PepsiCo y su embotelladora en México redujeron peso de botellas
PepsiCo, junto con su embotellador en México GEPP, logró la reducción de 6g de peso en sus botellas de PET. Este resultado, revelado hace algunos meses, ha sido catalogado como un gran logro.
Compartir
Lea a continuación
Con el sistema de control automatizado de moldeo por soplado Process Pilot, de Agr, acoplado a una máquina de moldeo por soplado Sidel SBO 16 Universal, el productor mexicano de bebidas GEPP ha reducido el peso de su botella de PET de 2L con baja carbonatación de 52g 46g. Con velocidades de operación de la máquina de moldeo por soplado de 24,000 botellas por hora, la reducción de seis gramos ahorra a la empresa aproximadamente siete toneladas de resina en cada producción de 48 horas.
Esta impresionante disminución de peso se ha logrado con condiciones ambientales cambiantes que añaden un extra de complejidad al proceso de moldeo por soplado. A pesar de los cambios de temperatura de 40 grados o más durante el día, la línea 1 en la planta de GEPP, en Hermosillo, Estado de Sonora, al noroeste de México, produce botellas de PET que alcanzan constantemente el nuevo objetivo de reducción de peso durante todo el día de operación.
La exitosa reducción de peso exige un cumplimiento riguroso de la receta de distribución del material desarrollado para el tipo de botella. Algo que es mucho más difícil de hacer cuando se trabaja con menos material, observa Jesús López, gerente técnico corporativo de GEPP.
Con la introducción de un nuevo nivel de control en el soplado de botellas, el sistema Agr proporciona la precisión necesaria para compensar el efecto de las temperaturas fluctuantes de Hermosillo. Como explica López, "nadie quiere poner la misma cantidad de calor en una preforma de 90 grados que una preforma de 70 grados."
Los sensores de alta precisión de Pilot, desplegados en la zona de retirada de la máquina de moldeo por soplado, miden el espesor de cada botella en intervalos de 12,5 mm a lo largo de la pared lateral. Los algoritmos propietarios de AGR analizan instantáneamente las mediciones y las comparan con la receta. Si la distribución de material empieza a mostrar una tendencia a salirse de las especificaciones, el sistema Pilot ajusta el control de la función de la máquina de moldeo por soplado apropiado modifica, por ejemplo, la temperatura de configuración antes del soplado o de las lámparas para mantener la producción constante. Eliminando la necesidad de una intervención manual, que es con frecuencia una práctica imprecisa, incluso para los operadores calificados; Este ajuste automático asegura que la cantidad correcta de resina se distribuye a la zona correcta de la botella, independientemente de las condiciones ambientales.
Además del impacto de un menor consumo de material, el sistema Agr ha permitido a GEPP, embotellador exclusivo de bebidas de marcas de PepsiCo en México, lograr otros aumentos importantes de productividad, especialmente cuando se trata de cambios. La línea 1 de Hermosillo produce una mezcla de botellas con carbonatación nula, baja o alta para seis productos diferentes: PepsiT, 7UP, Mirinda (una soda con sabor a naranja), Manzanita Sol (sabor manzana), Limonada (limón) y Epura (agua)-en varios tamaños: 600mL, 1L, 1.5 L, 2 L, 2.5 L y 3 L.
El cambio de un envase a otro solía tomar un promedio de dos horas, cerca 1.5 horas para reemplazar los moldes en la máquina de moldeo por soplado de 16 estaciones, y luego otra media hora para controles de verificación de proceso y de calidad. Ahora, con la instalación de Process Pilot, la máquina de moldeo por soplado produce las botellas de manera correcta desde la puesta en marcha, sin necesidad de muestreo y ajustes, haciendo cada cambio 25% más rápido, mientras que también se ahorran 6.000 botellas de desecho.
Los beneficios de una producción sólida de botellas también aparecen más adelante en la planta integrada de fabricación y llenado de botellas. López asegura que hay mucho menos interrupciones en los procesos de etiquetado, puesta de tapones y embalaje, debido a la presencia de botellas que no se justan a las especificaciones. En las ocasiones poco frecuentes en que se producen interrupciones, "Pilot retoma el proceso dos a tres veces más rápido," dice.
López, que posee gran experiencia en embotellado y estuvo muy involucrado en la transición de GEPP de vidrio a PET a mediado de los años noventa, es responsable de todas las operaciones PET en las 25 plantas de la empresa. Hermosillo, con su larga historia y su talentoso equipo, es la primera planta en montar una iniciativa de reducción de peso, junto con el Process Pilot.
El éxito de este esfuerzo, en conjunto con puestas en marcha más rápidas de la máquina de moldeo por soplado, cambios más cortos, rápida recuperación de las interrupciones y reducción de desechos, ha generado un atractivo retorno de la inversión, no sólo en el envase de 2 L, sino también en otros tamaños y tipos. Más aún, esto le da a GEPP la confianza de una mejor calidad de la botella, que para López es una consideración "primordial".
De cara al futuro, a López le gustaría "estandarizar lo más posible los equipos y el proceso." Es partidario de la visión de instalar el sistema en la segunda línea de soplado en Hermosillo y el establecer la planta como el sitio de entrenamiento para todas las operaciones de moldeado por soplado de GEPP en todo el país.
"Process Pilot gestiona la manera en que la máquina de moldeo por soplado hace la botella por lo que siempre tenemos el mismo resultado", concluye López.
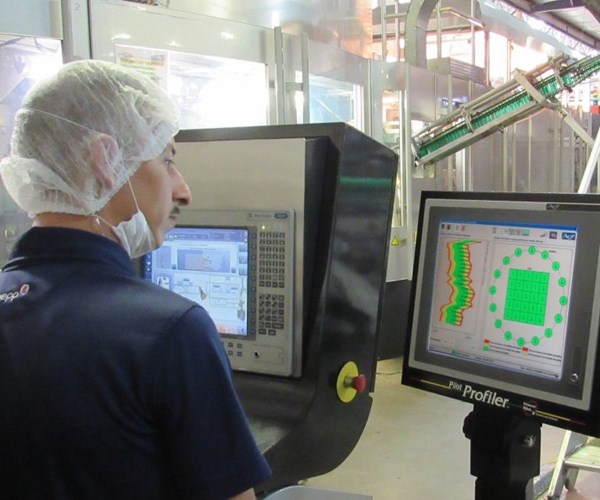
Contenido relacionado
Transición hacia la economía circular en México: beneficios del PET
La nueva Ley General de Economía Circular de México exige que las empresas registren un plan de economía circular, aumenten el porcentaje de contenido reciclado y logren cero desperdicios. En este contexto, el PET es una solución eficiente y sustentable para cumplir con la regulación.
Leer MásTereftalato de polietileno (PET): procesamiento, reciclaje y futuro
El PET (tereftalato de polietileno) es un polímero termoplástico que se caracteriza por su resistencia, claridad y ligereza. Es esencial en diversas aplicaciones gracias a su versatilidad, durabilidad y reciclabilidad. En este artículo, exploramos la historia, las propiedades, la producción, las aplicaciones y el futuro de este material esencial.
Leer MásDiez consejos para recortar los ciclos de moldeo de preformas PET
Descubra cómo mejorar los tiempos de ciclo en moldeo por inyección centrándose en técnicas eficientes de enfriamiento, especialmente para preformas gruesas.
Leer MásCinco problemas en el moldeo por soplado de botellas de plástico PET
Lea aquí una guía rápida para resolver cinco problemas recurrentes en el procesamiento de botellas de PET. Cómo lograr la mejor distribución de la pared en una botella PET y otras soluciones para obtener envases más resistentes y duraderos.
Leer MásLea a continuación
Innovación en empaques de pared delgada: tecnología y sostenibilidad
El mercado global de envases de pared delgada está en constante evolución y abarca una amplia gama de aplicaciones y materiales. En el presente artículo exploraremos este mercado, su crecimiento, tendencias emergentes, impacto de la pandemia por COVID-19 y sus proyecciones para los próximos años según un reciente estudio publicado por Mordor Intelligence.
Leer MásClasificaciones de moldes de inyección de plásticos: análisis detallado
Examine los factores que influyen en la durabilidad de los moldes de inyección. Desde la complejidad del diseño hasta la selección de materiales, aprenda cómo optimizar la vida útil de los moldes.
Leer MásOportunidades de la Industria 4.0 para la nueva normalidad en México
La pandemia ha generado graves afectaciones en diversas actividades y sectores económicos de todo el mundo. Sin embargo, detrás de esos problemas llegaron grandes oportunidades, como la adopción acelerada de la digitalización y la diversificación del portafolio de muchas empresas. Aquí la Industria 4.0 tiene mucho que ofrecer.
Leer Más