La pared nominal en diseño de plásticos: claves para un moldeo exitoso
Entienda por qué la pared nominal es vital en la fase de diseño plástico y cómo la experiencia y FEA guían decisiones efectivas en ingeniería.
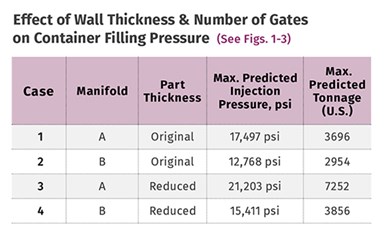
Efecto del grosor de la pared y el número de compuertas en la presión de llenado del contenedor
La mayoría de los ingenieros que han tratado con los plásticos ha escuchado que la primera regla de diseño es que la pieza debe mantener un espesor uniforme de la pared. Los principios de esta norma están profundamente enraizados en la fabricación. Pero con las tendencias actuales para aligerar y reducir el consumo material en los productos, los diseñadores toman a menudo decisiones con respecto a la pared nominal basándose únicamente en el rendimiento de la pieza.
Efectos de la pared nominal en la fabricación y diseño
No considerar los efectos de la pared nominal en el proceso de fabricación en la fase de diseño puede resultar en una ventana de procesamiento estrecha o en una incapacidad para la fabricación de la pieza a moldear. Cuando surgen estos problemas durante los ensayos iniciales del moldeo, la carga se coloca generalmente en el moldeador para que el producto funcione.
En este punto, las opciones para resolver los problemas muchas veces son limitadas, y la solución podría conducir a resultados no deseados cuando la pieza está en servicio
Importancia del análisis estructural de elementos finitos (FEA) en la toma de decisiones
Aunque la fabricación es importante, la decisión preliminar de establecer una pared nominal debe ser dictada por los requisitos de rendimiento funcional de la pieza. Si la pieza no funciona nadie la comprará.
Consideraciones como niveles aceptables de esfuerzo y vida útil esperada de la pieza deben ayudar a los diseñadores en la creación de la pared nominal. La experiencia previa y la interpretación correcta del análisis estructural de elementos finitos (FEA) han hecho que estas decisiones se tomen de manera más razonable durante las etapas preliminares de diseño.
Una vez que se ha establecido el espesor de pared mínimo para rendimiento, el pensamiento del diseñador debe centrarse en la fabricación. La discusión aquí se limita al moldeo por inyección. Debido a la naturaleza inherente del proceso, hay límites prácticos sobre cómo de delgadas pueden ser las paredes y aún fabricar la pieza.
La mayoría de las máquinas de inyección más convencionales pueden generar 20.000 a 30.000 psi de presión de plástico para llenar el molde. Como regla general, la presión necesaria para llenar debe ser 50-75% de la capacidad de la unidad de inyección. Esto permitirá un proceso de moldeado estable que puede acomodarse a cualquier variación natural que pueda surgir en el material plástico fundido.
Si el espesor seleccionado requiere demasiada presión para llenar el molde, el espesor de pared debe aumentarse, debe reducirse la longitud de flujo, el material debe ser cambiado o una combinación de estos tres factores. Una reacción instintiva a presiones excesivas es utilizar un material que fluya más fácilmente.
Por lo general, estos materiales de fácil flujo tienen un menor peso molecular promedio, lo que reduce la viscosidad efectiva de la resina. Aunque esto puede tener buenos resultados, debe hacerse un enfoque holístico para ver cómo el cambio en el material afectará el rendimiento del producto a corto y largo plazo.
A menudo esto requiere algo más que mirar una hoja de datos. Un enfoque alternativo a la reducción de la presión de inyección, mientras se mantiene la pared nominal deseada, se centra en la reubicación de la entrada o en agregar entradas adicionales para reducir la longitud de flujo.
Desafíos y soluciones en el moldeo por inyección: cómo evaluar la moldeabilidad
La simulación en moldeo por inyección puede utilizarse para determinar la factibilidad de la fabricación de una pieza en un espesor de pared determinado. La simulación permite al diseñador representar los efectos de los tres factores (viscosidad del material, espesor de la pieza y longitud de flujo) en el proceso y proporciona una predicción de presión de inyección máxima y tonelaje de la fuerza de cierre requerido para la fabricación de la pieza. Esta información ayuda a determinar el tamaño de la máquina que se necesita.
Si la presión o tonelaje previstos superan la capacidad de la máquina, un analista puede ajustar uno de los tres parámetros para evaluar cómo cambiarían los parámetros del proceso y si va a aumentar la ventana de procesamiento de la pieza.
Al incorporar la simulación en la evaluación de diseño, estas decisiones se pueden tomar al inicio del proceso de diseño y pueden ayudar al diseñador a juzgar si el procesamiento afectará el rendimiento de la pieza.
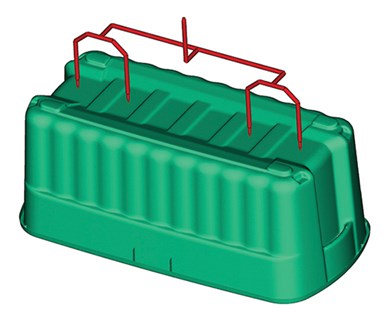
El distribuidor A utiliza cuatro entradas de inyección para llenar la pieza y todas las entradas están situadas en la línea central de la pieza.
La figura 1 muestra un envase que estaba pasando por una revisión de diseño con el fin de minimizar el consumo de material, reduciendo el espesor de la pared.
El objetivo del proyecto era poder fabricar el envase en la máquina del mismo tamaño, pero reduciendo el espesor de pared en un 10%. El envase iba a llenarse con cuatro puntos de entrada situadas a lo largo de la línea central del envase (Distribuidor A). Se realizó una serie de simulaciones de la línea de base para determinar, como estaba previsto, el cambio del proceso como consecuencia de la reducción del espesor de la pared.
El análisis reveló que reduciendo el espesor de la pared en 10%, aumentaría la presión de inyección prevista en un 21% y el tonelaje previsto en un 100% (ver tabla). Esto dio lugar a un proceso de presión y tonelaje limitado y habría requerido una prensa más grande para moldear las piezas.
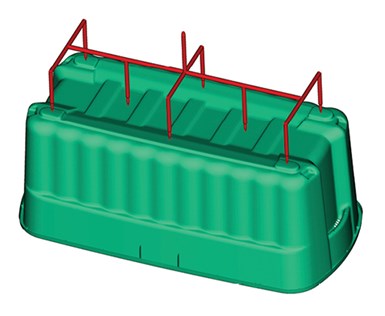
El distribuidor B incrementa el número de entradas y las acerca a los laterales del contenedor para reducir la longitud de flujo.
Por lo tanto, se determinó que la reducción del espesor de la pared no era posible con el actual diseño de molde. El cliente no quería cambiar el material, se modificó el distribuidor y se incrementó el número de puntos de entrada de cuatro a ocho (Distribuidor B), como se muestra en la figura 2.
Aumentar el número de entradas y colocar las entradas más lejos (más cerca de las paredes laterales) redujo la longitud del flujo del material en la cavidad.
Las simulaciones revelaron que el nuevo diseño de distribuidor reduciría de hecho la presión de inyección necesaria y sólo aumentaría la fuerza de cierre prevista en un 4%. Este distribuidor modificado permitió que se lograra la reducción de la pared sin necesidad de cambiar a una prensa más grande.
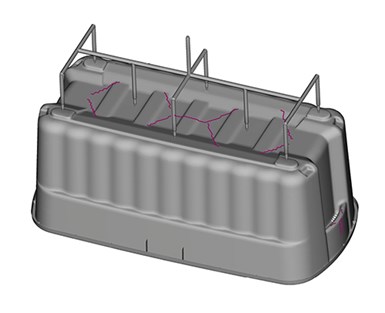
Incrementando el número de puntos de entrada con el distribuidor B, el número de líneas de soldadura se incrementan en la base del contenedor.
La simulación también permitió al diseñador identificar la ubicación y el número de líneas de soldadura para determinar cómo influyen en el rendimiento de la pieza, como se muestra en la figura 3.
¿Por qué mantener un espesor de pared uniforme?
Una vez establecido el espesor nominal de pared, es importante que el espesor de la pared permanezca lo más consistente posible. Mantener un espesor uniforme permite el flujo más uniforme del plástico a través de la pieza y permite el mejor procesamiento posible.
Ya que el moldeo por inyección es un proceso impulsado por la presión, el polímero fundido tomará la trayectoria de menor resistencia. Esto significa que cuando hay que hacer una variación en el espesor de pared, el plástico preferentemente fluirá a través de la pared más gruesas. Este flujo preferencial puede provocar patrones de llenado desequilibrado, aire atrapado o formación de líneas de soldadura.
Además, los plásticos son inherentemente malos conductores del calor, así que manteniendo un espesor uniforme de la pared de la pieza se refrescará tan uniformemente como sea posible.
Esto también significa que, si se llena correctamente, la pieza debe encoger lo más uniformemente posible y minimizar los esfuerzos residuales en la pieza moldeada. La siguiente ecuación muestra que el tiempo de enfriamiento de una pieza de plástico es directamente proporcional al cuadrado del espesor de la pared:
t.enfriamiento ∞ espesorpieza2
Densidad
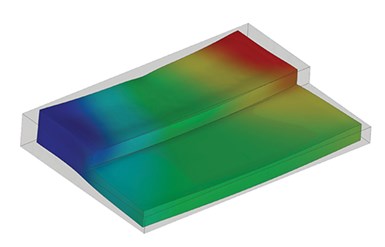
La variación en el espesor de la pared de la pieza de plástico produce contracción no uniforme que puede resultar en una deformación excesiva.
Por lo tanto, si una pared de 2 mm tendrá 1,76 segundos para enfriarse, una pared de 4 mm tendrá aproximadamente 7 segundos. Si estas dos secciones de pared se colocan adyacentes una a otra, la pared de 4 mm tendrá que reducir significativamente más que la pared de 2 mm, como se muestra en la figura 4.
Como resultado de esta contracción diferencial, se desarrolla un esfuerzo que la pieza quiere aliviar en la eyección, y la pieza entonces puede exhibir una deformación excesiva. Si el diseño requiere que ciertas áreas tengan un desempeño más rígido que otras, hay mejores opciones que simplemente aumentar el espesor de la pared.
La adición de las reforzamientos o la evaluación de la pared de la pieza para lograr una pieza más rígida, manteniendo uniforme el espesor de pared, permitirán mejores resultados que el aumento selectivo del espesor de pared de la pieza. Sin embargo, las dimensiones de estas características todavía son dictadas por la pared con la que se intersectan.
Reducir el espesor de la pared en el diseño de envases y su impacto en la fabricación
Las aplicaciones actuales para las piezas muchas veces hacen difícil mantener una pared nominal constante. Además, las exigencias contradictorias de fabricación y función de la pieza no siempre se alinean para permitir la construcción óptima del molde.
Aquí, puede ser necesaria una variación localizada del espesor de pared para obtener el patrón de llenado deseado o el desempeño de la pieza. Los requerimientos de fabricación puede ser el resultado de un patrón de llenado desequilibrado, aparición no ideal de una línea de soldadura, aire atrapado o deformación excesiva.
Sea cual sea la razón, establecer una pared nominal será una guía para que el diseñador sepa cómo puede ser alterado el espesor de la pieza. Cuando se requiere una variación en el espesor de la pared, se deben seguir estas pautas:
- Haga una transición gradual de espesor. Como se mostró en la sección anterior, las transiciones abruptas del espesor pueden conducir a variaciones en la contracción y a un alto esfuerzo residual en la pieza moldeada. Esto puede generar deformaciones excesivas o resistencia reducida.
- Minimizar la variación en el espesor de la pared a 25% en resinas amorfas y menos del 15% para resinas semicristalinas. Las tasas más bajas de la contracción de las resinas amorfas permiten una mayor variación.
- Coloque la entrada en la región más gruesa de la pieza. Localizar la entrada en la sección de pared más gruesa permitirá que las áreas más gruesas se llenen mejor y permitirá mayor control sobre la etapa de llenado, que puede ayudar a minimizar la formación de vacíos o rechupes.
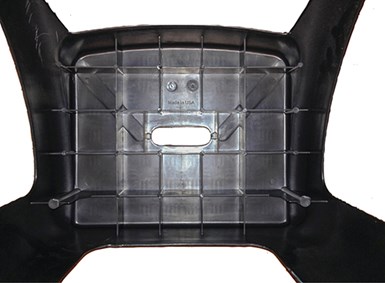
La imagen muestra la incorporación de un líder de flujo (incremento localizado del espesor) para ayudar al moldeo de la pieza de plástico.
La configuración de una pared nominal es una de las decisiones más importantes que toma un ingeniero cuando diseña una pieza de plástico que va a ser moldeada por inyección.
La pared nominal influye en las dimensiones generales de la pieza, el rendimiento de la pieza y los requisitos de fabricación. Los diseñadores deben adoptar un enfoque integral sobre cómo reducir el grosor de la pared de la pieza antes de tomar decisiones.
Entender cómo los cambios de diseño tendrán impacto en el proceso de fabricación es esencial para asegurar que la pieza tenga el desempeño esperado.
Sobre el autor
Erik Foltz
Es ingeniero, gerente senior en The Madison Group, una firma independiente de ingeniería y consultoría en plásticos, con sede en Madison, Wisconsin. Es un consultor profesional certificado de Moldflow y es usuario beta de la línea de productos Autodesk de Moldflow Insight Plastic. Teléfono de contacto: (608) 231-1907; erik@madisongroup.com, madisongroup.com
Contenido relacionado
Cálculo preciso del volumen en máquinas de moldeo por inyección
Descubra la importancia de calcular el volumen de inyección y cómo garantizar que su cilindro tenga la capacidad adecuada. Evite errores comunes en el moldeo por inyección.
Leer MásDiez consejos para recortar los ciclos de moldeo de preformas PET
Descubra cómo mejorar los tiempos de ciclo en moldeo por inyección centrándose en técnicas eficientes de enfriamiento, especialmente para preformas gruesas.
Leer MásPuntas de boquilla: impacto y selección en moldeo por inyección
Descubra la relevancia de las puntas de boquilla en moldeo por inyección. Aprenda sobre tipos comunes, problemas y técnicas de reemplazo.
Leer MásClaves para seleccionar el cañón correcto en inyección de plásticos
Análisis técnico sobre la elección del cañón de plastificación. Conozca las ventajas de utilizar dos cilindros y cómo maximizar la eficiencia en el moldeo.
Leer MásLea a continuación
Moldeo por inyección robusto: temperatura, tiempo y presión
Entienda los elementos críticos del moldeo por inyección robusto y cómo mejorar la eficiencia del proceso, incluyendo viscosidad, balance de cavidades y más.
Leer MásFuerza de cierre en moldeo por inyección: ¿Por qué es crucial?
Conocer en detalle los parámetros del material, la máquina y del molde es la base para un proceso de moldeo por inyección fluido. La carencia de conocimiento en alguno de estos tres elementos afectará al proceso de inyección, y por consiguiente la calidad del producto.
Leer MásEconomía circular de los plásticos en la realidad comercial
Estas son algunas tecnologías, ya disponibles en el mercado, que buscan ayudar a mejorar e implementar la circularidad de los plásticos.
Leer Más