. El aire realmente fluye a través de los venteos en ambas direcciones. Si bien el escenario más común es que el aire se escape de la cavidad durante la inyección para evitar problemas de llenado y quemado, los venteos también permiten que el aire ingrese a la cavidad durante la apertura y expulsión del molde.
Los venteos eliminan así una condición de vacío que puede causar que una parte o característica se adhiera a la cavidad o al núcleo. Esta condición de vacío a veces puede volverte loco. No solo puede salir el aire por el venteo, a menudo el aire viene cargado con acumulación de gases, dejando marcas de grasa en la parte inferior de la pieza.
Aún así, esta ventilación inversa puede permitir una apertura más rápida del molde, así como reducir la cantidad de fuerza requerida para expulsar la pieza. En casos extremos, puede alimentar aire comprimido a través de un venteo, tal como lo haría con una válvula de aire.
En los moldes de múltiples cavidades, no solo necesita ventilar cada cavidad exactamente igual, sino que también necesita ventilar cada colada de la misma manera. De lo contrario, puede causar una situación de llenado y empaque desequilibrado. Cuando todo esté dicho y hecho, asegúrese de actualizar los dibujos o planos del molde con las ubicaciones, y dimensiones finales. Con el tiempo, los venteos probablemente se desgastarán o colapsarán. Deberá reemplazarlos o volver a mecanizarlos a sus profundidades originales.
Acerca del autor
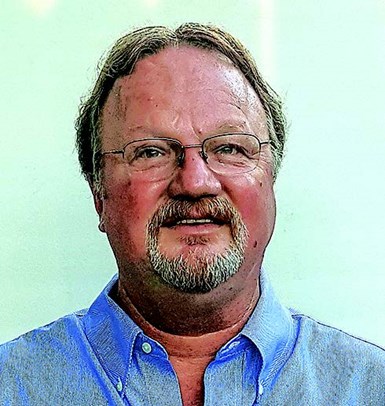
Jim Fattori
Jim Fattori es un moldeador de inyección de tercera generación con más de 40 años de experiencia en moldeo. Es el fundador de Injection Mold Consulting LLC, y también es ingeniero de proyectos para una gran moldeadora de múltiples plantas en Nueva Jersey. Contacto: jim@injectionmoldconsulting.com; injectionmoldconsulting.com.
Contenido relacionado
Meximold 2023: la vanguardia en moldeo de plásticos vuelve a Querétaro
Llegó la hora de vivir la experiencia más completa en todo lo relacionado con tecnologías para manufactura de moldes y transformación de plásticos. Meximold, en su cuarta edición, reunirá a los líderes de la industria de moldes, troqueles y herramentales en Querétaro. Regístrese sin costo y sea testigo de las últimas tendencias y equipos en moldes, troqueles y herramentales.
Leer MásFactores clave para estimar tiempo de ciclo en moldeo de plásticos
Descubra los 14 factores cruciales que influyen en la estimación del tiempo de ciclo en moldeo. Conozca un nuevo recurso gratuito que puede ser útil.
Leer MásAcoplamiento en moldeo: puntas de boquilla y manguitos de bebedero
Examinamos por qué un mal acoplamiento entre la punta y el manguito afecta el moldeo por inyección. Aquí veremos qué buscar y cómo solucionarlo.
Leer MásCompuertas de túnel para diseñadores de moldes
De todos los tipos de compuertas, las de túnel son las menos estudiadas. Esto es lo que necesita saber para elegir el mejor diseño para su aplicación.
Leer MásLea a continuación
Moldes: la verdad sobre los sistemas de expulsión guiada
Cuándo, dónde, cómo y por qué utilizar sistemas de expulsión guiada en sus moldes.
Leer MásTrucos del Intercambio en RTOs y RSOs
Cuanto más sepa sobre estos diversores y cierres de coladas, más los usará. Aquí le mostramos cómo ponerlos a trabajar en su molde.
Leer MásMoldes, de vuelta a lo básico: resortes de compresión
Algunos talleres de moldes insisten en que todos sus moldes tengan resortes para devolver las placas de expulsión. Afortunadamente, hay muchos para elegir. Este artículo se centra en los resortes de compresión para moldes de inyección.
Leer Más