Extrusión: mantenga su cambiador de mallas en funcionamiento
Descubra los distintos diseños de cambiadores de mallas y elija el más adecuado para su aplicación de filtración en procesos de extrusión.
Elección de diseños de cambiadores de mallas
Hay muchos diseños diferentes de cambiadores de mallas en el mercado hoy en día, desde placas deslizantes manuales hasta diseños de presión constante y flujo reverso continuo, cada uno viene con sus fortalezas y debilidades. Como procesador, necesita saber esto con el fin de hacer la mejor elección de cambiador de malla para su aplicación en particular.
Este artículo se centrará más en la solución general de problemas proceso en lugar de temas específicos de la máquina, pero es importante tener en cuenta que un gran porcentaje de los problemas que los procesadores de extrusión tienen con sus cambiadores de mallas se producen debido a que el cambiador que está utilizando no es el mejor diseño para su aplicación. Cada aplicación específica de filtración de extrusión debe ser examinada de cerca antes de especificar un cambiador de malla para el proyecto.
Malla de filtración
Cada procesador quiere la mejor filtración que pueda conseguir para el área de filtración que tiene. Muy pocos, sin embargo, utilizan una configuración de paquete de mallas totalmente optimizado para su proceso.
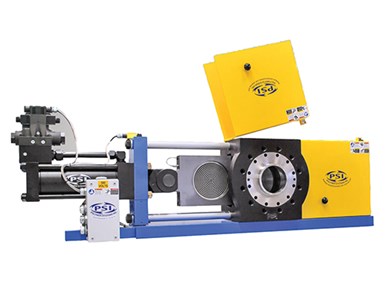
Una forma de minimizar las fugas en los cambiadores de mallas de placa deslizante es aumentar la presión. Mientras que puede sonar contrario a la intuición, porque los sellos están diseñados para responder a la presión en la extrusora, sólo están trabajando en su mejor momento cuando la presión es mayor.
Tomemos como ejemplo una situación en la que un operador está tratando de extender una producción entre los cambios de mallas. A medida que la malla se va obstruyendo, la presión se eleva y con el tiempo hace que la tela de alambre falle. Una solución simple es operador a acumular mallas 20 adicionales para una mayor resistencia.
Una mejor solución sería aumentar la fuerza de soporte de la malla base, usando una malla 10 de mayor calibre en capas con una sola malla 20. Las mallas 10 y 20 se apoyan mutuamente, trabajando en dos niveles.
El resultado final es la capacidad de correr más tiempo entre cambios, pero sin la caída de presión innecesariamente alta y el aumento resultante en el calor de cizallamiento. Es mejor evitar cualquier aumento en cizalladura inducida por la presión, ya que esto generará temperatura de fundido más alta en el extremo de descarga de la extrusora, creando una mayor demanda de capacidad de refrigeración aguas abajo y potencialmente reduciendo la productividad.
La mayoría de los proveedores de cambiadores de mallas ofrecen servicios de apoyo en proceso que incluyen cálculos de caída de presión. Estos son fáciles de realizar y tienen influencia en las viscosidades de los materiales, el plato rompedor de área abierta y el área abierta de mallas para llegar a la mejor configuración del paquete de filtros para el entorno de procesos y operaciones. Este servicio es normalmente un medio sencillo y gratuito para optimizar el rendimiento del flujo de polímero.
Control de temperatura
Otro inconveniente atribuido en ocasiones a los cambiadores de mallas es la fluctuación de la temperatura. La mejor práctica es permanecer alerta a los indicadores, calentadores y circuitos de calefacción. El monitoreo de estos en el cambiador de mallas puede no ser tan crítico como la comprobación en el tornillo extrusor y la alimentación, pero puede ayudar a detectar un problema antes de que sea catastrófico.
Otro consejo es optimizar el número de zonas de calor necesarias para equilibrar la temperatura a través del cambiador de mallas. Más específicamente:
- Los cambiadores hidráulicos de placa deslizante se sirven mejor con tres zonas, una zona central y zonas independientes para la cada extremo de la placa deslizante. Muchos procesadores cablean estas máquinas en una sola zona de control, resultando en demasiado o muy poco calor a la placa deslizante. Esto puede desestabilizar el perfil de fusión y causar material en llamas en la placa rompedora.
- Los cambiadores de malla continuos de tipo perno normalmente se sirven mejor con una única zona de control, pero a medida que estas máquinas aumentan de tamaño, las zonas adicionales ayudan a equilibrar el calor. Los cambiadores de malla continuos de tipo perno calientan los tornillos por conducción desde el cuerpo. Si el calor no es equilibrado, el cuerpo puede reducir el tamaño en el perno y generar fuerzas de sujeción suficientemente altas para evitar el movimiento del perno.
- Los adaptadores de máquina también sirven mejor normalmente con control de temperatura independiente. Esto, sin embargo, variará con el tamaño.
Fluctuación en la presión
Restringir el flujo de polímero a través del cambiador de malla también afectará a la estabilidad del proceso. Para materiales sensibles o aquellos con características de flujo únicas, el software de modelado CFD (dinámica de fluidos computacional) se puede utilizar para optimizar pasos de flujo en el cambiador de malla y minimizar el tiempo de residencia del material.
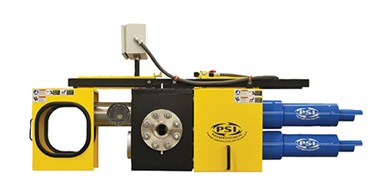
Los cambiadores de mallas continuos que no utilizan sello mecánico utilizan piezas mecanizadas de forma precisa para efectuar un sello de polímero. Estas mismas piezas proporcionan lubricación entre los tornillos o la rueda y la estructura y deben mantenerse para evitar el bloqueo de las máquinas.
En esta línea, la longitud del adaptador, etapas y transiciones, y el inventario de polímero entre la punta del tornillo y el paquete de la malla puede ser fundamental para establecer un mejor flujo y reducir al mínimo los puntos de degradación del polímero y la estratificación térmica.
Los ciclos de venteo en los cambiadores de malla continuos pueden influir en la estabilidad de la presión. La mayoría de los cambiadores de tipo perno pueden ver reducida hasta el 50% del área de filtro disponible del proceso por cambio de malla. Mientras que esto provoca naturalmente un aumento de la presión, el caudal y la presión en el dado normalmente permanecer relativamente estables. El problema surge con la reintroducción de la malla limpia.
Los venteos mecanizadas en los pernos desvían una pequeña porción de la masa fundida de polímero para llenar previamente y purgar el aire de la malla que ingresa. La ligera caída resultante en la presión del dado puede ser minimizada por el operador o de forma más precisa por el control PLC.
Los cambiadores de presión constante, como los de diseños de ruedas giratorias, no están normalmente sujetos a estas cuestiones. Un auxiliar que puede ayudar enormemente con la presión fluctuante es una bomba de engranajes, que puede tolerar las oscilaciones de presión aguas arriba mientras sostiene la presión del dado estable.
Gestión de fugas en los cambiadores de mallas
Las fugas son un problema con casi todos los diseños de cambiador de malla a medida que envejecen, pero más notablemente con los modelos de deslizamiento de la placa. Este tipo de cambiador de pantalla se basa en sellos activadas manualmente o con presión y están sujetos a desgaste por el movimiento de la placa deslizante, la degradación del anillo de estanqueidad a presión, y el daño de las mallas desalojadas.
El mantenimiento del sello para estas máquinas puede ser necesario con tanta frecuencia como semanalmente o una vez al año. El mantenimiento puede conducir a desmontaje y ensamble, que puede ser un proceso costoso que consume tiempo. Incluso antes de que alcance este punto, el esfuerzo necesario para mantener la placa deslizante limpia y prevenir el escape de polímero en el cableado y otros equipos, es significativo.
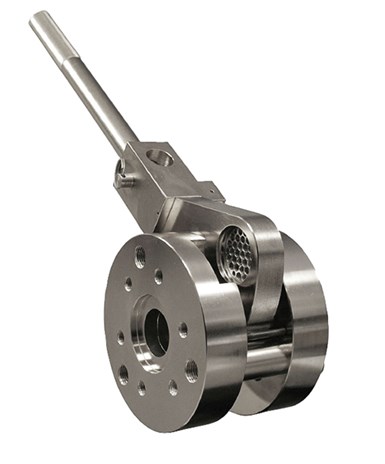
Los cambiadores manuales proporcionan filtración rentable para la extrusión. Los cambios se simplifican y el tiempo de inactividad se reduce debido a que el diseño permite que el tornillo de la extrusora sea halado a través del cambiador de mallas.
Una forma de minimizar las fugas en un sistema como este es aumentar la presión. Su intuición le puede decir que presión más baja sería mejor porque pondría menos presión en el sistema. Sin embargo, debido a que los sellos están diseñados para responder a la presión en la extrusora, solamente están trabajando en su mejor momento cuando la presión es mayor.
A una presión más baja, los sellos se relajan un poco. Cuando la extrusora está inactiva o funcionando a velocidad baja y se ejerce muy poca presión sobre el sello, se hace fácil que el material de viscosidad más baja se escape hacia fuera.
Un nuevo sello de placa deslizable, todo en acero, con diseño de anillo de presión segmentado, aborda estos problemas y otorga una garantía libre de fugas de por vida, independientemente de la temperatura y baja viscosidad, por lo que este sello el primero en operar sin fugas aen plicaciones de recubrimiento de alta temperatura.
Las fugas de material en cambiadores tipo perno o otras máquinas de ruedas giratoria que operan sin un sello mecánico pueden así mismo ocurrir con el tiempo; pero con estos diseños, la fuga casi siempre es causada el daño mecánico. Estos cambiadores mecanizados con precisión están diseñados normalmente para un rango de viscosidad del material bastante estrecho.
No se debe aplicar una máquina diseñada con espacios libres para alta presión y alta viscosidad a un proceso de baja viscosidad sin la aprobación o modificación del proveedor.
Contaminación de resina y degradación
El propósito principal de un cambiador de malla es filtrar los contaminantes de la corriente de masa fundida; pero el hecho es que los cambios de malla introducen casi inevitablemente contaminantes, algunos de los cuales entran en el dado. Estos son el resultado de la limpieza imperfecta de la placa deslizante, el perno, o la rueda. Por ejemplo:
• Esto puede ocurrir en un cambiador de malla de placa deslizante cuando los sellos de entrada y salida raspan residuo de material en ambos lados del paquete de mallas que se ingresa. Los contaminantes aguas arriba son atrapados en la malla. Los contaminantes aguas abajo pasan dentro del dado.
• Un cambiador de malla de presión constante puede experimentar esto también, pero en un grado mucho menor. La brecha entre el perno o la rueda y la carcasa se mide en micras en el lado aguas abajo. El contaminante que pueda pasar a través de este espacio libre entra en el flujo de fundido sólo tiene consecuencias en las aplicaciones más exigentes, y por estas pocas ocasiones, los filtros secundarios capturan todo lo que viene a través.
Muchos procesos no tienen que correr continuamente o requieren 100% de calidad y pueden pasar por alto los contaminantes durante el cambio de malla. Sin embargo, si su cliente tiene tolerancia cero, necesitará un tipo diferente de cambiador de malla. No hay manera de seguir utilizando un cambiador de malla de placa deslizante sin introducir algún nivel de contaminación o degradación del material en la placa rompedora fuera de línea. Para resolver esto, un cambiador continuo tipo perno o de rueda giratoria es una mejor solución.
Lock-up (perno o rueda atascada)
Los cambiadores de pantalla continuos que no utilizan sello mecánico utilizan partes mecanizadas de forma precisa para efectuar un sello de polímero. Estas mismas partes proporcionan lubricación entre los tornillos o la rueda y la carcasa y deben mantenerse para evitar el bloqueo de las máquinas.
El lock-up (perno o rueda atascada) puede ser el resultado de varias cosas, por lo general se pueden prevenir con una operación correcta. La principal causa de los bloqueos se produce cuando los pernos o la rueda no se limpian y lubrican con regularidad.
Muchos procesadores con cambiador de malla de tipo de perno o rotatorio han comprado estas máquinas de proceso continuo porque no tienen sellos mecánicos y funcionan de forma fiable y sin fugas durante años y años. Si bien estos diseños avanzados sin duda requieren menos mantenimiento que una placa de deslizamiento, el mantenimiento durante el cambio de malla no debe ser descuidado.
Con el tiempo, el exceso de acumulación de polímero puede formar una placa sobre las superficies de los pernos o las ruedas, reduciendo los espacios requeridos y, eventualmente se requiere más presión hidráulica para su movimiento que la disponible a partir de la unidad de potencia o accionamiento mecánico.
Este perno o rueda atascada es fácilmente prevenible con la limpieza regular. Un bloqueo requiere un proceso de apagado y recalentamiento que puede tardar hasta 8 horas o más. Hacer el mantenimiento diario y la limpieza del pistón toma de 5 a 10 minutos y se puede ahorrar una cantidad considerable de tiempo de inactividad.
“El mayor problema es tener la mentalidad de la limpieza de todo el perno”, dice Marty Danco de Verity Resinas, un reciclador y fabricante de compuestos en Forest City, Carolina del Norte “Cuando se bloquea, no hay camino a casa, se cerró para siempre. El perno debe limpiarse todos los días usando una gasa de cobre adecuada, no sólo la parte superior, también en el fondo y en los lados”.
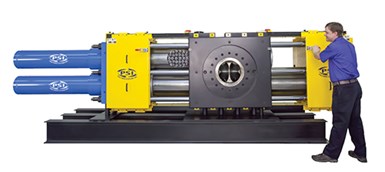
Los denominados cambiadores de malla de área extendida son adecuados para aplicaciones de extremadamente alta capacidad en la producción de compuestos y el reciclaje.
La necesidad de un mantenimiento regular también es válida para las placas rompedoras. Con el tiempo, el material se carbonizará en ellas, cerrando los agujeros, lo que aumenta la presión y finalmente compromete la productividad. La obstrucción de la placa rompedora también es fácilmente prevenible.
La mejor solución es asegurarse de tener un repuesto limpio. Intercambiando estas placas rompedoras incluso una sola vez a la semana es un gran mantenimiento preventivo para asegurar que nunca llega al punto en el que se ve afectado el proceso o el producto final.
La mayoría de los proveedores líderes en cambiadores de malla son excelentes recursos para la solución de problemas. Si lo hace, en lugar de confiar únicamente en su equipo de mantenimiento, a menudo puede reducir sus gastos de tiempo de inactividad y reparación, eliminar algunos problemas antes de que ocurran, y potencialmente le indican una solución de proceso mejor.
Contenido relacionado
Guía de limpieza para el sistema de plastificación
Todo lo que necesita saber sobre la limpieza y mantenimiento del sistema de plastificación. Descubra cómo minimizar el tiempo de parada y desperdicios en procesos de extrusión y moldeo por inyección.
Leer MásClaves del procesamiento de coextrusión en polímeros
Descubra los fundamentos y desafíos del procesamiento de coextrusión en polímeros y cómo lograr resultados óptimos.
Leer MásExtrusión y ventilación: claves para materiales compuestos
Conozca la importancia de la ventilación en la extrusión de materiales compuestos y cómo resolver problemas comunes en el proceso.
Leer Más¿Por qué y cuándo debe recristalizar su scrap de PET?
Ya sea que usted fabrique botellas de PET mediante moldeo por soplado o extruya lámina APET, producirá desechos amorfos en el proceso. El manejo que usted le dé a este material afectará sus costos de producción. La re-cristalización puede ayudarle.
Leer MásLea a continuación
Moldeo por soplado: guía completa y preguntas frecuentes
¿Está interesado en el moldeo por soplado? Conozca las ventajas, desventajas y fundamentos de este proceso de transformación de plásticos.
Leer Más¿Por qué se necesitan reglas globales para el uso de polímeros?
La legislación de la ONU tiene el potencial de reducir la contaminación por plásticos a escala mundial a través de un lenguaje firme y claro y de objetivos jurídicamente vinculantes.
Leer MásInnovación en empaques de pared delgada: tecnología y sostenibilidad
El mercado global de envases de pared delgada está en constante evolución y abarca una amplia gama de aplicaciones y materiales. En el presente artículo exploraremos este mercado, su crecimiento, tendencias emergentes, impacto de la pandemia por COVID-19 y sus proyecciones para los próximos años según un reciente estudio publicado por Mordor Intelligence.
Leer Más